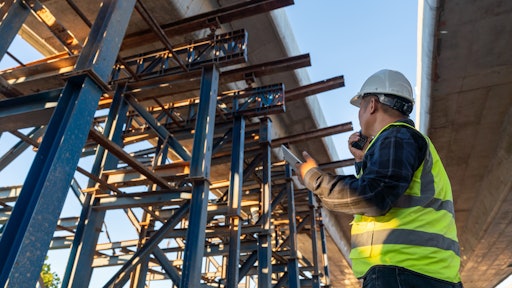
Construction work is characterized by high labor turnover, constantly changing work environments and conditions on site, and different types of work being carried out simultaneously by several contractors, increasing the health risks of workers. Your employees may be exposed to various hazardous substances and physical agents, on the construction site due to debris and dust containing lead, asbestos, and silica dust, besides sewer gases, organic solvents, radiation, welding fumes, noise, and vibration.
Being exposed to these agents is hazardous to your employees resulting in acute chronic illness, injury, permanent disability, or even death. Loss of concentration at work and fatigue due to poor health conditions may increase the risk of worksite accidents. So how do you minimize the health risk to your employees at the construction site? Here are certain measures you can adopt at your construction site to minimize the risks of health hazards:
Hazard Identification
Identify all possible health hazards that are likely to be encountered before the commencement of construction work. These hazards may occur due to the hazardous substances used, those already present on site, the environmental conditions, heat, and noise. You can obtain hazard identification information from the equipment and material supplier, site owner, and principal contractor. If not, then identify unknown substances or seek assistance from a specialist, if the need be.
Risk Assessment
Studying the conditions or hazards the workers are exposed to and determining the harm they are likely to cause, is Risk Assessment. To ensure that the workers are adequately protected, health risks at the work site should be assessed. Risk Assessment involves considering factors such as:
- Air concentration of fumes, vapors, and dust generated from the work processes.
- Effectiveness of ventilation on site to control the air contaminants.
- Probability of skin or eye contact with corrosive or irritating substances.
- Exposure of the workers to hazardous physical agents, such as noise, heat, and radiation.
- Ergonomic factors, such as repetitive tasks and manual handling.
- Immediate risks, such as being overcome by fumes in a confined space, and the long-term health risks, such as skin cancer from prolonged contact with the pitch. should be assessed.
- Review assessment when new hazardous substances and physical agents are used or when there are significant changes in the working environment.
Prevention
Once you identify the health hazards try to eliminate them completely by:
- Doing the job differently- instead of using acids or caustic soda to unblock a drain, use drain rods.
- Using a substitute- instead of using spirit-based paints, use water-based ones which are generally less hazardous.
However, always ensure that one hazard is not simply replaced by another.
Control
If prevention is not possible, try to control the risk by using control methods such as:
- Ensuring adequate ventilation in the working area.
- Using minimal amounts possible, of hazardous substances.
- Applying local exhaust ventilation to particularly hazardous processes, such as rock cutting, grinding, and welding.
- Using water suppression to control dust emission.
- Segregating hazardous processes so that indirectly involved workers are not affected.
- Taking administrative measures, such as providing sufficient safety and health training, appropriate supervision, good personal hygiene instructions and information to the workers, and good housekeeping.
- Providing exhaust ventilation in work areas where natural ventilation is insufficient.
Personal Protective Equipment
The following Personal protective equipment should be provided if the above combination of measures fails to prevent exposure:
Respiratory equipment for protection against specks of dust, vapors, or gases.
Protective clothing, such as overalls, boots, and gloves for protection against irritating and corrosive substances, abrasion, and vibration;
Eye protectors for protection against chemical splashes, such as goggles or face visors.
PPE should be selected with care and a personal protective equipment program, including selection, maintenance, user training, and supervision, should be set up to ensure the effectiveness of the personal protective equipment.
Medical Surveillance
Medical surveillance is a system of monitoring the health status of workers engaged in hazardous occupations, to detect early signs of illness so that intervention may be taken to prevent permanent health damage. Useful for occupational illnesses with long latent periods, like silicosis and occupational deafness, this examination should be done by an occupational medicine expert. Workers engaged in hazardous occupations should undertake pre-employment and periodic medical examinations because they may have prolonged exposure to high concentrations or levels of hazardous substances and physical agents.
Types of Health Hazards
There are three types of health hazards in the construction industry- chemical hazards, physical risks, and ergonomic hazards. While chemicals can affect the body via inhalation, ingestion, or skin absorption, Physical hazards include noise, heat, vibration, and radiation. Ergonomic hazards mainly include manual handling of loads.
- Silica dust: A lot of building materials, like natural stone, bricks and concrete contain silica which the workers are widely exposed to. Any process involving breaking, crushing, or grinding of such materials will generate silica dust. High-risk workers include drillers, operators of pneumatic breakers, and masons. Excessive dust exposure for prolonged periods can lead to silicosis, i.e. lung fibrosis, causing difficulty in breathing. The risk is highest in confined spaces with poor ventilation, such as caissons and tunnels. Water suppression, and engineering control measures should be used. Otherwise, adequate and suitable respiratory protective equipment should be provided and worn by workers at risk.
