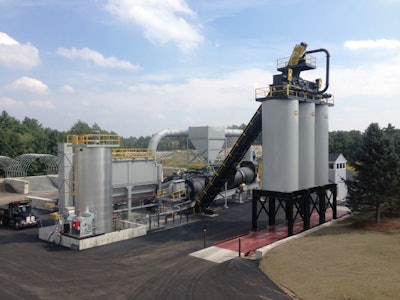
I started in the asphalt plant industry in 1975. I began my career as a shovel operator at an StanSteel batch plant in Hood River, OR. By 1978 I was in charge of the two plants in the area, in addition to operating one of them. By 1985 I was in charge of a number of asphalt plants and traveled the Northwest keeping them running. We were constantly trying to improve costing/profit ratios. One of the areas we experimented in was with fuels we used at our plants. We tried used motor oils, blended oils, PS-300 and Diesel #4 & #6. All of these fuels saved the company money in purchasing costs. And when the only consideration was the “cost per ton” of fuel used, these fuels were all superior to diesel #2.
However, unless everything was perfectly maintained, we experienced all the same issues of burners not lighting reliably and “flaming-out” occasionally that modern plants are experiencing today. One day, after much frustration trying to get reliability, I started doing the math. But this time factoring in the down time related to the poor burner performance. I quickly discovered that all of our fuel cost savings were being eaten up by the costs of the paving crews and trucking stand-by time relating to that down time at the plant. On that day I began a long quest to eliminate the use of heavy oils in our plants.
At first, as you can imagine, I ran into a stone wall. Upper management was only interested in the fuel cost per ton. None of my other data was of interest to them because it was not a finite cost they could easily quantify. They seemed to blame the down time on my plant operators or our lack of ability to correctly tune the burners. To this end they spent large sums of money to have outside technicians come in and re-tune our burners—which only made the situation worse.
Then in 1995, five years after switching to the heavy fuels, we began to realize that there was another hidden cost to using the heavy fuels - sulfur.
Sulfur is a caustic chemical. We had realized early on that we were replacing baghouse bags at an accelerated rate, however we attributed this to lower quality bags produced by the low bidder our purchasing agent was using. In the winter of 1995 we were replacing the bags in our Bingen asphalt plant when one of our mechanics fell through the tube sheet in the baghouse. As I looked closely at the steel, I realized that it was heavily corroded. In fact, all of the surfaces in the dirty air side were in very poor shape. We replaced the baghouse that winter and did not think much more about it.
In the summer of 1996, we had to replace some bags in another plant and again discovered that the tube sheet was heavily corroded. This got me to thinking about the problem, so I scheduled an inspection of all of our baghouses and then discovered that they all had corrosion issues in varying degrees. I took my findings to the equipment’s owner and explained the problem. I explained the issue in great and boring detail, but apparently I explained it well. We switched back to Diesel #2 that week and I am firmly convinced that it is cheaper in the long run when you factor in the cost to heat the heavy fuel, the down-time relating to performance and the elevated costs of maintenance associated with the use of high sulfur fuels.
I own a highly modified and updated 1984 Boeing MS-400 that is leased out. I supply this plant with operator and loader operator so that it is operated and maintained to my specifications. I will not allow them to use high sulfur fuels. In fact, I require them to use low sulfur, on-road diesel #2. Yes, it costs me more per ton to run, but it cost me less in the long term. My baghouse bags are 10 years old and have seen over 1,000,000 tons yet they are still in good condition and there is no corrosion anywhere in my exhaust air system.
I hope all of this proves helpful to you guys. As always, feel free to call me with any problems that come up. There is no charge for phone consultations.