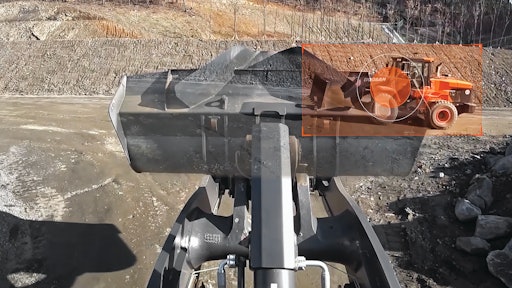
Awareness and visibility are two of the major safety considerations when operating a wheel loader. “A wheel loader is often moving in forward and reverse in its normal work pattern. The ability to see and be aware of your worksite is paramount,” says Aaron Kleingartner, product and dealer marketing manager, Doosan Infracore North America. This can be accomplished in a variety of ways, including with mirrors, cameras, radar and the machine design.
“Visibility on any piece of large mobile equipment is always a concern,” says Juston Thompson, wheel loader product manager, Hyundai Construction Equipment. “Reducing blind spots by use of mirrors, rear view cameras, observation systems or radar are the best options to mitigate risk. Hyundai wheel loaders feature rear view cameras as standard equipment. The camera provides a wide field of view to maximize the visibility behind the machine.”
Anything you can do to increase visibility around the machine benefits jobsite safety. “To put it in simple terms, better visibility means safer jobsites and employees, and cameras help to enhance visibility,” says Eric Yeomans, product manager, wheel loaders, Volvo Construction Equipment. “That’s why Volvo offers rear view cameras that display on the Co-Pilot in-cab tablet. Radar detect systems are another great technology that can help prevent collisions. Our rear view cameras can be integrated with a radar detect system that gives visual and audio warnings when in reverse or near objects. These features combine to provide maximum visibility for the loader operator.”
Doosan has featured rear view cameras as standard on its wheel loaders for quite a number of years and is now simplifying the system to further enhance visibility. “Up until our Dash-7 wheel loader launch, it was a separate monitor,” notes Kleingartner. “With our Dash-7 Series, that monitor is integrated into the standard display.” The fewer monitors in the front of the cab, the better the operator visibility out of the front. “There’s actually less area that’s potentially covered with front visibility by another separate monitor for a camera.”Doosan integrates the rear view image into the standard display, reducing distractions in the cab.Doosan Infracore
Camera technology has not replaced the need for functional mirrors. “We also continue to offer rear view mirrors,” says Kleingartner. “There’s a mirror in the cab as well as two external on the machine. The option is either a standard mirror or an electric heated mirror... Both the left and right are electronically adjustable as an option from within the cab. If it needs to [be adjusted] regularly to see your jobsite better, or if you have different operators coming in and out of the machine that have a lot of variability in size, they can change those mirrors very easily from inside the cab.”
Heated mirrors are more than merely a convenience. “In combination with the standard rear view camera, we include heated mirrors with a convex mirror section to provide maximum visibility,” says Thompson. “Heated mirrors can quickly remove moisture from the surface rather than the operator climbing up on a machine risking a possible fall accident.”
Be sure to sit in the cab of any wheel loader you plan to purchase and note its all-around visibility. Some of the latest designs provide better sightlines to the areas around the loader, especially toward the rear.
“We have been able to keep the envelope of our machine relatively small and compact,” says Kleingartner. “As you look out the window you have great visibility.” The latest Doosan loaders do not require the space-consuming DPF to meet emissions requirements. “That allows the exterior envelope of the machine to be smaller. The cooling packages can be a little smaller as a result. We don’t have that as an impediment to visibility.”
Delivering More than Rear View Visibility
While rearward visibility should be a focus on any mid-size and larger wheel loader, you also need to be able to track traffic moving around the jobsite and be aware of objects that can be obscured by front attachments and buckets.
Volvo has made it easier for operators to keep an eye on jobsite traffic. “A recent update to Load Assist is the Map application,” says Yeomans. “It allows operators to monitor site traffic in real time so they can proactively adjust their driving behavior according to the conditions around them, making everyone safer and more productive.”Volvo has made it easier for operators to keep an eye on jobsite traffic with a Map application for its Load Assist technology. It allows operators to monitor site traffic in real time so they can proactively adjust their driving behavior according to the conditions around them.
Cameras also do more than provide rearward visibility. Liebherr offers a roof camera that extends the operator’s field of vision. When working with large attachments, it ensures better and quicker recognition of people and obstacles in front of the machine.
