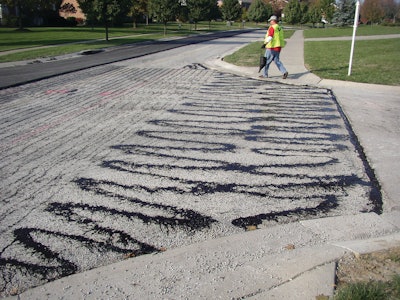
To determine the application rate for an asphalt emulsion tack coat, it is absolutely necessary to start with the residual asphalt content – the amount of asphalt binder remaining on the pavement surface once the water in the emulsion evaporates. If, for example, it has been determined that a residual asphalt content of 0.04 gallons per square yard (gal. /sq. yd.) is needed, an application rate of 0.06 gal. /sq. yd. should be delivered from the asphalt distributor. This calculation is based on a ratio of two-thirds residual asphalt binder and one-third water in the asphalt emulsion and is done by multiplying the residual asphalt content by a factor of 1.5 to determine the required application rate (as discussed in “How a Tack Coat Improves Your Paving,” in the May issue of Pavement Maintenance & Reconstruction).
If the residual asphalt content of the asphalt emulsion was required to be 0.06 gal. /sq. yd., for example, the emulsion application rate from the distributor would be approximately 1.5 times as great, or 0.09 gal. /sq. yd. (0.06 x 1.5 = 0.09). Similarly, if the required residual asphalt content was 0.05 gal. /sq. yd., the application rate from the distributor would be 1.5 times as great, or 0.075 gal. /sq. yd.
In some cases, it is advantageous to dilute an asphalt emulsion in order to achieve a more uniform application of the residual asphalt binder in the emulsion on the pavement surface. The usual dilution ratio is 1:1 – one part water is added to one part emulsion. This means that the original emulsion makes up only 50 percent of the diluted emulsion. It also means that only one-third of the diluted emulsion will actually be residual asphalt binder – two-thirds will now consist of water. The water used to dilute the emulsion must be potable – suitable for drinking.
It should be noted that only slow setting emulsions can be diluted with water. When a slow set emulsion is diluted, the water is added to the emulsion – not the emulsion to the water. Adding the emulsion to the water might cause the emulsion to break and cause water and the asphalt binder to separate. A diluted emulsion will typically take longer to set than will an undiluted emulsion under the same environmental conditions, thus possibly delaying the placement of the hot mix asphalt mix.
For an emulsion that is diluted 1:1 with additional water, for a required residual asphalt content of 0.04 gal. /sq. yd., it would be necessary to apply the diluted asphalt emulsion at a rate of 0.12 gal. /sq. yd. from the asphalt distributor. This application rate is calculated by multiplying the residual asphalt content by a factor of 3.0 to determine the required application rate of the 1:1 diluted emulsion.
If the residual asphalt content was required to be 0.06 gal. /sq. yd., for example, the application rate of the diluted emulsion would be approximately 3 times as great, or 0.18 gal. /sq. yd. (0.06 x 3.0 = 0.18). Similarly, if the required residual asphalt content was 0.05 gal. /sq. yd., the application rate of the diluted emulsion from the distributor would be 3 times as much, or 0.15 gal. /sq. yd.
It is very important to note that it is the residual asphalt content in the emulsion that is the key to the tack coat performance. If a distributor operator applies an undiluted asphalt emulsion tack coat at rate of 0.10 gal. /sq. yd., the amount of residual asphalt will be approximately 0.066 gal. /sq. yd. If a distributor operator applies an asphalt emulsion that has been diluted 1:1 with water at the same application rate, 0.10 gal. /sq. yd., however, the amount of residual asphalt will be only 0.033 gal. /sq. yd. This reduced residual amount most likely will not provide adequate performance. The application rate of the tack coat should always be calculated by starting with the required residual rate and working backward to determine the application rate.
The distributor operator must know the type of material being used and, if an asphalt emulsion is being used, whether the emulsion has been diluted or not. In addition, he or she must know what the residual asphalt content is supposed to be and then back-calculate to determine the application rate of the emulsion from the distributor. Unfortunately, many distributor operators simply do not know whether the emulsion has been diluted or not or know how to determine the application rate and/or the residual rate for the tack coat material. If pure asphalt binder is used for the tack coat, the application rate from the distributor spray bar and the residual rate on the pavement surface will be exactly the same.
Asphalt Application Temperature
Proper tack coat application begins with the asphalt distributor (shown in Figure 1) used to deliver the tack coat material to the existing pavement surface. The tack coat material in the distributor tank must be kept at the proper temperature to assure that the material can be sprayed uniformly onto the existing pavement surface. When an asphalt emulsion is used, it should normally be applied at a temperature between 120oF and 160oF. When an asphalt binder is used, it should normally be applied at a temperature between 275oF and 325oF. It is very important to have the tack coat material at the proper application temperature in order to obtain a uniform distribution on the existing pavement surface.
