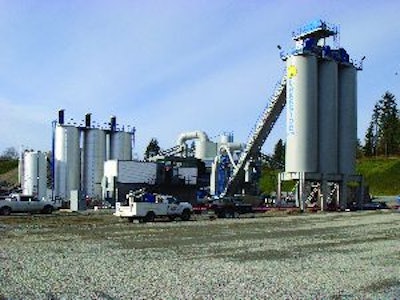
As production manager for Lakeside Industries' plant operations throughout Western Washington, Bill Dempsey obviously gets excited when a new facility is brought online. That was the case in early November, when Dempsey and plant operator Gary Swanson, a 30-year asphalt veteran, turned on the newest installation in the Lakeside network of plants at the company's Monroe, WA facility.
Dempsey has been a fulltime Lakeside associate for the past 25 years, covering the gamut of jobs from laborer to plant operator to quality control manager to division manager to his current position, and he's impressed by the ever-improving technology plant manufacturers are bringing to the industry.
"When you start evaluating the upper-end of plants available in the market, they all have comparable features and benefits," Dempsey says. "Lakeside has a variety of reliable, productive plants, so we're fortunate to be able to draw on the resources of top plant manufacturers."
The company chose to install a new plant at its Monroe facility because the existing plant needed to be moved off land Lakeside was leasing from the City of Monroe.
"We purchased land adjacent to the leased land and decided to purchase a new plant that would meet our needs for that particular market for the next 25 years," Dempsey says. "We kept our other plant running during the installation of the new plant, but now we'll move that 300-tph plant to another location."
Lakeside heritage
Lakeside Industries has been in business since 1952, when Rhoady Lee, Sr. and his son Rhoady Lee, Jr. purchased a sand and gravel, and ready-mix concrete company on the eastside of Lake Washington.
By 1971 the business expanded to include three asphalt paving companies and a dump trucking business. During the 1980s, Lakeside grew to become the largest asphalt paving company in the Pacific Northwest. Today, the company is under the leadership of third generation Lees - Tim Lee as chief executive officer and Michael Lee as president.
Operating west of the Cascade Range from Portland, OR to Canada, Lakeside employs a dedicated quality control staff that is supported by more than a dozen in-house testing laboratories.
Monroe's North Puget Sound market
Ninety percent of the asphalt produced at the Monroe facility serves Lakeside paving crews working in the North Puget Sound area, which extends from North Seattle to the Canadian border.
"It's a competitive market, but the investment we've made in the new facility will position us to meet the needs of our customers," Dempsey notes.
The new plant not only has the capacity to meet Lakeside paving projects, but independent customers as well.
The new plant is also equipped to meet the emerging market demand for reclaimed asphalt pavement (RAP) mix designs. While Washington Department of Transportation currently allows up to 20 percent RAP content to be used on its projects, commercial customers currently allow 20 to 25 percent.
"We made sure this new plant was equipped with two RAP bins to handle the RAP that comes from our projects as well as suppliers," Dempsey notes. "We know that as material costs rise, the benefit of increased RAP usage will require facilities to have the capability to produce quality high-RAP mix designs."
Lakeside also considered the future possibility of producing warm mix with the new plant.
"We're just getting into some warm mix test projects, so we'll be able to add a water/AC mixing system if the interest in warm mix continues to grow and our customers want to spec it for their projects," Dempsey adds. "But our primary interest in selecting and installing a facility that meets emerging mix design trends is that it can produce quality RAP mixes, and this plant will do that."
Choosing the Dillman DuoDrum
Since the decision was made to invest in a new plant and move the old plant, the final analysis zeroed in on a high-production plant that could be operated at approximately the same cost as the old plant.
"We wanted to increase our production capabilities and we wanted to make sure the investment we made would meet our needs for the next 25 years," Dempsey notes.
"We also wanted to install a high-production plant in a way that would lower our operating costs and we were able to accomplish that by eliminating some wear parts (bucket elevators and conveyor systems), which minimizes our long-term maintenance costs," he says.
As Dempsey notes, Lakeside is very familiar with high-performing plants, owning and operating numerous Gencor, Astec and Dillman plants.
"On this installation we decided to go with the Dillman 400-tph DuoDrum because we felt it was the plant that would serve our needs and we felt confident it would be backed by the service we expected," Dempsey says.
Components of Lakeside's new Monroe plant include:
Virgin Cold Feed System
- Eight 9' x 14' cold feed bins with 36-inch self-contained collector conveyor
- A 5' x 14' Deister double deck aggregate screen
- A 36" x 90' aggregate scale conveyor
Recycle System
- Two 10' x 15' recycle bins with 36-inch self-contained collector conveyor
- A 5' x 14' Deister double-deck recycle screen
- A 30" x 86' adjustable recycle scale conveyor
- A 50-ton DEI crusher
- A 30" x 50" closed-loop recycle access conveyor
Dryer System
- A 9' 6" x 40' aggregate dryer assembly with a Hauck Low NOx EcoStar ESII oil or gas burner
- DuoDrum Mixing System
- A 400-tph Model 9020 Duo-Drum Mixer assembly with gravity inlet chute
Pollution Control
- An 88,000-cfm four module reverse pulse baghouse with ancillary equipment
Dust Handling Equipment
- A 16" x 36' dust auger
- A 16-inch rotary airlock with AC drive
- A 40-hp air blower
- Model AS400 Atmospheric Silo
- A 16" x 24' dust auger
Control Module
- A 12' x 40' 10" Model 124010 two-room split-control module
Mix Handling Equipment
- Three 300-ton storage silos that will give Lakeside the flexibility of producing multiple mix designs to meet the daily needs of its own paving crews, as well as the needs of independent local customers.
- A 400-tph x 112' main slat conveyor with reject gate
- A 400-tph x 32' three-way horizontal transfer conveyor
Tanks and Heaters
- Three 30,000-gallon vertical single compartment AC tanks
- A 2 million BTU heater
- A motor control center for tank farm
"The DuoDrum (with separate dryer and mixing drums) also lent itself to the elevated gravity feed system we wanted to accomplish in order to eliminate parts that require maintenance," Dempsey states.
"With an elevated dryer drum feeding directly into the mixing drum below you can eliminate a bucket elevator and sweep points that are high-wear maintenance items," he adds.
The same holds true for how the mixing drum empties directly onto the slat conveyor.
"We really wanted this new plant to be as cost-efficient as possible and the dual-drum design lent itself to eliminating as many maintenance issues as possible," Dempsey says.
Setting up the dryer and mixing drums as a gravity feed system eliminates the discharge flights needed for a conventional in-line system, and as asphalt producers know, discharge flights inside a dryer or mixing drum require maintenance.
And the fact that three Dillman plant experts were on site for a month during installation provided reassurance that the plant would deliver to Lakeside's expectations.
"We did a lot of preliminary work (electrical and concrete) in September and then erected the plant in October, and when we turned it on November 3rd, it was producing mix the first day," Dempsey states. "This is the first double drum system we installed and we believe it will serve our needs for a long time to come."