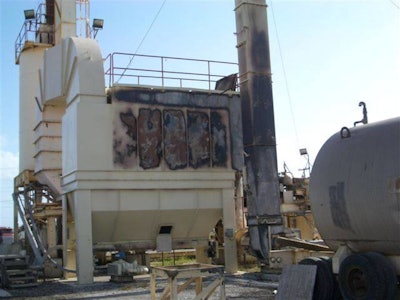
As a part of my company’s mission, I am privileged to be able to travel to some pretty nice locations around the world to work on peoples’ asphalt plants. A few years ago I took a crew and went out into the Caribbean to do some extensive upgrades to an older 6-ft. ALmix Drum plant. At that time, we rebuilt the control house which had become a “rat’s nest” of loose and frayed wiring due to so many people trying to fix this and that problem. For some reason people seem to seldom try to tidy up after themselves. As a result some control panels get to looking like a big jumbled bundle of wires.The best thing to do in these cases is to simply strip out all the old and build it back new.
So we replaced all the switches with modern 22 mm stuff, we built new feeder controls, AC controls and installed a new Systems,Inc. ADP-100 Blending Computer. We also built a new baghouse pulse control system that was automated and linked to the AC inject. This way, the pulsing stops when there is a hot-stop and the pulsing picks up where it left off when the plant is restarted. If the pulsing were to start back at the beginning, even dust flow can be disrupted under certain circumstances and considerably more fines would happen when the system gets back to the bags that haven’t been pulsed in the proper sequence. We then built a new burner control and incorporated an over-temp shutdown safety that killed the burner if the baghouse inlet temperature exceeded 380° F.
I sent the crew home and now it was my turn to train the plant personnel. When teaching new plant operators to run plants, one thing I stress is that when you are starting up cold, after the baghouse is warmed up, you need to incrementally adjust the burner to keep the baghouse inlet air around 330° F. That way, the very first mix that comes out of your drum will be very close to useable, depending on how you have your timers set-up.
The difficult part is having the patience to not get the baghouse inlet too hot and trip the over-temp safety or in other words, stack out the plant. This young plant operator was easily distracted and kept stacking out the plant on start-ups, no matter how many times I reminded him. Several times while I was trying to train him, I had to chastise him for lack of attention. I would even catch him texting his girlfriend during this critical time. It got so bad that I even recommended to the owner that he replaced the guy. But, alas the kid was his nephew so he stayed on at the plant.
We struggled along like this for several weeks and he slowly seemed to get better. After six weeks with the kid, I returned to the mainland thinking all would be fine. But 3 weeks later we got a call that the kid had set the baghouse on fire and I needed to bring a crew over to repair the plant. When we got back to the plant, the pictures with this article show what we found.
With a little investigation, I discovered that the kid had turned the baghouse over-temp shutdown safety up to 425° F. Not a good thing since bags start burning at a little over 400° F. We rebuilt their baghouse, repaired all the burned up wiring and Goyen Solenoids and got the plant running again. In the meantime, the company lost about 25,000 tons of production to their competitor.
Again, we told the plant owner that the kid had to go. But no, he just needed more training the owner figured. So I stayed there with the kid for another month. I thought all was good, the kid really seemed to get the fact that he was solely responsible for what had happened. His remorse and the additional training had me convinced that the kid had “seen the light,” but just a month later the owner called. The kid had burned it down again. This time the owner wanted me to sell the plant for him. As it happened, I had just received a call from a client in Jamaica looking to buy a used plant. So we sent it over to Jamaica where it has worked flawlessly ever since.