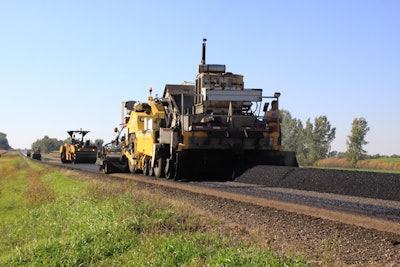
For Jason Duininck, partner of Duininck, Inc. of Prinsburg, MN, trying out the Cedarapids CR652RX Remix paver was all about building a higher quality road. “We were seeing some segregation at the end of the truck dump and were hoping to eliminate the shadow,” he says.
The road rehabilitation project was State Highway 86 in Jackson County, Minn., which required milling the top 2 inches of asphalt and widening the road by 2 feet, so the crew was paving 14-foot-wide lanes. Spanning 9.4 miles, the $3.2 million paving project ran from the Iowa-Minnesota border at the south end to Interstate 90 at the north end, where it joined a previously reconstructed bridge spanning I-90.
The contractor also wanted to achieve consistent mix temperatures across the entire mat width, so the crew could attain the 92% compaction density and receive bonus for temperature uniformity. “The Minnesota Department of Transportation (MnDOT) is testing a pilot program in which a bonus is paid or penalty assessed, based on temperature readings for every 150-foot segment,” says Bill Rieken, paver application specialist for BOMAG Americas.
Scott Heglund, paving supervisor for Duininck, Inc. further explains, “If the temperature differential is less than 25° F across the mat’s width every 150-foot segment, we receive maximum bonus. If the differential is between 25° - 50° F, we receive regular pay, and if the differential exceeds 50° F, we receive a penalty.” For a project the size of Highway 86, this translates into roughly 330 segments for each lane, where bonus or penalty can be assessed.
When contractors begin seeing shadows from particle segregation, then chances are that invisible-to-the-eye thermal segregation is also present. The trucking pattern Duininck established for the Highway 86 project included 8 belly dump trucks hauling only mix and 32 hauling both mix and millings along the 20-mile one-way trip, which allowed the mix to cool from the plant to the jobsite. “The asphalt left the plant between 305°-315° F, so it would arrive to the site at 270° F,” offers Heglund.
The trouble with the conventional paver used by Duininck on the Highway 86 project is the slat conveyor system inside the hopper is not intended to address segregation issues. “By design,” mentions Dave Hosch, vice president of Ruffridge-Johnson Equipment Company, Inc. of Minneapolis, Minn., a BOMAG distributor in Minnesota, “the slat conveyor of a conventional paver pulls material from the front of the hopper back to spreading augers.”
Neither was the windrow pick-up machine attached to the front of the paver. It does not offer reblending capabilities, so segregated material in the windrow remains segregated behind the paver. “A contractor could add an MTV to the train, but this adds costs to the paving process,” says Rieken. “Some larger material transfer vehicles add up to $1.50/ton to the paving costs and are costly to move.”
So Duininck worked with BOMAG Americas and Ruffridge-Johnson to schedule a demo of the Cedarapids CR652RX Remix Anti-Segregation System paver to see if it could help address some of the shadowing issues and help deliver uniform mat temperatures.
High-tech paving train
After the milling crew removed the 2-inch surface layer and holes in the base were patched, Duininck’s paving crew worked to establish continuous paving. The plant and trucking strategy resulted in an average of 330 tph of material flowing to the jobsite and laid in windrows. The asphalt was conveyed to the paver’s hopper via a Cedarapids pick-up machine, which provided a continuous, non-contact paving process.
The mix was a Minnesota Type 4 asphalt, which included a modified PG 64-28 binder and 0.5- to 0.75-inch top aggregate size. Millings from the road were recycled and added back into the mix at a 28% rate to reduce oil usage by up to 50%. The leveling course was placed in a 1.5-inch-thick lift, while the surface lift was 2 inches thick. “We targeted paving production goals of 3,000 tpd for the first lift and 4,000 tpd for the second.
The pilot program on Highway 86 paving tested the feasibility of paying a bonus structure based on temperature differential and compaction densities as well as ride smoothness. Both the paver and compactors were equipped with sophisticated monitoring equipment to quantify temperature and compaction results, helping Duininck’s crew to meet specifications.
Intelligent compaction technology installed on the rollers helped to ensure proper compaction specifications of 92% density were met without over-compacting. These systems are designed to take the guesswork out of reaching optimal compaction. They log detailed compaction documentation to back-up core testing results.
