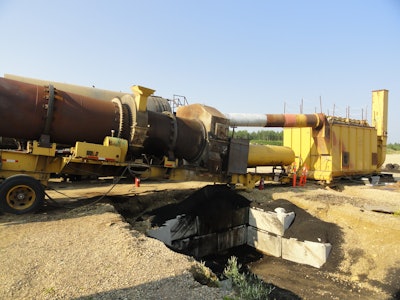
I started my plant career as a shovel operator at an asphalt plant in Hood River, OR in 1975 and I made it my business to know the “how & why” of asphalt plants. After a long career at one paving company, I set-up my own popcorn stand, C.M. Consulting and I’ve worked on asphalt plants all over the world since 1990.
In the intervening years I have seen a lot. The good and the bad. This summer I came upon a plant that defied even the most basic concepts of safe and economical operation. In the following narrative the names have been changed to protect the guilty.
August found me touring the frozen north, heading to a small paving operation up near the arctic circle. I will admit that it wasn’t “nowhere”, but it wasn’t much more than about a mile from it. After an hour-long, arduous journey down obscure Canadian back roads, I found myself at “Bubba Paving.” I was met by the plant operator, Alfie and went to inspect the plant. The first thing I noticed as we walked around was the SIX guys with weed burners who were heating the various pumps and lines of the asphalt system.
Me: “Problems with your hot oil heater?”
Alfie: “What’s a hot oil heater?”
Me: Stare at Alfie in utter amazement.
Me: “How long have you been running asphalt plants?”
Alfie: “This is my third week.”
Me: “At this plant?”
Alfie: “At any plant.”
Me, using my ’inside voice’: “Great!”
As we walked further along I noticed another man with a weed burner diligently heating the fuel lines. The fuel lines? Alfie told me that they ran a blend of waste oil from their shop mixed with diesel. They are a huge dirt work company with hundreds of pieces of heavy iron. He said they mix this waste oil with diesel and burn it. I asked him what was the ratio of diesel to waste oil. He said, “Whatever the shop guys put in it.”
Well, that sounded pretty precise to me, so I decided to leave that alone for the moment. I asked Alfie about a fuel oil heater and he said, “That’s Rodney’s job,” pointing at the dude heating the fuel lines.
Now at this point I had to admit to myself that I seemed to have stepped right into an episode of “The Twilight Zone.” I had driven nearly 600 miles up into the depths of the frozen north to get there, been there less than an hour and was thoroughly astonished at the fact that they were actually able to make about 750 tonnes of mix a week out of this wreckage. How? Now that escaped me. But rest assured, it got better…..
Not a Good Mix
Soon they were ready to make mix. Alfie got his asphalt circulating (again, to my astonishment) and then, literally faster than I can type this, he started all his motors. No reason to worry about a “demand charge” up in the frozen north, eh? Now he was ready to move forward with what I thought was a baghouse pre-heating session. I was wrong again. He called Rodney on the walkie talkie and told him to “open the fuel valve”. Before I could say a word, Alfie jetted out of the control room like an Olympic sprinter, grabbed a lit weed burner and stuffed it up into the burner. The thing lit with a mighty “whump”, rattling the windows and my nerves as I dove up under the counter.
That little bit of drama behind us, I fully expected Alfie to work on pre-heating the baghouse, but no, there would be no time wasted on that! He started the aggregate, counted down 75 seconds and then turned on the asphalt. All the while the baghouse inlet temperature was hovering around 410° F. One thing I should mention, bags start to burn at about 420° F so he was skirting disaster.
After a short time, the drum started to spit out stuff that bore a passing resemblance to hot-mix. Mind you, not the kind of stuff I would send out to a job but as “gob smacked” as I was to this point, I figured I just clamp the ol’ biscuit hole shut and see how this played out.
This is when I noticed that their portable, 72-in. drum was sitting with its tires on the ground and the chassis landing gear in the front. There were no additional legs or supports of any kind. To say it was “shaky” would be like saying the Titanic is “wet.”
Another issue with the thing was that the drum was set at an extreme angle. In areas where the incoming moisture is around 5%, I usually set drum slope at ¾-in. per foot of slope. If the incoming moisture is 2% or so, I may set the drum slope at 1-in. of slope per foot, NEVER more than 1 ¼-in. These guys had this drum set at 2-in. of slope per foot at least. Dwell time in the drum was about half of what it needs to be because their incoming moisture was around 7%.
The result of this was that their outgoing mix was literally sizzling when it left the plant. Of course this is an indication of the aggregate not getting dried in the drum. Still full of water. They made about 80 tonnes, Alfie shut the asphalt off and when the rock turned dry he quite unceremoniously shut the plant down. The last thing he shut down was the burner. By this time the baghouse inlet temperature was near 415° F so I asked him a question.
Me: “Aren’t you worried about catching the baghouse on fire?”
Alfie: “That’s happened twice already,” he said. “I keep a bunch of spare bags.”
Now I had heard it all.
Me: “Don’t you clean the drum out at night?”
Alfie: “Why, I just put rocks back in it tomorrow….”
Well, I had to admit that he had me there.
I have to admit, visiting Bubba Paving and Alfie have been a challenge. But things are improving now. If you need help at your plant, you know where to reach me. Evidently, no challenge is too tough.