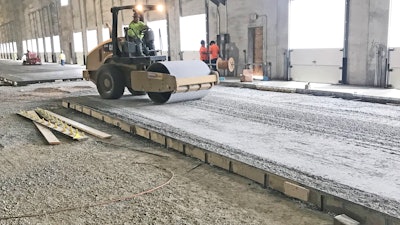
The concrete slab can be thought of as the wearing cap for the building pad and base course. A well compacted and smooth subgrade is critical to a successful slab. Slab formwork, jointing details, vapor barriers and reinforcing must be installed correctly for the slab to function as designed.
Building Pad and the Base Course
Typically the building pad and base course will be designed based on a local soils report and installed by the site contractor. A third-party inspecting agency normally will monitor installationMesh being pulled during concrete placement.Chad S. White
Major considerations when installing base course for slabs on grade:
- Uniform slab thickness and correct elevation.
- Correct concrete yield for slabs placed. We have always strived to maintain a 1% overage for slabs on grade.
- Adequate compaction and surface smoothness to reduce under slab restraint and insure correct slab profile.
- Proper backfill and compaction of excavations for plumbing and electrical lines, which should always be 2 in. to 4 in. below top of subgrade.
- Trimming and detail of base course at slab edges, walls and columns.
Grading Tips
- Control rolldown and compaction. Depending on base course thickness, local aggregates, moisture content, pad condition and grading/compacting equipment used, the difference in elevation of the base course can vary considerably from machine graded to final compacted base. Rolldown will vary daily and within slab placement area.
- Know when to use static roll. Once the placement area has been graded and compaction/proof roll approved, do only static, (non-vibratory) rolling/compaction for touch up grading before and during concrete placement. Do not vibratory compact next to fresh concrete, (under seven days in age) as a rule of thumb.
- It’s easier to bring material in than take it out. We recommend that building pad be +/- 1/10’ balanced prior to installation of base course.
Slip Sheets and Vapor Barriers
A slip sheet is a layer of material (usually15 mil vapor barrier in place.Chad S. White
Vapor barriers are materials that will minimize the transmission of water vapor from the subgrade into the concrete slab. Vapor barriers are typically specified according to ASTM E 1745. Low density polyethylene film is commonly used, and a minimum thickness of 10 mils is recommended for reduced vapor transmission and durability during and after its installation.
Sometimes a granular blotter layer is specified between the underside of the concrete slab and the vapor barrier. Be advised that a blotter layer is generally not recommended due to the potential of water ponding under slab and being trapped by the vapor barrier.
There are several major considerations when installing slip sheets and vapor barriers, including:
- Insure base course is smooth prior to installation.
- Protect from puncture and abrasion.
- Overlap edges correctly. Install per manufacturers recommendations. Vapor barriers will require taping of joints and special attention at penetrations, block-outs and walls.
- Keep clean.
Additional Installation Tips
- Double check that correct vapor barrier materials and thickness is being used.
- Keep material flat and wrinkle free during installation of concrete.
- Have additional material and repair items available during concrete placement.
Slab Forming, Jointing and Reinforcement
For the purpose of this article we will be discussing conventional slab edge and column block-out formwork solutions, the different doweling systems currently in use and light slab reinforcement installation.
Slab Forming Solutions
Dimensional lumber is the most common Slab edge forming with dowel pocket formers installed.Chad S. White
Major considerations for installing formwork for concrete slabs:
- Maintaining top of slab elevation, FF/FL specification and joint straightness requirements.
- Form to form joint and support.
- Understand bracing requirements for system used and soil conditions to be encountered.
- Consider reuse and stripping/cleaning requirements for the forming system used.
- Is it “finisher friendly”? Are the stakes/braces below top of form? Is top of form beveled? Can a troweling machine safely overlap edge? Is there adequate room for workman to access edge of slab?
Tips for Installing Formwork
- Stack and store forms properly.
- Use good lumber and accessories.
- Minimize hand grade trimming under forms.