Spray Bar Nozzle Size
Uniform tack coat application also depends on the size of the nozzles used on the distributor spray bar. If asphalt binder is used and the application rate (and residual amount) is only 0.04 gal. /sq. yd., for example, the nozzle size used should be appropriate to uniformly apply that amount of material. If a 1:1 diluted asphalt emulsion is used and the application rate is 0.18 gal. /sq. yd. (for a residual amount of 0.06 gal. /sq. yd.), it will generally be necessary to use larger nozzles on the spray bar to achieve the desired tack coat uniformity.
It is noted that the nozzle size needed to apply an asphalt emulsion for a surface treatment or chip seal is significantly larger than the nozzle size required to apply an asphalt emulsion for a tack coat. For a surface treatment which requires a residual asphalt content of 0.28 gal. /sq. yd. to properly hold the cover aggregate, the application rate for an undiluted emulsion would be 0.42 gal. /sq. yd. Compare that application rate to that of an undiluted asphalt emulsion rate of 0.06 gal. /sq. yd. for a tack coat with a residual asphalt content of 0.04 gal. /sq. yd. Obviously the same size nozzles cannot be used for both types of application.
A chart usually supplied with each distributor provides the operator with information on the proper nozzle size to use for different application rates. In too many cases, the same distributor used for surface treatment construction is used to apply the tack coat material during a hot mix asphalt paving operation. If the nozzles are not changed, the asphalt tack coat application will be extremely non-uniform – the asphalt material will come out in longitudinal streaks instead of a fan-like spray. The pump pressure on the distributor must be set to match the desired application rate of the tack coat.
Spray Bar Operation
Once the correct nozzle size is selected for the desired application rate and the type of tack coat material being applied, the next step is to assure that all of the nozzles on the spray bar are set at the correct angle and are functioning properly. This means that the nozzle opening (slot) should be set at an angle of approximately 30 degrees to the axis of the spray bar. If all of the nozzles are not set at the same angle, non-uniform application of the tack coat will result. In addition, all the nozzles must be working correctly. If a nozzle is partially or completely blocked, non-uniform application of the tack coat material will result.
For a tack coat application, a double or triple lap of the asphalt material from the spray bar to the road surface can be used. The amount of overlap will depend on the height of the spray bar above the pavement. In most cases, a triple lap is used even though it is not necessary to completely cover the existing pavement surface with the tack coat – 90 to 95 percent coverage is typically adequate.
As the tack coat material in the tank on the distributor is used, the height of the spray bar might rise slightly, changing the amount of nozzle overlap. So the height of the spray bar must be manually adjusted to compensate for the change in the height of the bar as the distributor is emptied. Perhaps the simplest approach is to set the bar height when the tank is half full.
The forward travel speed of the distributor must be controlled to assure that the application rate is correct. If the distributor travels too fast, the amount of tack coat applied to the pavement surface will be reduced. The opposite effect occurs if the distributor travels too slowly for a given spray bar nozzle size and pump pressure. Luckily today's computer-controlled distributors manage variations in speed and are able to maintain the application rate while speeding up or slowing down.
James A. Scherocman, P.E., is a consulting engineer who can often be found arbitrating project conflicts between contractors and public agencies. He can be reached at 11205 Brookbridge Drive, Cincinnati, OH 45249 or at [email protected]. He will present "Identifying, Preventing and Solving Mat Problems" and "Effective Compaction of Hot Mix Asphalt" at National Pavement Expo, Jan. 28-31 in Nashville. For details visit www.nationalpavementexpo.com.
[Sidebar with 3 photos...072, 073, 076 use in order left to right...one caption for all three photos]
Conducting a Trial Tack Coat
Before starting the tack coat application, the distributor operator should check the temperature of the asphalt material to assure that it is at the correct spraying temperature for the type of material being used. In addition, the nozzles on the spray bar should be checked to assure that they are of the proper size and that they are all turned to the same angle to the axis of the bar.
If the distributor has not been used for a time, it is good practice to construct a trial placement of the tack coat over some convenient, unused area to assure that all the nozzles are operating properly. In addition, the trial run can be used to judge the tack coat application uniformity as well as to confirm the proper amount of tack coat application. If desired, the distributor application rate can be calibrated, both in a transverse direction and in a longitudinal direction, in accordance with ASTM D 2995. This is shown above.
[Sidebar]
How to Prepare the Pavement Surface
If the existing pavement surface is dusty, the application of the tack coat may not provide adequate bond between the pavement layers or prevent sliding of the new layer on the old layer. Thus it is extremely important to thoroughly clean the existing surface before the tack coat is applied. This should be accomplished by properly sweeping and/or flushing the existing pavement surface with high pressure water to remove any dust film before placing the new HMA material.