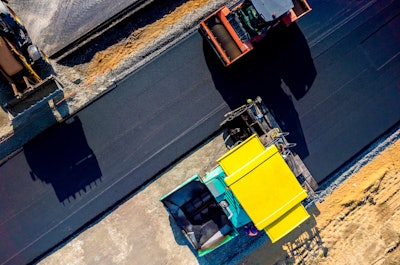
Of the 2.7 million miles of paved roads in the U.S., 94 percent are surfaced with asphalt1. There are a few likely reasons asphalt is used more often than other pavement alternatives – for one, studies have shown that asphalt pavement has a high return on investment thanks to the material’s durability and given it requires less energy to produce compared to concrete.
Asphalt is also recognized as a great renewable resource. In fact, reclaimed asphalt pavement (RAP), also known as recycled asphalt, is an attractive solution given the reduction that using recycled asphalt can have on project costs while also helping to provide a more sustainable project. According to the National Asphalt Pavement Association, it is estimated that the recycling of asphalt pavement saves the American taxpayer more than $2.5 billion and saves more than 60 million cubic yards of landfill space each year. Asphalt’s ability to make meaningful economic and sustainable impacts makes the material ripe for opportunity – this is an important area for new research, innovation and education to ensure correct use and safe handling of the recycled product.
A look back: The ‘Golden Age’ of recycling and the 2000s revival
Over the years, use of RAP has varied in popularity based largely on what is happening in the world, including economic pressures and other outside variables. The 1970s was the first time RAP was commonly used. Traditionally, recycling asphalt involves removing old asphalt pavement and taking it through a series of processes to produce RAP. Then, RAP is blended with new aggregates and asphalt binder to create a new, partially recycled, asphalt mix used to repave roads.
When the recycling of asphalt became popular in the 1970s, it emerged during the energy crisis as an economical option, and the quantity of RAP used in mixtures could range as high as 50 percent. Towards the end of the 1970s and into the 1980s, RAP use declined due to an increase in affordable asphalt binder supply, and performance issues like excessive cracking were observed in some recycled roads, as technology at the time was not mature enough.
In the 1990s, Superpave, an innovative new specification at the time, was introduced to prevent pavement deformation in the form of rutting. It limited the content of RAP in the binder and was also focused on preventing fatigue and low temperature cracking. With little economic benefit, RAP use declined to about 5 percent. In the 2000s, the high cost of asphalt binders influenced those in the industry to revisit recycled asphalt, which has the potential to help save time and money in addition to being a sustainable option. By 2017, approximately 20 percent of RAP was being used on average in asphalt mixtures in the U.S. Today, as government regulations and organizational commitments to sustainable practices continue to grow around the world, additional attention to sustainable options like recycled asphalt is critical.
Properties of recycled asphalt
For recycled asphalt, the quality and performance can be affected by the specific recycled materials used. Understanding the potential affects that different recycled materials can have will help ensure a quality finished product. In the end, recycled asphalt will need to withstand significant weight on roads as well as extreme weather conditions, both of which are major factors that cause stress on road material.
When blended correctly, with the right technology and machinery, RAP containing pavement performs similarly to pavements built exclusively of virgin materials. Use of RAP helps minimize environmental impact by preserving natural resources, reducing landfill waste, and minimizing energy spent by additional aggregate quarrying, asphalt production and transport.
In addition to being a more sustainable option, the ease of use in construction is a key advantage for RAP over concrete pavement. Not only can RAP be easily added to new mix at the hot mix plant, only a single top layer requires being milled off and replaced. Moreover, there are technologies that allow for 100% in-situ recycling. Typically a road train of equipment mills and scrubs the asphalt pavement, mixes it with additives and new binders and places it back in its original place to create a fully recycled pavement. A new pavement can be produced without a single load of material being transported around. Usually this process is used to rehabilitate the structural pavement layers, and an overlay with hot mix is placed on top to preserve the in-situ recycled layers. A process like this is impossible with concrete pavement, where the whole pavement structure must be dug up and removed in order to replace with new layers. In addition, recycled concrete cannot typically be used in the new concrete pavement, and can only be used in bottom construction layers, as a filler, or landfilled.
