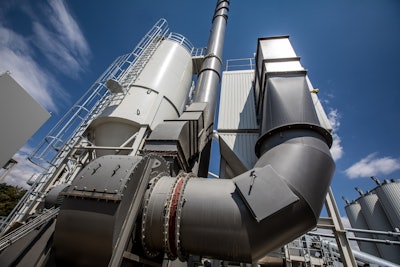
Technologically advanced asphalt plants, producers, and contractors emerged as among potential big winners when the Infrastructure Investment and Jobs Act (IIJA) was approved and signed into law by President Biden on November 15.
Some $110 billion of that $1.2 trillion funding program, also referred to as the Bipartisan Infrastructure Package, is earmarked specifically for the much-needed repair of aging roads and bridges across the United States, an anticipated boon for asphalt production for years to come.
Along with the national drive to improve America’s aging infrastructure and roadways, so is the general shift toward implementing a wide variety of green initiatives, such as recycling, clean energy measures and emissions reductions—areas in which the asphalt industry already is well above many in the industrial sector.
The asphalt industry remains the country’s most diligent recycler with more than 94 percent of asphalt mixture reclaimed from old asphalt pavements being put back into new pavements and the remaining 6 percent being used in other civil engineering applications, according to a survey by the National Asphalt Pavement Association (NAPA) and Federal Highway Administration (FHWA).
Reclaimed asphalt pavement (RAP) used in asphalt mixtures totaled an estimated 89.2 million tons in 2019, with 97.7% of survey respondents reporting use of RAP. Reclaimed material for future use saved an estimated 58.9 million cubic yards of landfill space and more than $5.3 billion in landfill disposal gate fees.
Pavement mixes in the U.S. generally use plus or minus 20% RAP, but plants and producers continue to work on methods that make it feasible to go well beyond that level. To that end, some asphalt plants are providing mixes using 65% and higher levels of RAP content for select applications.
“Of course, RAP utilization provides significant cost savings,” Chris Perkins, Director of North America for Ammann,” told Asphalt Contractor magazine. “Industry leaders increasingly see green practices as not only a way to better the world, but a tactic to improve profitability, too.”
In the U.S., DOTs are showing greater interest in allowing higher levels of RAP, although it varies by state, according to Perkins.
Increasing RAP Without Sacrificing Quality
Through its U.S. hub in Davie, Florida, Swiss-based Ammann currently sells asphalt-mixing plants, heavy compactors and light compaction equipment in the North American market, while keeping an eye on expansion possibilities.
“We are driving sustainable growth in North America and are always evaluating the potential for making additional investments / expansions to properly serve the North America Market,” said Perkins, who added that the company’s base in Florida “will not be the final view” of Ammann America.
___________________________________________________________
See full Q&A with Ammann’s Chris Perkins on Asphalt Contractor online
___________________________________________________________
“It’s essential that asphalt producers have both recycling capabilities and practicality,” he said. “We must provide recycling opportunities while never, ever sacrificing quality.” Ammann offers both batch and continuous plants to meet the needs of individual asphalt producers and contractors. Among key RAP mix technology is the ABP 240-400 HRT plant, specifically designed to incorporate large percentages of RAP.
“The most striking difference is that the ABP HRT’s entire recycling system is arranged vertically, in direct line above the mixer,” Perkins said. “This allows materials to be dropped instead of conveyed, which minimizes wear and optimizes transport of the hot RAP. The HRT approach also means that there is enough room in the plant’s tower for additive feed components and for carrying out inspection and maintenance work.”
In addition, Ammann’s ACP 300 ContiHRT Asphalt-Mixing Plant with continuous production capacity of 330 tons per hour, is capable of producing mix consisting of more than 60% RAP. The continuous plant, introduced to the market in late 2019, meets stringent emissions guidelines while maximizing RAP utilization.
Other recycling technology designed to incorporate higher amounts of RAP in asphalt mixes include Ammann’s RAH100 counter-flow dryer to mix up to 100% RAP, its RAH60 parallel flow dryer to handle up to 60% hot recycled materials and the RAH50 middle-ring dryer incorporating up to 40% recycled materials.
For milling plants that do not employ those specific dryers, Perkins said that up to 30% cold recycled material can go directly into the mixer.
Stationary and Relocatable Options Abound
Astec Inc., Chattanooga, TN, another major developer of asphalt plants and related technology, also has been on a mission to increase RAP in mix and offers producers and contractors a variety of stationary and relocatable options to meet individual needs.
Its continuous-mix plants include portable, relocatable or stationary versions, while some batch plants are offered for the export market and select domestic applications. The stationary Recycle Batch Plants can process recycle percentages from 0% to 40% and switch from recycle mixes to virgin mixes without emptying the hot bins.
Its Double Barrel X drum mixer system, capable of achieving high recycling percentages, separates the drying and mixing processes and enables a plant to process warm and hot asphalt mixes up to 50% RAP content.
