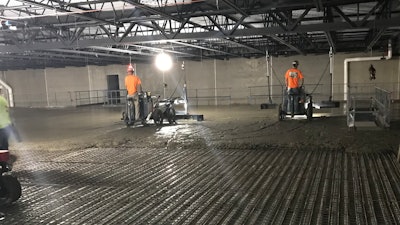
Warehouses are not high rises, and vertical pumping of concrete rarely is a problem—but they do pose their own challenges. Defined and stringent Ff/Fl numbers and burnish requirements, high daily production, continuity of work and limited site access are just a few of the challenges encountered.
Modern warehouses are incorporating more and more slab on metal deck (SOMD) into their warehousing footprint. Flatness, levelness and burnish requirements established for warehousing operations on grade can be much more difficult to attain when off the ground. Mix designs get more complicated due to pump/place issues, and the finish floor elevation is somewhat of a moving target. Despite these variables, consistent uniform finishes can be installed with predictability. Great strides have been made in the placing and leveling of SOMD, and under the best conditions and appropriate deck design specified, warehouse slab flatness and levelness standards are attainable.
Planning of SOMD Placement
Access, reach, truck and equipment staging and movement across deck are critical aspects that must be established prior to the start of project. Usually boom pumps and all-terrain reach forklifts are the main vehicles for moving concrete and equipment from ground to upper levels, although on some projects, light cranes may be utilized. Movement of equipment and material across decks is done using small lightweight tug vehicles or by manpower and wheel assemblies. Warehouse slab on metal deck finishing process.Chad S. White
Lay-down and staging areas along with all-weather access points to the edge of the building will determine deck placement lay-out, as well as size and sequence of placement. Establishing placement rates, staging areas that will be required and total length of pumping system are critical when planning slab placements.
In addition, pump grout disposal needs to be discussed and agreed upon. The best practice is to not incorporate it into slab placement. How are you cleaning/moving hose, clamps and pipe?
Slab Mixes and Fresh Concrete Properties for Pumpable Decks
Evaluate mix design specifications, pump/place/finish requirements for the project and conditions to be expected during placements when designing elevated slab mixes. Local aggregates and the length of the pumping system (vertical and horizontal) will greatly impact mix design. Oftentimes, a hybrid of synthetic fibers and steel reinforcement is an integral component of a warehouse slab on metal deck design due to the crack minimization provided. Pumpability and finishibility are the main drivers in developing the concrete mix design.
Here are some guidelines for an elevated warehouse slab mix:
- Slump 6 to 8 in. at point of placement
- Adequate cement content to achieve pumpability/finishibility
- Minimum bleed water exhibited
- Use largest aggregate that meets slab thickness restrictions and can be pumped and uniform set time
Things to look out for are excessive bleed water and over-sanded mixes. Don’t get caught up in complicated admixture additive solutions; simple is better.
Slab Deflection and Solutions
Most warehouse slabs on metal deck will require strike-off to a fixed Ff elevation with minimum and maximum slab thicknesses specified. Gauging the slab for a specified thickness without Ff control can be a challenge to overall slab levelness that must be discussed and understood prior to construction. Teamwork between steel erection and slab installation is critical.
Important steps to take include surveys of beam and decking elevations pre-placement and post placement and review of camber and anticipated deck movement.This information is critical to managing your loading and placement procedures. Concrete placing foreman should receive slab loading instructions regarding time and area placed before strike-off, min/max slab thickness requirements and any other special instructions prior to placement.
Devote extra attention at construction joints to ensure the joint is at finish floor elevation after deck is loaded. SOMD steel structure will take time to deflect with the concrete loads. Deflection is very hard to calculate and predict. Review the designer’s intent in the specifications and the manufactured camber. Concrete yield should not be more than 5% overage.
When loading the deck understand what the weight of your equipment is; size and weight does matter. Construction joint lay-out, concrete place/finish means and methods, and equipment to be used should be both understood and approved by the design team.
