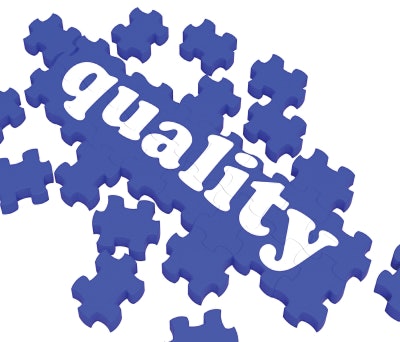
Back in 2006, while working for a cell tower installer as its general manager, I spent a few days in the field helping the crews install antennas. At one point in the middle of the project, our foreman broke out a camera and started taking pictures of our work. I asked him what he was doing, and he explained that our telecom client had a list of photos that we had to take to show that our work met their standards. We would not be paid until the pictures were turned over and approved. This was how our client enforced proper construction. Genius.
One of the biggest concerns small contractors have is figuring out how to ensure their crews carry out the work properly without having to be in the field with the crew every minute of every day. Typically they tell us "I just can't trust my guys to do the work the way I want it done." If they don't figure out how to solve that problem, overcome that emotional hurdle, they'll never have anything but a one-crew business - which means they will never have financial security.
The preceding paragraph opens the door to several topics; however, in this article we're going to focus on methods for ensuring your crews deliver the quality you want, expect and need. I am going to share a few tricks for driving quality that don't require you to stand over them.
Hire and train really good foremen
You can't build a successful business if you can't build a strong team where each member performs his or her job well. That statement applies to the office and the field. Weak foremen create big headaches. A weak foreman will not drive the crews to work fast, he will not ensure the crews adhere to proper safety procedures and he will not enforce quality standards. If you only get one staffing decision right, make it your foremen.
Surprise inspections
Drop by the site after work hours and look closely at the work, or stop by unannounced and wander the site. Take notes. If the work is up to snuff you don't need to say anything. If the work isn't up to snuff walk your foreman around, show him what is wrong and give him a chance to explain. Teach him the difference between acceptable and unacceptable quality.
Require photos
Think about the times we live in. Nearly everyone carries a smart phone. Have you visited a cell phone store lately?
Why are smart phones relevant to this topic? They have digital cameras, typically at least a 5 megapixel camera or better. And they text. And email. I bought my wife's phone in 2007. It's a little flip phone, but even it has a 3 megapixel camera that takes good pictures. And it texts those pictures just fine. I can hook her phone up to the computer and download the pictures. If her phone can do these things rest assured that every phone carried by your crews and foremen can, too.
There is no reason for not having your crews take pictures of their work. You don't have to buy film or pay for developing. It's virtually free and gives you the ability to keep an eye on their work without being there. Do what our telecom client did. Make a list of required pictures. Every time a crew "forgets" to take a picture let them hear about it.
I'm not only referring to pictures of the finished work, though. If the crews are going to cut corners it will be on the work nobody can see. Those are the pictures you really want - pictures of the work that is getting covered up. You can always drop in on the client after the work is done to see whether the finished work looks good. You need confidence that the hidden work is being installed correctly.
Another tip is to use video cameras to do essentially the same thing as still pictures. Give a flip camera to each of your foremen and tell them what you want videoed. Have them shoot five to 10 minutes of video of the work that is being performed. Have them email the video to you each afternoon, and skim through them in the evening or next morning. This is also a good method for communicating previous trade or general contractor issues that are impacting your company's progress.
Additional tips
Pictures speak 1,000 words. Take a page from the manufacturing world and use pictures to show your crews the difference between properly and improperly installed work. Concentrate on the work areas most likely to be questionable. For example, if you lay floor tile show the tile near a wall where a full tile doesn't fit. Use a computer to circle and point out specific critical items on the picture. Print the pictures, put them in plastic sleeves and give a book to each foreman.
Mix and match your approaches for driving quality. Different approaches will work for different crews. Different foremen will justify different levels of heavy handedness. If a foreman proves to consistently produce the quality you expect, rely on the occasional spot check. If one proves to struggle with quality work, make them take pictures, video and drop by unannounced.
You need to develop a way to overcome your fear of stepping away from the field. I've shared several in this article. Find one that works for you. The only choice you really don't have is watching over the work every minute of every day. Good luck.