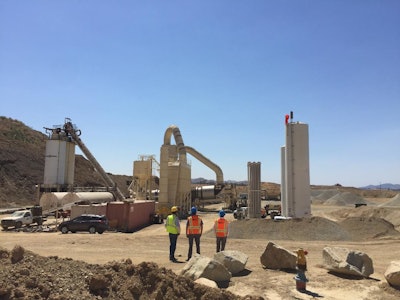
There is no lack of challenges confronting asphalt manufacturers in today’s highly competitive, cost-driven marketplace. Project bidding processes are complicated by wide swings in the price of fuel, which is a critical element in any estimate. Compliance with a range of environmental regulations requires constant vigilance. And ensuring workplace safety is an ever-present concern.
Recently, a growing number of asphalt manufacturers without cost-effective access to natural gas have discovered a simple solution to addressing each of these challenges. They have switched to using liquified natural gas (LNG) to fuel their stationary and temporary asphalt production facilities. They are finding LNG to be more stable in terms of price, more sustainable and much safer than fuels traditionally used to produce asphalt. Here is a closer look at some of the advantages LNG has over other fuels, such as propane and diesel, in manufacturing asphalt.
Simplifies Bidding Process
Accurately determining cost per ton of asphalt is a key to asphalt manufacturers being awarded Department of Transportation (DOT) contracts. However, for those who use propane and diesel in their plants, there is an added degree of complexity in the bidding process, because the price of these fuels can vary by as much as a dollar per gallon over the course of a year in some circumstances.
By comparison, asphalt manufacturers who use LNG as the fuel source in their plants are finding the bidding process greatly simplified. This is due to the stability of LNG prices, which typically vary by no more than a few cents per gallon over a 12-month period thanks to the abundance of natural gas in the U.S.
More Sustainable Than Other Fuels
Mike Acott, president of the National Asphalt Pavement Association (NAPA), says that for decades, the asphalt pavement industry has been proactive in reducing the impact of its operations on the environment. That proactivity is why the sustainability aspects of LNG are so appealing to those who are using it to fuel their asphalt plants.
Asphalt manufacturers are learning that LNG is the cleanest burning fossil fuel. That is because it is the simplest hydrocarbon – one carbon atom and four hydrogen atoms (CH4) – and the simpler the hydrocarbon, the cleaner it burns.
Diesel fuel, by comparison, is much more complicated than LNG. It consists of a mix of long-chained carbons, with sulfur and other molecules attached. As a result of this complexity, its emissions levels are dramatically higher than LNG.
Safer Than Other Fuels
Another important differentiator for LNG as a fuel source is that if a spill or other type of incident occurs, it will quickly evaporate and become non-hazardous because LNG is lighter than air and acts more like helium in its gaseous state, quickly rising and dissipating into the atmosphere.
This is in stark contrast to spills involving propane and diesel. For example, when propane, a heavy fuel, is spilled, it is extremely hazardous until fully mixed with surrounding air. In the interim, the combination of an ignition source and the presence of propane in a low area or corner of an asphalt plant can create an extremely hazardous situation for employees, first responders and others at the scene.
Diesel fuel spills are another case in point. Depending on the amount spilled, they could require a full HAZMAT response team and could contaminate the soil in the area, requiring a costly removal and cleanup process.
Easy and Beneficial Transition to LNG
An important reason for the growing use of LNG in asphalt plants is its widespread utility. Any stationary or temporary plant that is currently operating on propane, diesel, recycled fuel oil (RFO) or waste oil, including hot oil heaters and power generators, is a perfect candidate to convert to LNG.
The first step in transitioning to LNG is a thorough evaluation of the site or sites involved. The evaluation is designed to answer the following questions:
- What fuel or fuels are being used at the location and in what applications?
- Does the plant have a dual fuel gas train if it is operating on diesel or waste fuel or will one need to be installed?
- Are the burners already equipped to operate on natural gas or will a conversion be required?
- How many tons per year of asphalt is the plant producing?
- Where will the LNG storage tanks will be located?
- How long will the plant be at its current location?
- Does the plant have adequate power supply or is a generator being used as the primary power source?
“Once the evaluation has been completed, the transition to LNG as a fuel source is relatively fast and easy and can be scheduled any time there is an available window,” John Greenwood, general manager of California Commercial Asphalt in San Diego, CA says.
While the installation is under way, plant managers simply coordinate with the maintenance department to dial in the burner to the appropriate oxygen content during commissioning or simply tweak the burner to run efficiently with the cleaner fuel source. The entire process can be completed in as little as four to six hours.
“At our plant, we’ve found that LNG is a great alternative to burner fuels and diesel for two important reasons." Greenwood adds. "First, it’s generally more cost effective. Second, the AC temperatures coming from the burner are more consistent and controllable, which equates to better mix and better compaction at laydown.”
Simple Solution to Many Challenges
“Simplicity,” it has been said, “is the ultimate sophistication.” That rings particularly true with respect to asphalt manufacturers who are converting to LNG to fuel their stationary or temporary plants. Not only are they finding the conversion process surprisingly simple, but they are also finding LNG to be a simple solution to many of the complex challenges they face on a daily basis.
Author Scott Johns is president of Cleancor LNG, whose mission is to promote the use of liquified natural gas (LNG) in various industries. Cleancor LNG is a business unit of Cleancor Energy Solutions, a division of Seacor Holdings, Inc (NYSE: CKH). Scott can be reached at [email protected]. Cleancor, as part of its turnkey solutions for permanent and temporary asphalt plants, can supply all of the LNG storage and vaporization equipment, including telemetry systems, tank level systems and all safety systems, as well as temporary power generation equipment during the transition. In addition, Cleancor will work with the asphalt company and the relevant air district to complete appropriate changes to the air permits before the transition to LNG.