So, why not turn to completely using recycled asphalt? It’s important to fully understand how the percentage of recycled asphalt used in the overall asphalt mix can affect the final product. Since the 1970s, the industry has debated this topic and the concern that the addition of high percentages of RAP could result in an undesirable chemical composition, prone to accelerate aging and eventually to significant stiffness of the asphalt mix leading to premature failure of the roadway. Increasing stiffness of an asphalt mix improves resistance to permanent deformation like rutting, but it can also cause increases in brittleness and be less resistant to fatigue and thermal cracking2.
Recycling of additional materials
Besides RAP, common materials from outside industries that are recycled in asphalt pavements include rubber from used tires, asphalt roofing shingles, and steel and blast furnace slags. These materials have unique characteristics that ultimately impact the final recycled asphalt product. For example, used tire rubber can enhance overall pavement performance; meanwhile, steel slag can enhance aggregates strength, but both require the right technology in order to gain the associated positive effects. In addition to the specific materials, the actual recycling process can also affect performance.
Significant advances in technology in the last decade have amplified the types of recycled materials that can be used in recycled asphalt. In addition, industry research continues around the changes in chemical composition based on the recycled material. This research is critical to determine which recycled materials could be chemically combative during the blending and diffusion process, and ultimately effect the end product.
There is always a potential risk in recycling asphalt if companies can’t confirm the materials that were used to pave the road previously. This is important because when asphalt is recycled there are materials, like specific plastics, that are not compatible with the blending process. There are many different types of plastic, which is why research plays such an important role – recycling foreign materials like plastic requires knowing the specific way it should be prepared and the maximum amount of that material that can be used.
Longevity of recycled asphalt
Advanced solutions are developed to enhance the performance of RAP mixes. For example, storage silos for hot mix help fuse old and new binders together and produce a homogenous pattern in a mixture, making it more uniform and causing less cracking.
The longevity and performance of a road ultimately depends on the type of road, stresses on the surface of the pavement (e.g. heavy trucks on highways vs. smaller cars driving around a parking lot) and weather conditions. The surface of the pavement is the most stressed layer, so using recycled asphalt below the top layer where it will not be exposed to salt, water and freezing weather can help extend the life of the road.
The future of recycled asphalt, whether it includes improved longevity, innovation around new technology or the discovery of new materials that can be recycled during the blending process will all require continued industry research, communication among industry experts and funding to ensure the quality of the asphalt isn’t compromised along the way. Recycled asphalt has come a long way since its first big wave in the 1970s, and the industry is responsible for ensuring the final product is the highest quality and produces a safe experience and sustainable roads for years to come.
1. Asphalt Pavement Alliance: https://www.asphaltpavement.org/index.php?option=com_content&view=article&id=14&Itemid=33
2.Road Materials and Pavement Design: https://www.tandfonline.com/doi/full/10.1080/14680629.2019.1684346
-----------------------------
About the Author: Pavel Kriz, PhD, PEng Americas Asphalt Technical Leader at ExxonMobil, has 20 years of asphalt technology experience, ranging from lab testing and research and development to refinery and customer technical support. He currently serves as an ExxonMobil asphalt technical team leader in the Americas. Pavel previously worked for Imperial Oil Research Centre in Sarnia, Canada as a lead researcher in the Asphalt lab.
Pavel currently chairs the Technical Advisory Committee at the Asphalt Institute, and is a member of the Canadian Technical Asphalt Association, Association of Asphalt Paving Technologists, AKM10 – Production and Use of Asphalt committee at Transportation Research Board, National Academies of Sciences, Engineering & Medicine. He has authored over 30 technical papers and several patents.
Pavel received his masters in chemical engineering with an emphasis in petroleum refinery operations from the Institute of Chemical Technology, Prague, Czech Republic, and his PhD in bituminous materials from the University of Calgary.