“The front monitoring camera assists in providing an extended field of view for the operator,” says Nick Rogers, product specialist, Liebherr USA. “With the addition of the roof-mounted camera, the operator can identify possible sources of danger on a separate display.”
Doosan has found a unique way to utilize the camera technology found in the most recent automotive applications. It recently introduced a transparent bucket option for all Dash-7 Series models.
“Wheel loaders have traditionally been workhorses on the jobsite where all of your work is done with the attachment on the front of the machine,” says Kleingartner. “That attachment very often impedes front visibility.” In the case of stockpiling, this means visibility would be restricted to the edge of pile. In the case of loading into a hopper or a truck, visibility to the edge of the hopper or box would be restricted.
“The transparent bucket technology uses multiple cameras on the machine to give you a stitched overlay of those camera views to make that bucket virtually invisible,” Kleingartner explains. “It is designed to improve safety and productivity. Especially if you are coming up a ramp to a blind dump, you have a better view of exactly where you are so you can hit the middle of the target every time and be more productive.”
Proper lighting is also critical for optimal visibility. “Our machines now come standard with LED work lights,” says Kleingartner. “We have various different options available to add additional lights.” The standard machine comes with two lights on the front and two on the rear. “You can add up to eight more on the machine. So, if you need additional side lighting or directional lighting, you can add up to four more on the front and four more on the rear.LEDs provide a wider area of light versus a lot of the halogen technology, which is very pinpointed at times. Doosan loaders can be equipped with up to 12 LED lights to light up the working area around the machine.Doosan Infracore
“LEDs provide a wider area of light vs. a lot of the halogen technology, which is very pinpointed at times,” he adds. “It really lights up the entire worksite when you have all 12 of those lights on... It uses less energy and it provides better visibility around the worksite.”
Ground Worker Awareness
Visibility is a two-way street. Not only must the operator be able to see everyone and everything around the machine, the ground workers must also be aware of and have “visibility” of the machine.
Backup alarms are the most common safety device utilized to alert ground workers. But workers can become complacent from hearing these alarms constantly going off every day.
“Our new Dash-7 machines also have a strobe light on the rear of the machine,” notes Kleingartner. “That is a visual indicator of the machine backing up right in the top of the rear cowl.” Two mini white lights positioned in the rear grille will strobe slightly as the machine is going in reverse.
“There is a new backup technology that uses a different form of noise that isn’t the beeping alarm because everybody has become agnostic to it,” Kleingartner adds. “It is not a warning anymore. There are other technologies out there that help with that, as well.”
Volvo offers more visibility to ground crew and supervisors, as well. “Because we place such a high priority on safety, we also have an external seat belt indicator light, which allows all site staff to see that the operator has the seatbelt engaged, meaning [the machine] could move at any time.”
Prevent Slips and Falls
Slips and falls are always considerations when working around taller machines.
“The most common safety concern on any construction equipment is a slip-and-fall accident, which is why maintaining three points of contact is critical (two feet and a hand or two hands and a foot),” says Yeomans. Volvo also uses visual cues for operators. “The orange color visually enhances handrails and steps, helping them stand out against the standard machine colors. Volvo wheel loaders include orange ladders, railings, three-point seatbelts and more because that color makes those safety points harder to forget. It also makes the operator and/or machine more visible to others around the jobsite.”
Doosan offers a new handrail option all the way around the cab on new Dash-7 wheel loaders to provide safety when operators are cleaning the windshields.
Another way to reduce slips and falls on the jobsite is to provide proper lighting when entering the machine. “The remote door opener combined with the entrance light is a great safety feature,” says Yeomans. “Remotely opening the door from ground level (with or without the key) and activating the cab entrance light provides the operator a safe and convenient entrance, especially when it is dark. It also keeps the operator from climbing the ladder and opening the door at the same time, thus maintaining three points of contact.”
Liebherr offers a key with remote control, including a “coming home/leaving home” function that enables the operator’s door to be locked, unlocked and automatically opened remotely. In addition, the working lights on the sides of the wheel loader light up the area of the machine to ensure the operator can get on and off safely and quickly.
Many manufacturers offer ground level service, which helps prevent slips and falls by keeping the technician’s feet firmly on the ground. There is no more crawling over the machines to access service points.
Collision Prevention Continues to Advance
Collision prevention technologies have taken hold in the automotive industry and are quickly expanding into the construction machinery realm.
“There are technologies on the horizon, like we have displayed with Concept X, where the machines are using radar and lidar to detect objects and potentially stop the machine whether there is an operator in the seat or not,” says Kleingartner.
