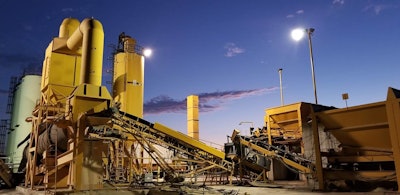
An asphalt plant control system consists of a computer (PC) and in many cases a programable logic control (PLC). The PC and/or the PLC provide commands in sequence to field equipment to allow the plant to produce asphalt to a specifically designed formula. When any part of the system malfunctions or fails the asphalt quality may suffer and the plant may shut down. Avoiding a costly shutdown is best accomplished if you can monitor equipment and component health, schedule preventive maintenance and anticipate repair and replacement to minimize surprises.
The diagram below is a typical schematic of a PC/PLC system and the peripheral equipment involved. The PC serves to provide information necessary for the PLC to function and control the operation of the peripheral devices as well as record necessary data that may be used for reporting or inventory reconciliation. The life cycle of a PC varies depending on the environment it is kept in, and the hardware used to configure the PC. Typically, a PC life expectancy is 3-5 years and should be replaced accordingly as it is an essential piece to keeping your operations up and running smoothly, however, computers that are housed in a clean environment can have a longer life.
Communication between the PC and PLC is managed by a software algorithm, that once installed is consistent and unchanged throughout the duration of the PC. The data brought back to the PC is stored in a data base and requires little maintenance depending on what was supplied with system. Software changes from your system vendor can occur on a regular basis and though they may not be required for of your existing system they due contain enhancements and features that can improve performance if installed. PC systems retain collected data for a limited period of time and usually based on the amount of data collected. It is recommended to back-up your system data so there are no surprises when data recovery is required. Keeping in close contact with your manufacturer regarding your control system is recommended in order to determine what data base maintenance should be performed, along with the frequency of system backup and system updates.
The PLC in the diagram provides commands to field devices and assures they are operating in a safe and sequential manner to produce quality asphalt. The PLC also collects and communicates data back to the PC that operational commands have been actuated or completed. The PLC also provides measured values used for transactions and inventory reporting where appropriate. The communication between the PC and PLC, as well as to and from the peripheral devices, relies on stable connections between devices and consistent dependable power. Bob Gardner, Director of Field Service at WEM Automation explains, “historically, 20 to 30 percent of calls received by my service department are related to plant electrical issues. The issues can range from damage caused by lightning to a loose wire connection on a communication card. When a situation surfaces where it is suspected there is a lost connection, and there has not been a thunderstorm in the area, a quick check of wire or cable connections can sometimes resolve the issue.”
PC’s and PLC life can be severely impacted by lightning. Isolation of peripheral equipment from the PC and PLC through the use of fiber optic ethernet cable can protect from transient current impacting the life of other equipment on the same network. PC’s and PLC’s are typically supplied with surge protectors to protect from line spikes or lightning. Even though the surge protector continues to function it has undoubtedly been weakened and should be replaced following a lightning strike.
Peripheral field device life cycle can also affect plant performance and inhibit the ability to reach peak plant performance. To help maximize useful life, maintenance management systems are available to provide preventive maintenance schedules. These systems are typically configured by the individual plant and measures time related events such as RPM’s or TPH that will indicate a period of time elapsed and preventative maintenance should be scheduled for the individual device or even a scheduled plant maintenance. Some types of activities that can be managed are bearing lubrication, gearbox oil evaluation/replacement and belt adjustments.
While your plant may be running today without issue, it is recommended to periodically review your equipment with your supplier to make sure what you have is current, and not beyond its useful life. The same holds true for your control system. Control systems can last in an asphalt plant for 10 years or more though it is recommended to periodically check with your vendor to see what may be outdated and what is new.
Failure results from issues that go unresolved for a length of time can put strain on the rest of the system, or put the process on the edge of acceptable performance, both of which can have a huge impact on quality and plant operations. Regularly scheduled review of control systems and plant equipment is crucial to maximize equipment life and plant production.
Kayla Stone & Hans Anderson are with WEM Automation, a supplier of control systems that help to keep your asphalt plant investment operating at peak levels.