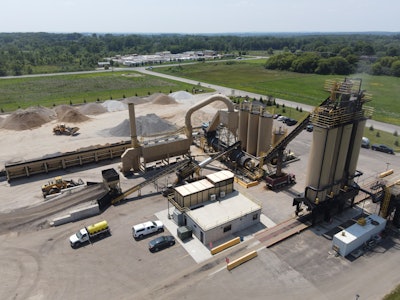
It should go without saying that asphalt plants are a complex interconnected system. After speaking with experts from several top asphalt plant manufacturers, one of the biggest takeaways I had from the information they shared is just how important overall, comprehensive, regular maintenance is.
Each and every part of the machine has some impact on the others, and, while some maintenance points can mean the difference between being able to turn it on and produce mix, in order to produce at the highest quality and at the safest levels, you can't cut corners.
"Running an asphalt mixing plant on a tight budget and with a short offseason requires a strategic focus on maintenance to ensure long-term reliability and profitability," Ryder Harman, the sales manager for ALmix, told me. "If you are not lucky enough to shut down for longer periods of time to work on, or catch up with your plant maintenance, you’re dealing with an additional layer of difficulty in keeping your facility running, especially on a tight budget."
However, there is a difference between being on a tight budget and cutting corners.
"It should go without saying that all maintenance on any equipment is critical to some degree," noted Carlos Cardenas, midwest area sales manager for the Ammann Group. "But some are more important when it comes to simply keeping the plant running. The rest are important to maintain efficiency, limit the environmental impact, and most importantly, to keep everyone involved safe."
Lots of owners and managers of plants have experienced being on a tight budget, and it means that all sorts of decisions must go through a process of prioritization. That's different than cutting corners, because when someone is cutting corners they primarily approach maintenance purely from a cost perspective, regardless of how critical the procedure or part need replaced is.
This list is for those of you out there with a short amount of time and a budget to keep in mind, while still operating at a high level.
Understanding Maintenance Goals
Every part and operation which can be fixed, reconditioned, or replaced can be placed into four different pillars of plant maintenance:
- Keeping The Plant Running
- Efficiency and Quality
- Environmental Impacts
- Safety
This list is not ordered by level of importance, because they are all equally important. If you twisted a plant managers arm, hopefully their answer would be that plant safety rises above all other aspects of maintenance. However, our maintenance goals can be categorized and understood as falling into one of them.
"The truth is there is no such thing as a short list for maintenance," noted Cardenas. "It is all important to maintain a balance between performance, efficiency, environmental impact and safety. If you are truly limited on time and budget, there are steps you can take without sacrificing on maintenance."
Since we are working from a framework with a limited budget and limited time, let's focus on the first pillar: keeping the plant running.
Provided by Ammann Group
#1 Drum, Burner, and Pump
The task of prioritizing your asphalt plant maintenance begins with understanding its basic, core function: drying the aggregates and mixing it with the liquid binder. This would mean the burner and the drum are the absolute first step in plant maintenance.
"The drum and burner are the heart of the plant," said Harman. "Any inefficiency here directly affects asphalt quality, expected production rates, and production costs. Any issues with the drum or burner mid-production can lead to timely delays."
Key Tasks:
- Inspect and clean the drum for buildup or wear.
- Check the drum shell for holes or thin areas that require patching.
- Have your burner tuned by a professional. You should be doing this at least once a year.
- Repair or replace worn-out drum flights to maintain material flow and heat distribution. Make any necessary flighting adjustments.
- Check your trunnions and their alignment, make adjustments as necessary.
- If timing allows, insulate the drum shell for increased efficiency and prolonged hot stop ability. A short winter maintenance period is perfect for having this work completed.
- Ensure burner fuel and air flow is uninterrupted. Inspect filters, valves and pressures.
- Regularly clean strainers in your asphalt pump.
- Check for leaks or visible damage.
- Calibrate the asphalt meter as needed.
These tasks are low-cost on the front end, but can end up costing you a lot more in downtime later. Taking care to check these boxes first can save you a lot of headaches down the line.
"To keep your burner running you simply need to keep the fuel and air flowing," said Cardenas. "Check fuel pressure, and air pressure regularly. If these are not correct check fuel filters, valves, and check for obstructions in the air supply which includes the exhaust gas system."
And that takes us to our next maintenance on a budget point.
Provided by ALmix
#2 Baghouse, Dust Control, And Exhaust
Once you've checked all your incoming lines for the burner, you must follow it through to the outbound exhaust systems, because if it is faulty it will cause your burners to malfunction. While these maintenance checks certainly pertain to keeping the plant running, you can cross off another item on your list because these systems impact our pillars of efficiency and environmental impact and plant safety, as well.
