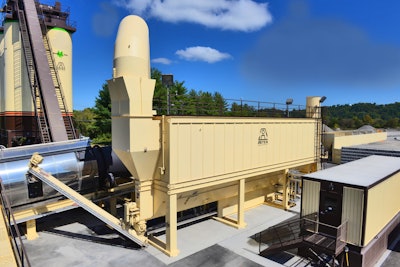
According to the Federal Highway Administration, there are approximately 3,600 hot mix asphalt plants in the U.S. that make over 500 million tons of asphalt material each year. With all that mix being produced, it’s estimated that nearly 8 million tons of dust fines are generated annually.
So just where does all that excess dust go? The baghouse.
Like it or not, it’s the responsibility of the plant operator to ensure they are not exceeding dust limitations at the plant in order to comply with the Federal New Source Performance Standards (NSPS). Therefore, installing a baghouse that not only works efficiently, but also operates properly at all times, is paramount to mix production success.
“The Federal New Source Performance Standards (NSPS) limits particulate concentrations from a hot mix facility,” Catherine Sutton-Choate, director of environmental compliance & product documentation at Astec, Inc. says. “That's the only emission regulation for our industry that is enacted on the Federal level and asphalt plants must hit that standard. Baghouses are the best available control technology to meet that standard.”
For a baghouse to function properly, and keep your asphalt plant compliant, there are a few things asphalt producers need to keep in mind.
Baghouse Maintenance Matters
Like anything at your asphalt plant, the baghouse needs regular maintenance in order to ensure proper operation.
Most baghouses need the following items checked for routine maintenance:
- Check that all solenoids are functioning properly and replace if necessary.
- Check pulse duration, interval and pressure. Monitor pressure drop across the bags.
- Monitor the pressure in the manifold to make sure the bags are pulsing at an appropriate pressure.
- Visually examine the bags monthly.
- Make sure blowpipes are properly aligned to ensure pulse air enters the bag. Never walk on blowpipes as this can warp them and cause misalignment.
- Examine venturi’s and be sure they are in good working order as these components are what induce the shockwave to go down through the bag.
- Check for air leaks in the exhaust system, including aggregate and recycle inlets, connection bands on the ductwork, holes in equipment, access doors not tightened and missing/damaged seals.
If these items are not attended to, over time bag performance will decline and failure will occur as dust is pulled into the felt. As the resulting pressure drop increases, particulate penetration will escalate due to the need to maintain burner suction.
“If plant owners are not performing at least some of the basic maintenance procedures on their baghouse then they can run into problems,” Sutton-Choate says. “Anything that prevents baghouse bags from cleaning is going to increase the differential pressure across the bags. That in turn increases the overall differential pressure throughout the entire production facility from the drum through the fan.
“Exhaust fans are only designed to generate a certain amount of static pressure and so if the pressure drop through the equipment gets too high, then the fans simply cannot generate enough airflow to sustain the production process and production is going to start suffering.”
Sutton-Choate says what causes an increase in pressure differentiation across the baghouse is what is known as blinding.
Blinding is a condition of reduced bag permeability. It means that something is restricting the air from being able to pass through the felt of the bags. One common way to blind the bag is literally by pulling dust into the felt thereby embedding dust particles into bags. This happens when the differential pressure across the bags increases and the plant exhaust system works harder to pull air through the bags and maintain suction.
Sutton-Choate says this is one of the main reasons bags in the industry fail and must be replaced.
Blinding can also occur if the temperatures within the baghouse drop below the dew point. This causes moisture to start condensing out of the flue gases which creates mud on the bags, interior walls and everywhere else.
"Leakage, which is the silent killer of production, uses up baghouse capacity. It can also lead to condensation inside the baghouse," Sutton-Choate says. "Mud cannot be removed by the cleaning system. It requires somebody to physically get inside the baghouse and scrape the mud off the bags. Plant owners can also remove the bags and work on them externally, but it still requires a physical person to do the work and not the baghouse cleaning system doing it automatically.”
Understanding the Significance of Hydrolysis
Another factor that leads to premature bag failure is what is known as hydrolysis or the weakening of the bags due to chemical breakdown. Hydrolysis affects the ability of the bags to clean because it causes them to shrink significantly. This can lead to the blinding previously mentioned, even if the cleaning system is functioning properly. Hydrolysis also causes bags to have weakened fibers, which may result in holes developing since these weakened bags are more susceptible to abrasion by aggregate particles or cleaning at excessive pulse pressures.
“Blinding resulting from hydrolysis is the number one reason bags fail in our industry,” Sutton-Choate says. Bags in an asphalt plant baghouse are prone to hydrolysis because the phenomenon is caused by exposure to moisture at elevated temperatures. This combination of moisture plus heat is exactly what is produced during the aggregate drying process at an asphalt mixing plant.
For the last several years, the industry has been working to educate customers on what hydrolysis is and how they can minimize the effects of it.
“We minimize hydrolysis by offering solutions to control the maximum temperature of the air going into the baghouse because hydrolysis is so dependent on temperature,” Sutton-Choate says.
Additionally, since moisture is one of the contributing factors to hydrolysis, anything that brings down the moisture content of the aggregate will also help to slow or minimize bag hydrolysis. Proper stockpile management is one the least expensive and most efficient ways to minimize moisture.
“For a baghouse to function successfully today, it not only has to maintain a high level of airflow in order to support the production process, but it also has to do it while also maintaining an extremely high collection efficiency,” Sutton-Choate concludes. “We're dealing with limits now that are one quarter of the Federal limit or less so every time a customer starts up their baghouse, there is zero room for error. We need to help customers get there.”