- Lead dust: Handling materials containing lead or its compounds, leaded paint removal, and metallic lead handling may give rise to lead dust. Dismantling tanks containing lead compounds and hot cutting give rise to lead fumes. Excessive exposure may have acute or chronic health effects, especially on welders and flame-cutting operators. The nature and degree of exposure to lead should be assessed, appropriate measures to control the exposure taken, the workers informed of the risks involved, and washing and changing facilities should be provided by contractors.
- Asbestos dust: Asbestos causes asbestosis or diffuse fibrosis of the lung, mesothelioma or cancer of the lining of the chest and abdomen, and lung cancer, the risk is further increased by smoking. Disturbing of materials such as sprayed asbestos coatings, thermal and acoustic insulation materials, fire-resistant walls and partitions, asbestos cement sheets and flooring materials, and demolition work on asbestos insulation can generate asbestos dust. Before the commencement of demolition work, these materials should be removed and disposed of in accordance with the Environmental Protection Department requirements with adequate worker protection by competent asbestos contractors.
- Gases, vapors, and fumes: Gases, vapors, and fumes can be released from a variety of processes, including:
1. Welding and flame cutting
2. Using internal combustion engines and LPG burners
3. Burning of waste materials
4. Painting, especially paint spraying.
5. Using adhesives and thinners.
The harmful effects, whether short-term or long-term, depend on the types, toxicity, and concentration of the gas and vapor present in the working environment. These include oxygen deficiency, and inhalation of toxic or inflammable gases like methane, carbon monoxide, and hydrogen sulfide. Adequate ventilation and respiratory PPE must be provided where required. Extra precautions should be taken if entry into a confined space is required, during the course of work. A safe system of work for the operation in a confined space should include, a risk assessment, appropriate safety precautions, use of personal protective equipment, emergency procedures and training, and monitoring for hazardous contaminants, before entering a confined space.
- Other chemicals: Many substances involved in construction work harm the skin including mineral oil or pitch causing skin cancers on prolonged contact, disinfectants, bleaches, solvents, oils, acids/alkalis causing irritation, nickel, acrylic resins, epoxy resins, formaldehyde, cobalt, chrome, natural gums, vegetation, and timber causing allergic reactions. If skin contact with these substances is unavoidable, suitable protective clothing and gloves should be worn. Hand washing after work and skin care can prevent dermatitis, but never use solvents to clean hands or other body parts.
- Noise: High noise levels can cause difficulties in speech communication, distract concentration, and increase the risk of accidents with long-term exposure to excessive noise causing permanent hearing damage. Construction plants, such as compressors and concrete breakers create very loud noise levels, hence exposure to noise should be assessed and controlled at source using engineering controls. If it is not possible, then suitable hearing protectors must be worn.
- Ionizing radiation: Used for detecting weakness of metal structures on a construction site, previously stored or used radioactive substances may be released in demolition of buildings exposing workers to Ionizing radiation increasing the risk of developing cancer and genetic disease. Thus, a recognized safe system of work such as isolation, segregation of workers, installing warning notices and signs (Trefoil signs), monitoring, and decontamination must be used. If in doubt, seek advice from the Radiation Health Unit, Department of Health.
- Vibration: Vibration from the use of hand-held power tools such as pneumatic breakers and disc grinders may cause carpal tunnel syndrome. The disease affects the fingers and hands and permanent damage to the nerves resulting in a loss of the sense of touch and dexterity. Hence, anti-vibration gloves should be worn and low-vibration tools should be used wherever possible, and be appropriately maintained to correct balance and avoid loose parts.
- Heat: Working under direct sunlight for long hours in summer without precautions may cause heat cramps, heat exhaustion, heat rashes, and even heat stroke. Impermeable protective clothing worn when undertaking heavy work or working in an enclosed area with a strong heat source, poor ventilation, and high humidity may aggravate the problem. Underground work, removal work for asbestos insulation, and maintenance of boilers are some examples. Avoid heavy manual work in a hot environment, doing it by mechanical means or in cooler parts of a day or season, providing shelter, blowing fans, adequate cool drinks to replace the water loss as sweat, and sufficient rest breaks are some of the best strategies to prevent heat stress.
- Manual Handling: Manual handling is one of the most common causes of injury at work resulting from carrying out lifting operations for a long period, and even a single bad lift can cause pain and disability for a lifetime. OSHA requires a preliminary assessment of all manual handling operations before work commences, and avoids the need to undertake hazardous manual handling operations as far as possible. Where avoidance is not possible, a further assessment must be made, and mechanical aids or team lifting provided to reduce the risk of injury.
Thus, the above measures if taken meticulously can minimize the health risk to your employees at the construction site, thereby preventing your loss of reputation, production, and money in terms of liabilities and compensations.