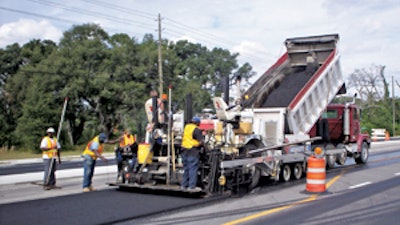
If you're not convinced how a high RAP mix design can work for you and your road agency customers, you need to take a look at what Daytona Beach, FL-based P & S Paving has been able to do with its aggressive RAP content proposals, and do so to the delight of its Florida Department of Transportation (FDOT) customer.
P & S recently completed the third segment of the State Road 15A reconstruction project north of DeLand, FL this past fall, placing 14,099 tons of Superpave Traffic Level C base and binder course mix designs containing 45 percent fractionated RAP. This two-mile segment was the third of a four-phase projectto convert the two-lane truck route into a four-lane divided highway.
P & S was awarded and completed the first two phases of the project in 2004 and 2005.
As the general contractor on the project, P & S performed all grading to expand the two-lane road into a divided four-lane highway, placing all the crushed rock subbase and then paving the approximate eight lane miles of new road surface. Bechtol Engineering and Testing Inc. of DeLand was hired by P & S to perform the quality control and quality assurance (QC/QA) requirements of the project.
The 45 percent fractionated RAP base and binder courses, which were composed of 12.5 mm and 9.5 mm recycled and virgin aggregate material respectively, were QC designed by Bechtol and produced at P & S's Daytona Beach HMA production facility. Following placement of the recycled base and binder courses, P & S then produced and placed 8,261 tons of virgin friction course (FC12.5mm TLC) to complete the project.
RAP production
P & S has been fractionating (separating by size) RAP since 2002. In late 2004, the asphalt producer/contractor installed a completely self-operating, closed-loop RAP processing facility. When the system is operating, the manpower required is for a loader operator to deposit RAP into a 42-inch by 16-foot Telsmith vibrating grizzly feeder. Once the material enters the Astec system, it passes over two screens — one a ¼-inch by 6-inch slotted screen for fine product, and one a 5/8-inch by 6-inch slotted screen for coarse product. Any oversized material is transferred back to the crusher until it is sized correctly and can be deposited into one of two piles — ¼-inch minus fines and ¼- to ½-inch coarse material. The system allows the asphalt producer to separate road millings back to the specific dimensional size of virgin aggregate without excess crushing, which would only create additional problematic fines that have to be controlled in producing a quality mix design.
For P & S, the fractionating system allows the producer to process recycled pavement and incorporate it into new mix as it would with virgin material. Mix content can be quantified since the processed fractionated RAP is aggregate with a black coating. The ability to quantify the contents of a mix design not only satisfies FDOT's Producers Quality Control Plan, which requires a high-frequency screen deck capable of maintaining 3,600 rpm in order to qualify as fractionated RAP, but also reduces the material, both aggregate and liquid asphalt cement binder, costs for the P & S.
"We produced 400,000 tons of mix this year (2006) and the fractionating process gives us a lot of flexibility in maintaining control over the mix content during production," says P & S President Tim Phillips.
In order to control the quality of the fractionated RAP used in its mix production, P & S processes RAP on a just-in-time basis. Having only enough processed FRAP (fractionated reclaimed asphalt pavement) on hand for a day's production prevents the stockpiles of FRAP from excess exposure to the hot Florida sun, which can actually harden the material, as well as preventing the piles from getting wet, which cuts down on drying costs. P & S conducts daily quality-control tests on its FRAP to verify volumetrics and viscosity, with reports sent to FDOT.
Additional QC measures for mix designs with high RAP content call for increased testing frequencies of the extraction/gradation test and recovered viscosity. The QC plan for the SR 15A project also included additional tests for determining the maximum specific gravity (Rice Method) of the mix design; and the bulk specific gravity (Gsb) was also regularly monitored as well.
One other measure P & S has taken to ensure a high-quality FRAP mix design is produced at the plant is the modification it made to its Astec Turbo 400 Double Barrel control system. The modification allows better control of the drum speed in order to control aggregate veil. This provides for more efficient heating of RAP without increasing baghouse temperatures.
Whenever mix adjustments are required during production, using the fractionated RAP allows the percentage of RAP content to be maintained by simply adjusting the ratio of the two FRAP components (fine and coarse), rather than decreasing the overall RAP and increasing the virgin material, which is the only way to make adjustments when using non-fractionated RAP.
A winning solution
P & S has always taken a progressive approach in identifying and implementing ways to grow its business while maintaining a competitive edge in the market. It didn't take long for the company to rapidly grow its road construction business from a single dozer operation in 1993 to the $60 million company it is today. Expansion into asphalt production, asphalt paving and asphalt milling have all contributed to the methodical approach brothers Tim and Todd Phillips have taken in a commitment to make the company what is today.
So it comes as no surprise that the Phillips have also taken a progressive approach in investing in state-of-the art equipment to expand their production and competitive capabilities, while generating a profitable return at the same time.
P & S purchased a used batch plant in 1998 to expand it construction services into the production and placement of hot mix asphalt. The Phillips soon recognized the potential of the HMA market within the 60-mile radius of their Daytona Beach production facility and decided to replace the aging plant with a state-of-the-art Astec Turbo 400 Double Barrel drum-mixer plant in 2001.
When the plant was fired up in January 2002, the Phillips soon realized they were in the asphalt business and the annual production rates quickly grew. At the same time, increased usage of RAP on FDOT projects also piqued the Phillips' interest, especially with the growing piles of road millings that were beginning to take over their production area.
"We've used RAP ever since we bought the batch plant, but it was on a very limited basis," says Pat Richards, paving operations manager who's been with company from the start. "Before we began fractionating RAP (somewhere around 2002), we were able to incorporate 30 to 35 percent in some of the mixes we were producing.
"Now with our RAP system, we can produce FDOT designs with as much as 50 percent RAP and some other designs for road base work with up to 60 percent," he continues. "What the fractionating system does for us is it gives us the exact same product that we would pull from our virgin aggregate piles, except that the RAP product has a coating of asphalt."
For the SR 15A project, the requirements are the same as with any other FDOT project that's built with RAP mixes or not. Standard FDOT density requirement and smoothness specifications had to be met.
"Even though every mix you produce might be a little different and the conditions during placement may call for different rolling patterns to achieve density and ride quality, the high RAP mixes still perform as well as virgin mix designs," Richards says. "We know the designs work and FDOT knows they work. The entire 15A project is a warranty project, so we're pretty confident of the long-term performance of the job."
Sixty percent of the mix P & S produces and places today is for FDOT, so the relationship the asphalt producer/contractor has built with the road agency is a strong testament of the mutual respect that exists.
"Using a high percentage of RAP in mix designs allows us to control our costs and be more competitive in the bid process. At the same time, we've proven that those designs perform up to FDOT's requirements and we have the quality control measures in place to verify the quality of the mixes we're producing and placing," Richards says.
P & S Paving maintains stockpiles of approximately 600 to 700 tons of fractionated RAP to meet daily HMA production needs. The company has another 160,000 to 180,000 tons of pavement millings available for future processing.
"We have an I-4 project coming up and we'll be using a lot of fractionated RAP in the new pavements we put down," Richards says. "We consider RAP to be very valuable material resource and we'll continue to use as much as we can depending on what a project will allow. It just makes sense to use good material that's readily available. It's good for our company and it's good for our customers."