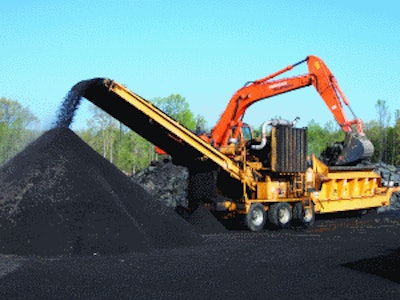
Recycling is a word used synonymously with just about every material under the sun. The country recycles everything from paper products, glass, and grass clippings to plastics and all sorts of metal. That's right, you name it and, as the saying goes, it's likely capable of being repurposed.
The asphalt industry has long been employing recycled asphalt pavement (RAP) in roads. More recently the use of recycled asphalt shingles (RAS), including factory rejects and tear-offs, has been gaining in popularity, riding in the wake of sustainable practices that reduce waste and conserve our natural resources.
Recycling shingles lessens demand for finite natural resources that comprise hot mix asphalt (HMA) and keeps them out of landfills. The latter makes the use of tear-offs even more attractive as they far outnumber their reject counterparts and make up a surprisingly high percentage of landfill content.
"In construction and demolition landfills, as high as 15% to 20% of the material comes from roofing wastes," explains Dan Krivit, industry consultant and Senior Project Engineer for Minnesota-based Foth Infrastructure & Environment. "Add to figure, the fact that more than 95% of tear-offs still end up in landfills, and that alone is incentive enough for environmentally aware individuals in both the private and public sector to consider using them."
There are economic considerations, as well, points out Rotochopper's Monte Hight, marketing manager for Minnesota-based Rotochopper.
"The cost savings can be significant for asphalt contractors who operate vertically integrated shingle recycling operations or buy RAS from another company. Obviously there are concerns, such as asbestos and deleterious materials such as wood and plastic. But these are very manageable issues. Tests performed by shingle recyclers have proven that asbestos has a very low occurrence rate in tear-offs. Furthermore, recyclers can use a number of strategies to ensure clean supplies of RAS that have acceptable levels of deleterious material."
As he points out, roofing companies also benefit from reduced landfill tipping fees, which are only going to increase over time. Krivit agrees "Some recyclers are offering lower tipping fees to roofing contractors that source separate tear-offs. Everyone from homeowner to waste handling companies can benefit from this drive toward clean shingle supplies."
Two immediate challenges
Indiana-based Recycling and Processing Equipment currently has four crews that grind shingles for asphalt producers.
"Already this year, we have ground 200,000 tons of both tear-offs and manufactured shingles, but that's only a very small percentage of the often-quoted 11 million tons that go into landfills annually," says company operations manager Jerry Lambert.
Recycling and Processing Equipment started grinding shingles for an asphalt paving contractor in the early 1990s, long before the green movement and oil costs became drivers, he explains. Prior to that the company actually ground shingles for a landfill, to keep down dust and improve the appearance of its roads.
"The biggest challenge our customers face is guiding roofing contractors toward keeping the shingles clean," Lambert emphasizes. "When roofing contractors keep metal, wood, and other debris from the shingles, they usually have a good flow of product to use. For any asphalt contractors looking to use tear-offs, this has to be one of the biggest hurdles."
The other hurdle for the industry in general is getting more states to write permissive specs. Currently, 11 states allow the use of both tear-offs and factory rejects, and another five allow manufacturers' rejects only.
"Permissive specs allow contractors to use tear-offs as long as they meet certain testing and quality control standards," explains Krivit. He notes that many non-state roads are at least partially state funded, which seriously limits the use of tear-offs in 39 states.
Missouri is one of the 11 states that have permissive specs for tear-offs. "We have been using tear-offs since 2005 and have a good experience with them," says Missouri DOT Field Materials Engineer Joe Schroer "One of the state's biggest incentives to use tear-offs was to keep them out of landfills, and we also wanted to reduce our use of a finite natural resource. Since 2005, we have reduced virgin asphalt content in HMA by 20%, and last year contractors used over 150, 000 tons of tear-offs for their state and commercial mixtures, making a big impact on the landfills."
Schroer notes that writing tear-offs into permissive specs is fairly straight forward, involving some up front testing, reviewing research and then conducting pilot projects. Still, he adds, perception varies from state to state. Currently six states, including Missouri, are conducting pilot projects as part of a longer-range Pool Fund Study.
"Each state is looking at a particular aspect of the use of tear-off shingles in HMA," says Schroer. "One might be comparing the performance of finely-ground versus coarsely-ground shingles. Another might be comparing the performance of tear-offs and factory rejects. Another still might be focusing on quantity, e.g., how much is too much. The study, to be completed in August 2012, will provide a performance criteria and guidelines for states currently using tear-offs as well as for those still on the fence."
Crystal ball
"The price of virgin asphalt will likely continue to go up, reason enough to recycle what we can and save our natural resources," says Roland Getz, president of Arizona-based Getz Recycling Equipment. "Furthermore, what's happening in the Gulf may ultimately reduce our oil supply at one level and, at another, raise awareness about steps we need to take to protect and conserve our natural resources."
Adds Rotochopper's Hight, "We can safely assume that as more state DOTs write tear-off permissive specs, more types of companies will enter the market in different ways. Shingle recycling has largely been in the hands of hot mix companies, as well as grinding contractors that work directly with asphalt companies. While these types of companies will likely continue to increase in number, we will also see more roofing companies, waste handling companies, and dedicated shingle recyclers entering the market.
"Already, we are seeing different types of companies involved in shingle recycling." He cites Owens Corning as a recent example of market innovation.
Last year, the company announced it was teaming up with Heritage Environmental Services to help keep tear-offs out of landfills. The program allows Owens Corning Preferred Roofing Contractors and others to drop off shingles at any of Heritage's four recycling centers around the country.
Although there will naturally be other markets unfolding for RAS, Krivit views the paving industry as its primary focus, at least for the next five years. As he relates, few industries have had the recycling success that the asphalt industry has seen, and tear-off shingles and asphalt roads make excellent partners. They can be directly incorporated into HMA once ground into a fine texture. He's optimistic about incorporating tear-offs into the relatively new warm mix technology, as well.
Both Hight and Krivit emphasize that DOT permissive specs need to move forward before tear-off use will increase dramatically. Supply isn't the issue. Demand is. And that's controlled in large part by state DOT Research & Development departments.
"One of the best tools at their disposal will be sharing the best practices of other states like the information gleaned from the Pool Fund Study," adds Krivit.
Hight emphasizes that the public sector can help remove some of the doubt about using tear-offs, but their future doesn't rely exclusively on its support.
"As an equipment manufacturer, we see more exciting things happening in the private sector," he relates. "Entrepreneurs are creating opportunities rather than waiting for government bodies to allow shingle recycling to occur. People are rightfully concerned about asbestos and maintaining quality standards. But the use of both factory rejects and tear-offs has proven that the benefits far outweigh the challenges."
Specializing in the construction industry, Rod Dickens is a freelance writer based in Neenah, WI.