For even higher RAP quality mixes, Astec markets a Double Barrel XHR system capable of running mix up to 65% RAP, according to the company. With stainless-steel drum and combustion flights, it features an outer chamber on the drum, an external mixer and the company’s V-PAC stack temperature control system for lower exhaust temperatures when running high RAP content.
Meanwhile, its BG 1800 batch plant series introduced in 2019 is capable (with additional drum options) of producing up to 70% RAP and its modular design can accommodate upgrades as plant operations grow. Customizable to meet local requirements, the BG 1800 plant delivers 120 tons per hour when handling feed materials with up to 3% moisture content. The plant’s mixer has a capacity of 1,800 kg and can take up to 2/5 of RAP.
According to the company, RAP can be incorporated into mix in the BG Series plant by way of the dryer drum or through the mixer unit. RAP is added to the aggregate in the drum through a RAP collar. Via the mixer, RAP is fed into a surge hopper on the batching tower.
Trends in Cutting Emissions, Noise, Dust and Smells
Thanks to ongoing new technologies, asphalt pavement production has emerged as an efficient green process that keeps emissions in line with local regulations, suppresses dust and noise, makes very high use of recycled content in mixtures as noted above, and significantly saves costs for producers, contractors and state transportation budgets.
Ammann offers varied sound-suppression packages to meet specific customer needs, according to the company. The efforts start with equipping burners with variable speed motor drives, which are much quieter, and stack silencers, which control exhaust noise. Sound-suppression options can range up to cladding an entire plant to look like a commercial building in an urban office park.
“Regarding dust, Ammann Asphalt-Mixing Plants remove dust through a highly efficient baghouse filter,” Perkins said. “It actually lowers exhaust dust to less than 0.0044 gr/ft3, which is an exemplary benchmark. We are currently working on reducing this value significantly again, to < 0.0022 gr/ft3.
“We focus on dust reduction points for further improvement. Taking measures at the cold feeder, load-out, skip hood, overflow silo, filler loading area, screen, belts and transfer points makes a big difference. That’s in addition to the efforts provided through the baghouse.”
The biggest reductions in indirect CO2 emissions result from the implementation of RAP, with the main focus on trimming CO2, volatile organic compounds (VOCs), nitrogen oxides (NOx) in the combustion process and on reducing the residual dust content after the baghouse, according to Ammann.
In addition, the use of new fuels is a continued focus by Ammann through renewable energy sources or, in some cases, converting a waste product into fuel, conserving natural resources and putting less pressure on landfills.
“We expect that in the near future other fuel types such as hydrogen will significantly reduce gas emission values, Perkins said. “These fuels will also be much more important in our industry. Ammann is already working on solutions to be prepared for this.”
Another big trend in asphalt production in recent years has been the increased use of warm-mix asphalt (WMA), various technologies that allow producers of hot mix asphalt (HMA) materials to lower mix temperatures some 30°F to 120°F lower than for traditional HMA, according to the Federal Highway Administration (FHWA). In addition, less energy used during WMA manufacturing typically reduces fuel consumption by 20%.
The highway administration adds that the use of WMA reduces paving costs, extends the paving season, improves asphalt compaction, allows asphalt mix to be hauled longer distances at lower transportation costs and improves working conditions by reducing exposure to fuel emissions, fumes and odors.
The latest WMA technologies also reduce asphalt binder viscosity while adding additives to the mix allowing the binders and aggregates to be mixed at lower temperatures and makes the mixture easier to manipulate and compact, according to FHWA.
Solutions Available for Tighter Budgets
Even asphalt producers with limited financial resources or still reluctant to adopt a strict sustainability commitment can still take internal steps to effectively improve plant efficiency, save money, reduce emissions, eliminate waste and lower overall energy consumption.
A potential cost-saving option might be to purchase a relocatable asphalt mixing plant rather than a stationary facility. Astec Inc.’s M-Pack plant, for example, features full-size control rooms, large silos, high production capacity and suitable maintenance access. It is engineered as a set of modules transported by truck and bolted on site.
Of course, those who are not ready to replace an entire asphalt plant might consider upgrading an existing plant’s outdated control system, which can significantly improve operational efficiency, reduce fuel consumption and decrease emissions.
In addition, retrofit systems are offered by many manufacturers today that meet the same standards as newer plants in the handling of certain asphalt-mixing processes. For example, the new Astec Versa Jet burner as a retrofit can be configured to meet individual production requirements, reuse an existing fuel train, work with present controls and be relocated to a different asphalt plant if the need arises.
Plant owners can determine the level of the commitment, according to Ammann. Retrofit customers can incorporate a new dryer, which optimizes heat transfer, reduces emissions and enables the use of an expanded range of materials, including RAP. Other options may include environmental upgrades to the bitumen tank and baghouse, incorporating noise reduction solutions and a range of technological improvements, including revamped burners and mixers.
Whatever the requirements and size of budget, the federal government’s close attention to green processes, recycling, lower energy consumption and reduced emissions, along with the asphalt industry’s already environmentally friendly manufacturing technologies, offers producers and contractors a growing variety of valuable options as the decade progresses.
Mike Botta is an experienced publisher, handling special coverage and projects for a variety of business publications.