An example of these advanced safety technologies includes Hyundai’s All-Around View Monitoring (AAVM) system. The AAVM system was developed for HX Series excavators in 2015 and was adapted for the HL900 Series wheel loaders in 2018. Equipped with four cameras — including one each mounted on the left- and right-side mirrors, one on the front of the cab and the standard backup camera mounted to the rear hood — the monitoring system provides a 360˚ surround virtual operating view of the jobsite.The Hyundai AAVM utilizes four cameras to stich together a 360-degree view around the wheel loader. It can be couple with an Intelligent Moving Object Detection (IMOD) system.
The AAVM system includes Intelligent Moving Object Detection (IMOD), which senses and warns the operator with on-screen flashing arrows and an alarm when objects come within either of two selectable ranges (6.5 ft. or 22.9 ft.) of the wheel loader. The image is integrated into the 7-in. color touchscreen cluster-monitor in the cab.
“It will tell if an object is within a certain range of the machine by different colored arrows, whether it is to the rear or the sides of the machine,” says Thompson. “There are different angles and views that they can select. If the operator is going to be really concerned about something to the right side, they can select it to where the primary detection is to the right-hand side of the machine. When an object is actually moving inside of that field of vision, it is going to circle it with a box and tell you that you have something moving within your area, so you need to be careful. It will give them an audible alarm to let them know that something is in that area.”
Hyundai continues to add collision mitigation technologies. “New for the A Series, we have also added a radar option,” says Thompson. “There is a radar monitor on the back of the machine.” This gives the contractor several options. The rear view camera is standard. “Then, you can add radar with a second monitor, you can add AAVM or you can add radar and AAVM.”
To increase safety, Liebherr offers optional intelligent assistance systems for its XPower wheel loaders. The systems, which are fully integrated into the machine’s control, include Adaptive Working Lighting, Active Personnel Detection at the Rear, a Roof Camera for Front Area Monitoring, Integral Tire Pressure Monitoring, Key with Remote Control and Skyview 360.
“The adaptive working lighting is an intelligent light control system that adjusts the brightness of [LED] headlights according to the position of the lift arms, the working attachment and the wheel loader’s articulation angle,” says Rogers. “This system is fully automated, only activating the various lighting components when they are needed.Liebherr also offers intelligent assistance systems that increase safety, which are options on its XPower wheel loaders. These systems are fully integrated into the machine’s control. The systems include Adaptive Working Lighting, Active Personnel Detection at the Rear, Roof Camera for Front Area Monitoring, Integral Tire Pressure Monitoring, Key with Remote Control and Skyview 360.Liebherr
“The system incorporates additional lighting on the front section of the vehicle, and automatic dimming of the front working headlight ensures the operating area is ideally illuminated at all times,” he explains. “This reduces reflections off of the working attachment and shadows around the operating area, producing ideal visibility conditions to ensure a high level of safety.”
The active personnel detection system monitors the rear area of the wheel loader and automatically warns the operator of dangers by means of a visual symbol on the display and an audible signal.
“Another aid for avoiding collisions is the brake assistant, which is automatically applied if the operator does not react fast enough to the audible and visual warnings,” says Rogers. “The system utilizes the latest camera technology, incorporating stereoscopic monitoring and cutting-edge AI to distinguish between people and objects without people needing to be equipped with transponders or sensors.”
If a person is located in the shunting area of the wheel loader, the intelligent systems alert the operator earlier than if a static object is detected. This reduces unnecessary warning signals and the resulting strain on the operator. The targeted warning with supporting braking function helps prevent personal injury and reduces the risk of accidents.
“The active personnel detection system also reports into the Liebherr Telematics portal (LiDAT), providing an intuitive incident mapping feature to easily track hot-spot areas on jobsites that need to be addressed,” notes Rogers.
Skyview 360 provides the operator with a continuous 360˚ view around the wheel loader. Four cameras capture the machine’s environment. The resulting images are compiled into a bird’s-eye view, which is displayed on the in-cab display. This eliminates blind spots and allows operators to quickly identify potential dangers.
In addition to eliminating blind spots and enhancing visibility, there are other safety considerations when purchasing a wheel loader, such as the structure of the cab.
“Look for equipment where the Roll-over Protective Structures (ROPS) and Falling Object Protective Structures (FOPS) are standard,” says Yeomans. “The main goal of ROPS/FOPS is to provide protection to the operator in case of a roll-over accident or falling objects, respectively. A fire suppression system is another key feature to have.”
Being able to set defined speed limits is a benefit on many jobsites, as well. “With the programmable speed limit setting within the monitor, we can control the maximum speed at which the loader can travel,” notes Hyundai’s Thompson.