- Control benchmark. Third party survey crews will typically establish monuments and control points but temporary benchmarks will need to be transferred as concrete slab installation progresses and maintained for prep, forming and concrete placements. We would recommend all benchmarks be established, moved or transferred using an optical level in lieu of a laser.
Slab Jointing/Doweling
Slab dowels and rebar at construction jointsPlate dowels installed prior to placement.Chad S. White
Major considerations for installing construction joint dowels, rebar and dowel baskets:
- Dowel alignment and straightness.
- Ability to consolidate concrete around and ease of form stripping.
- How dowel baskets will be installed and maintained during slab placement.
- Having enough material on hand and proper storage.
Tips for Installation of Dowels and Dowel Baskets
- Read the installation
instructions for any proprietary doweling systems used and the plan details. So basic but oftentimes neglected.Plate dowel baskets being installed during placement.Chad S. White
- You can’t just put the dowels in and leave it. Someone must be responsible for monitoring dowel installation and correcting dowel displacement during placement.
- Straight lines, straight lines, straight lines.
Slab Reinforcing
Reinforcement categories to be covered is mesh, rebar and fibers. Mesh is generally specified for light commercial projects, slabs on metal deck and as a work platform during installation and placement of structural slabs. Reinforcing can run the gamut from light # 3 rebar on wide spacings to double layer closely spaced mats of # 6 rebar. Fibers can be either steel or plastic of various lengths and configurations with different poundage requirements per cubic yard of concrete specified.
Mesh and rebar are typically chaired andSingle layer rebar mat chaired in place.Chad S. White
Major considerations when installing mesh, rebar and fibers:
- For mesh and rebar insure that overlap and wastage is accounted for when ordering.
- Stability of subgrade when selecting chairing method.
- Interface with placing operations. Method of concrete placement will impact rebar installation sequencing and bar support/chairing requirements.
- How you are going to get the fibers in the truck and where.
Tips for Installing Mesh, Rebar and Fibers
- Mesh is difficult to chair in place and hand
pulling of mesh as a supplemental method of installation is recommended.Steel fibers being loaded onto conveyor.Chad S. White
- Rebar mats are easier to manage than individual bars tied in place.
- Understand shop drawings and plan details.
- Try to eliminate or minimize personnel climbing up and down the back of truck mixers while loading fiber.
- Insure that fibers are loaded correctly into mixer trucks and properly mixed prior to discharge.
Slab Protection and Housekeeping
Primary concern is protection of work in Columns shrink wrapped and end wall protected during concrete placement.Chad S. White
Concrete splatter, dirt and staining are major worries that must be addressed. Hot and cold weather protection activities may be required and access to slabs during curing period will have to be monitored and controlled.
Chad S. White has been involved in all aspects of concrete construction from craftsman to concrete subcontractor and is a founder of WL Concrete. He has been personally involved with design and construction of many industrial slabs, including shake-on hardeners, defined traffic super flats and high tolerance random traffic floors. White is the author of numerous published articles regarding concrete slab on grade installation and a speaker at World of Concrete.
References:
ACI 302-IR-04: Guide for Concrete Floor and Slab Construction
ACI 302-2R-06: Guide for Concrete Slabs that Receive Moisture-Sensitive Flooring Materials
ASTM E1745-11: Standard Specification for Plastic Water Vapor Retarders used in Contact with Soil or Granular Fill under Concrete Slabs
ASTM E1643-11: Standard Practice for Selection, Design, Installation and Inspection of Water Vapor Retarders used in Contact with Earth or Granular Fill under Concrete Slabs
More Resources
How To Reinforce Concrete Slab on Ground to Control Cracking
Controlling Cracks in Slabs with Unusual Panel Geometries
Acceptable Tolerances for Residential Basement Slabs
How to Finish Flatter Concrete Floors
Avoid Surface Defects on Exterior Slabs
Standing Water in Prepared Footings: A Problem or a Precaution?