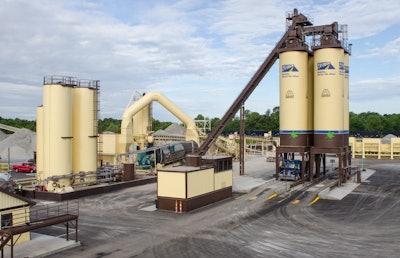
If you’re driving through the central part of Kentucky, chances are Scotty’s Contracting and Stone LLC built the road. Since 1972 when James Scott acquired a paving business, this asphalt contractor has been meticulously building not only solid projects, but also a solid reputation as an industry leader.
Scotty’s has asphalt production facilities located throughout Central Kentucky, and its latest plant addition in Vine Grove represents the company’s ongoing quest to invest in the latest technology offered in a high-production drum plant facility. All facilities are operated by computer controlled mixing and loadout controls to ensure consistent and reliable product to supply its own demanding project specifications, as well as the high expectations of independent paving contractors who buy their mix at one of Scotty’s production facilities.
Whether Scotty’s 11 paving crews are paving 92 continuous interstate miles, a grand-prix style racetrack, an airport runway or a residential driveway, using high-quality asphalt mix produced by the most up-to-date equipment and technology, and backed by over 45-years of experience, has served this asphalt contractor well in delivering a quality project day-in and day-out. Scotty’s 430 associates and $70 million of equipment are put to the test each day, with “Quality Paves the Way” serving as the driving mantra to inspire all to do their best work.
Vine Grove
When it came time to replace an existing plant at Scotty’s Vine Grove location, recycling was a major consideration and adding a reclaimed asphalt shingle (RAS) feed bin to the facility would make it only the second plant in Scotty’s production operation capable of incorporating RAS into its RAP (reclaimed asphalt pavement) mix designs.
At the heart of the plant is an Astec 500 TPH 9 ft. by 47 ft. Double Barrel Drum Mixer fired by a Phoenix Talon 125 MBTU/hr. natural gas/#2 fuel oil burner. The mixer is equipped with Green Pac System used to foam both hot and warm mix designs. The production is fed by eight 10 ft. by 14 ft. cold feed bins and three RAP bins, with one having steeper walls to accommodate better flow of the sticky asphalt shingle material.
Mix is transferred via a 30 in. by 80 ft. inclined conveyor to a 1,200-ton New Generation Storage System comprised of four 300-ton silos. A 11’ by 80’ low-profile truck scale monitors loading weight. A 90,569 CFM Pulse Jet Baghouse filters dust from the mixing process and transfers excess dust (more than is allowed to be put in mixes as filler) to a 650-gal. dry additive storage tank for later disposal. The baghouse system includes a variable frequency drive (VFD) exhaust fan to control airflow and reduce electrical costs.
The entire plant is operated from an 11 ft. 6 in. by 35 ft. 4 in. Command Control Center with a Total Control 2,000 HMA PLC Control System.
“When we decided to replace the existing plant at this location, we wanted to increase our production capabilities to better serve the needs of projects in this area,” explains Ronnie Bryant, who’s been managing Scotty’s asphalt production for the past 40 years.
As Bryant notes, RAP production was another primary consideration when working with Astec in the initial design of the plant and subsequent modifications.
“We have one other plant that can accommodate asphalt shingles, so we thought it just made sense to add that capability to this plant,” Bryant says.
Currently, Scotty’s production facilities can add 20-25 percent RAP to mixes without changing the grade of the asphalt cement binder required for the mix design. With that RAP percentage, approximately 5 percent can come from shingle material.
“If we increase RAP beyond 20-25 percent, we have to use a softer liquid binder to achieve the same type of flowable characteristics of a virgin mix design,” Bryant states. “I think the oxidation of the recycled material makes the overall mix stiffer, so we tend to maintain our current RAP percentage.
That approach seems to work well, considering approximately 95 percent of the company’s asphalt production is used to support its own paving crews, and 80 percent of the projects the crews are working on are state and federal roads. With most of those agency projects being Perpetual Pavements, where only the top surface course is replaced, often the millings from the project are used in the new mat placed.
“We incorporate RAP based on what government specifications allow and if we were to increase RAP content for a private project, then we would change the binder to compensate for the stiffer mix,” Bryant says.
According to survey data collected by the National Asphalt Pavement Association and the Federal Highway Administration, during the 2014 construction season more than 71.9 million tons of RAP and nearly 2 million tons of RAS were put to use in new pavements in the United States. When RAP and RAS are reprocessed into new pavement mixtures, the liquid asphalt binder in the recycled material is reactivated, reducing the demand for virgin asphalt binder. RAP usage also lowers the demand for virgin aggregate and reduces landfill waste.
Some of the other modifications Scotty’s had to make for its new plant had to be done to accommodate the site layout. Additional conveyor systems were needed to accommodate where the plant could be located.
“We had to set the plant up on a different location so it was closer to our rock supply that was being delivered by a rail line,” Bryant says.
The plant layout also better accommodates trucks moving through the facility. Scotty’s has 100 dump trucks in its own fleet and regularly hires additional independent truckers to keep its projects supplied.
“This new plant not only increases our production capabilities compared to the 1986 model it replaced, but it also gives us more options on the different mix designs we can produce on any given day (based on the increase in material feed bins),” Bryant states. “And it’s really going to support the upcoming 10-mile I-65 resurfacing project we have to complete this year.”