"Airflow is the key to production, so you want to ensure your baghouse is in top operational condition," added Harman. "Proper dust control system functionality [also] ensures environmental compliance and prevents damage to sensitive equipment from excessive buildup."
Key Tasks:
- Inspect and replace worn-out or torn bags.
- Inspect and replace cages.
- Clean ductwork and check for blockages.
- Check for and work to seal off any air leaks throughout the baghouse and ductwork.
- Verify that fans and blowers are operational and efficient.
- Inspect fan bearings and blades for wear and vibration
- Check the damper for proper operation.
- For pulse jet systems: Test air diaphragm valves, solenoid valves, pulse timer board, and differential pressure switches.
- For reverse air systems: Inspect rotor function and differential pressure switches.
- Consider upgrading exhausters using a damper to adjust airflow to exhauster systems driven by VFD (variable frequency drive) to increase efficiency and reducer wear on your exhauster.
"Check the bag cleaning system, air diaphragm valves, solenoid valves pulse timer board, and differential pressure switch for a pulse jet system," adds Cardenas. "For a reverse air system check to make sure all the rotors are functioning correctly, and check the differential pressure switch. Check bags for holes or blindness. [However], if you can’t get the aggregate or the liquid asphalt in the drum then nothing else matters."
Provided by Ammann Group
#3 Cold Feed Bins, RAP Feed, and Conveyor Inspection
Being able to efficiently and accurately move your aggregates is the name of the game. If these transportation systems become faulty and break down during your busy production schedule, it's going to be a huge headache. Not only that, but it's going to cost you money that you can save now by properly inspecting and conditioning the gear now.
"These systems are required to move a large amount of material reliably; malfunctions can halt production and lead to a waste of materials," explained Harman. "Consistent feeding of aggregates and recycled materials is essential for smooth operations and mix consistency."
Key Tasks:
- Inspect belts for wear, tears, or misalignment.
- Lubricate and adjust pulleys, sprockets, bearings, and rollers. Replace worn pulleys.
- Replace damaged belts to prevent costly mid-season breakdowns.
- Inspect and repair cold feed bins and RAP feed bins for wear or damage.
- Consider adding liners in your bins for better material flow and enhanced wear protection.
- Check vibrators and bin gates for proper function.
- Inspect conveyors and drag chains for wear and alignment.
- Calibrate belt scales.
The backbone of the production cycle, your feed systems cannot afford to be overlooked.
"If you do have the time and money to do a scheduled shut down to replace a drag chain how then can you afford to replace the chain if it breaks mid production?" asked Cardenas. "If you don’t have enough time to do it right the first time, you will always find the time to do it right a second time."
Provided by Thalle Industries
#4 Build or Replenish Spare Parts Inventory
If you're keeping your plant running on a tight budget this year, and, after checking off the key tasks on your list, you have some wiggle room left over, then you need to be thinking about what you have on hand just in case something unforeseen happens. There are all the things you can plan for, and then there are the things you never see coming. The best case scenario when those happen, is that you have, on hand, things to get you back to operational as fast as possible.
"Having an inventory of manufacturer-recommended spare parts for your plant helps eliminate downtime during the production season and avoid costly delays in receiving parts," emphasized Harman. "The offseason is the perfect time to inventory your spare parts and stock up on what you need to be prepared for the start of next season."
Key Tasks:
- Contact your plant manufacturer for a recommended spare parts list for your plant, or the specific plant unit from that manufacturer.
- Ensure that you have spares of heavily used wear parts, electrical components and sensors, and parts that typically require longer lead times from the supplier.
- Utilize a clean, dry, and dedicated location for storing the parts as well as a system for replacing spares once they are used on your plant.
Not having an essential part on-hand can be a devastating situation when you're in the heart of your busy season. Downtime is the dirtiest word in the industry, and no one wants to pass along that downtime to their customers who depend on their supply.
"The time to remove the old chain and install a new one would be same in both occasions but if you planned it ahead of time the chain might cost less because you had already punched it and it is now on your lot. So, you don’t have to pay expedited shipping cost or deal with long lead times," explained Cardenas. "You won’t be down an extra day because you now have to clean out the drag and waste the mix, before removing the failed chain. You will not have a line of trucks just sitting idle. It they are your trucks it’s expensive, but if they are your customer’s, that can cost you even more, especially if these unplanned stops are a frequent occurrence."
This year, you can really look smart and frugal by approaching your annual plant maintenance with this two-pronged approach: be economical with your maintenance goals and make efficient use of your time. Planning for the season ahead can be stressful, but you're doing yourself and your crew a favor by taking care of these items now, so when it matters most, you can worry a little bit less.