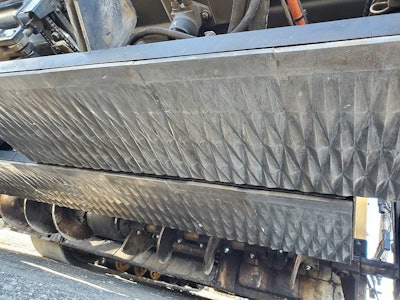
As previously announced, Caterpillar Inc. has entered into an agreement with construction solutions supplier, Axenox, Inc., to acquire the intellectual properties of two of the company’s asphalt paving screed products. Under the agreement, three-dimensional screed plates and the modular screed plate fastening system will be available options exclusively for Cat asphalt paving customers.
These new innovations are true market disrupters for the asphalt paving industry,” said Nate Just, marketing manager for Cat Paving Products.
“The innovative three-dimensional screed plate design improves mat density and smoothness as well as density at the joint to reduce compaction expense and improve the chances of achieving bonus. The modular fastening system reduces the time required to replace screed plates by more than 80% to lower costs and maximize paver uptime availability.”
Brothers Michael and Stuart Frost, long-time paving contractors and owners of Axenox, invented the innovative screed system to improve paving efficiency and quality for their paving operations. “Basic screed design had never changed in our lifetime or our father’s, so my brother and I developed our own screed. We knew we had something special with this technology,” says Stuart Frost. Michael Frost adds, “We want to see this effect the industry in a positive way, just like it has for our paving operations. That’s why we chose Caterpillar and the second-to-none support offered by the Cat dealer network as the best way to carry out our vision.”
Increased density and smoothness
The Axenox screed plate design is a significant departure from industry standard. Whereas traditional plates are flat, these plates utilize a three-dimensional, angular design. This added dimension delivers lateral compaction confinement to asphalt material. The kneading action helps aggregate to interlock more efficiently than with flat screeds, increasing mat and joint density along with improving mat smoothness.
Densities reaching 91% have been measured behind pavers equipped with the three-dimensional screed plates, so there is less of a chance for material shoving and cracking with the roller. These high densities can reduce the number of passes, lowering compaction cost. At the longitudinal joint, higher densities result in improved material containment during compaction to increase final density. Uniform mat temperatures gained by using the angular plates also help to reach specified densities more easily, helping contractors to meet bonus-level work.
The stiffer asphalt mat left behind the three-dimensional plates allow the breakdown roller to achieve higher densities before the mat reaches the tender zone. It produces a more stable unconfined edge that resists pushing and shoving by the breakdown roller, so consistent density readings are achieved across the entire mat width.
The three-dimensional cast plates are made with high strength chromium carbide, delivering high wear resistance and longer life in the field. Whereas traditional screed plates are run with an elevated front angle of attack, increasing wear, grooves at the front of these plates act as the angle of attack, so they run flat to wear more uniformly and reduce cost.
Fast changes
A revolutionary new way to secure the plate to the screed, the modular fastening system reduces screed plate change time from days to less than four hours, minimizing replacement costs for the paving contractor. After a one-time installation of the insulated conductor plate, simple screed plate changes are completed using a unique lock-and-go system. This eliminates the time-consuming process of removing asphalt material from the screed to access the nuts and bolts holding the plates in place. Once normal screed set-up and adjustments are completed on the conductor plate, minimal adjustments are required on future screed plate changes.