Equipment Requirements and Current Practices
If you are placing medium to large SOMD placements, puller/placer equipment for moving pump hose will save on labor and improve safety. Boom pump-slickline-rubber hose, puller/placer equipment is currently the most common set-up for placing large SOMD. Practical production rates of 80 cu. yd. per hour for large deck placements is attainable. The increase in the amount of rubber hose that can be used with puller/placer units is substantial. Skid plates/Dragon Eggs are essential to facilitating movement of rubber hose.
Puller and placer equipment.Chad S. White
Drive-in laser screed machines are currently the state-of-the art for placing high production SOMD that are designed without significant deflection and are approved for use by design team. Screed widths will vary from 6 to 10 ft., machine weights 1,100–1,700 lb. Recommendation would be for a controlled elevation rake machine with 8-ft. screed head and strike-off with 10-ft. screed head with auger. Rake pass elevation should usually be 1/2 in. higher than finish pass. Hand held vibratory screeds are used for strike-off of edges and off-sets. Oftentimes, a hand-held vibratory screed will be used to cross-check drive-in screed landings. Slab thickness and Ff elevation should be continuously monitored.
Ride-on trowel machines will vary in weight from 1,500-2,500 lbs. Smaller 8-ft. ride-on trowels are easier to move around, but 10-ft panning capabilities will help Ff numbers. Make certain that your planned equipment usage for placing and finishing SOMD is reviewed and approved by the design team. Pan floating of slab.Chad S. White
Placing & Finishing of SOMD
Managing placing slump is crucial. Set times are tied directly to the placing slump and placement rate. Experience dictates that an 8-in. slump max at point of placement is a good guideline. You must minimize unwanted bleed water. You want some bleed water at the surface to facilitate finishing operations, but excessive bleed water will cause differential set times and weaken the surface, especially if machined into the floor.
Managing differential set is one of the most critical finishing challenges to overcome for a successful warehouse SOMD placement. Direct sunlight and wind are the enemy and can be mitigated by careful pre-planning. Steps to take include:
- Avoiding weather events
- Shading/screening of placement area
- Use of evaporation retarders
Pan tight before first trowel pass with combination blades. Plastic trowel blades used properly will diminish the effects of differential set and reduce blemishes. Using plastic trowel blades too early in the finishing process may not achieve the surface density desired, so for best results, use plastic trowel blades only for the last pass and final burnish of the floor. Edge troweling machines should be a key component of the finishing process. The use of roller tamps to minimize aggregate shadowing typically doesn’t help much due to the higher placing slump required for pumping, although they should be considered depending on the local aggregates and required surface finish.
Burnish and gloss requirements specified will be similar to requirements for warehouse slabs on grade. Gloss meter readings may be specified.
Some final tips for a successful placement:
- Get the mix right. Most mixes will require some tweaking to be pumpable and have the finishing characteristics desired. Allow enough time in the schedule prior to start of placements so that trial batches/mock-up panels can be properly evaluated.
- Access, reach and staging usually dictates what you can do more so than pump/place capability. Ensure that production goals and site logistics requirements are clearly understood by all.
- Treat it like an exposed warehouse floor. Most SOMD are not exposed and have minimal Ff/Fl or slab finish requirements. The mind-set of the place/finish crew sometimes needs to be recalibrated.
- Maintain slab elevation surveys. Documentation and a robust data base will confirm specification compliance, improve deck loading procedures and provide greater predictability of in-place deflection during place/finish operations.
References:
ACI 302 1R.15 “Guide to Concrete Floor and Slab Construction”
Bruce A. Suprenant, “Construction of elevated slabs” Concrete Construction Magazine 1990
Bryan M. Birdwell, “Committed to Producing the Finest” Concrete Contractor Magazine April/May 2011
Bryan M. Birdwell, authored technical paper for SSI Bulletin “Floor Flatness and Levelness Testing-The Complete Specification” 2018