The mainline paver was equipped with the MOBA PAVE-IR system to map surface temperatures across the mat. The system uses infrared sensors to produce a thermal profile for the entire Highway 86 paving project. A full-color Thin Film Transistor (TFT) touchscreen displays real-time temperature data to the screed operator, and the system stores all the files for post-paving review. This data was then analyzed by MOBA Mobile Automation and MnDOT to determine mat temperature uniformity and the amount of bonus or penalty assessed.
Detecting temperature differentials during the paving process allowed Duininck to make corrective actions to asphalt production, truck loading, hauling and paving practices. Adding the Remix Anti-Segregation System paver to the train was one such corrective adjustment, as it offered mix reblending capabilities at the last stage of the paving process.
Thorough reblending
What sets apart the Cedarapids rubber tire CR652RX Remix paver and rubber track CR662RM RoadMix paver/MTV from conventional pavers are the in-hopper remixing augers. Replacing the slat conveyor system of the conventional paver are two sets of twin counter-rotating auger shafts running the full length of the hopper.
Whereas the slat conveyor simply channels asphalt from the paver hopper’s front to the feed tunnel, the large-diameter, variable-pitch augers of the Remix paver provide a differential material draw-down across the shaft length to pull asphalt from all areas of the hopper. The interleafing augers aggressively reblend 100% of the asphalt in a figure-eight motion to diffuse segregated material over an area five times greater than traditional slat pavers. The end result is a more homogeneous mix with more uniform temperatures behind the screed.
Duininck’s crew used a hopper insert inside the CR652RX paver to give some additional surge capacity to maintain continuous paving as much as possible. “Finding the right paving speed is the key to continuous paving, so that you are not outpacing plant production,” comments Heglund.
The Cedarapids insert also helps to eliminate “dead flow” areas, so the asphalt does not cool. “It allows the material to free-flow and further helps to reestablish temperature uniformity,” says Rieken.
Upon adding the CR652RX to the Highway 86 paving train, operator’s quickly picked up on the differences in operating the Remix paver, and they started to notice a difference in the mat behind the paver. “The Remix augers offer a better asphalt reblending (than slat conveyors), and there were no shadows in the mat behind the paver,” says Heglund.
Remix more uniform
After inserting the Remix paver in the train, crew members checked some preliminary temperature uniformity data from the MOBA PAVE-IR system while paving. “We looked at three test shots of mat temperatures, and the ranges were 15°, 18° and 20° F,” adds Heglund. This put the contractor in the maximum bonus category for these mat project segments.
The CR652RX paver was used to pave one lane the full length of the project in late September 2014. After the demonstration, Duininck returned to paving with its traditional 10-ft (3.0-m) mainline slat paver to complete the rest of the project. The crew finished paving the highway in October.
Post completion analysis of the temperature data showed that the Remix paver produced a much higher percentage of 150-foot lane segment grids falling within the maximum bonus level than the slat conveyor. “This is the first opportunity we have had to look at data from both Remix auger and slat conveyor pavers on the same job, using the same mix, the same paving crew and reviewing data over a short time period of 15 days,” comments Paul Angerhofer, product manager Pave-IR for MOBA Mobile Automation.
The analysis included five random project segments from both the Remix and slat pavers. Nearly 63% of the Remix paver readings fell within the 0-25° F temperature variation/ bonus range per 150-ft. segment. Another 36% of the thermal readings landed within the 25-50° F category. Only 1.2% of the average class segregation readings fell above the 50° F temperature variation.
By contrast, the slat conveyor’s five random segment projects showed the traditional mainline paver averaged 0-25° F temperature variation/bonus level only 5% of the time, and the mid-range, regular pay level of 25-50° F temperature variation 69.2% of the time. More than 25% of the time, temperatures varied, on average, by more than 50° F when paving with the traditional slat paver.
“With the variables of mix design including modified oil and long haul distance between plant and jobsite,” says Hosch, “there was a high chance of seeing segregation. This was not an easy job to pave, and that’s why we recommended the Remix paver to Duininck.”
Rieken offers some additional considerations for the Remix paver beyond its reblending capabilities that aid in reducing particle and thermal segregation. “The CR652RX has outboard spread auger drive, which allows the augers in front of screed to back up to each other,” he says. “This eliminates the center drive gearbox and the potential for centerline segregation and top-down cracking. Plus, the cost of ownership between a Remix and conventional slat paver is about the same, so contractors who regularly encounter high-profile jobs with tight specs should consider the addition of a Remix paver to their fleet.”