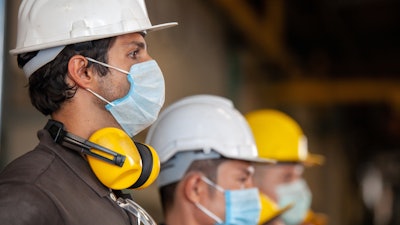
Most hospitals and/or healthcare facilities are under some level of renovation nearly every day. Harmful pathogens can become airborne during construction work and potentially infect patients with compromised immune systems. The work doesn’t even need to be in the building, construction down the road can also pose a threat.
In short, a secondary infection occurs when a patient contracts an infection unrelated to the primary issue. For example, should someone be admitted to a hospital for a broken leg and contract MRSA (Methicillin-resistant Staphylococcus aureus) while there–that’s a secondary infection. According to Alliance for Aging Research, about 99,000 Americans die each year from hospital-acquired infections. And 5 to 10% of these cases have been attributed to construction work in a healthcare setting.
Many contaminants like Aspergillus Niger (a.k.a "black mold") are able to lay dormant on even new constructions for 10 years. If infection control is not handled correctly, contractors can run the risk of posing a risk to any patient going in or out of the facility.
While there are best practices and personal protective equipment for the immediate construction worker and the nearby team, there isn’t a national standard for safety and contamination—the United Brotherhood of Carpenters & Joiners of America (UBC) is looking to change that with Infection Control and Risk Assessment (IRCA) Best Practice in Health Care Facilities.
Founded in 1881 and currently representing over 600,000 members, the UBC is the biggest building trade union in North America. According to Tom Bender, Infection Control Risk Assessment Director with the Eastern Atlantic States Regional Council of Carpenters (EASRCC), the UBC spends about $200 million on training. The EASRCC is in the Eastern District, one of six districts within the UBC, which encompasses much of the original colonies. At about 45,000 members strong, the EASRCC covers Pennsylvania, New Jersey, West Virginia, Maryland, Delaware, and Washington D.C.
“We’re 100% self-funded and fund all of our training internally with training centers throughout the U.S. and Canada,” says Bender. People often aren’t considering concrete contractors as carpenters, however UBC considers “carpenter” an all-encompassing term to include just about anything related to the building of a structure, with the exception of MEP’s, framing, drywall, trim, roofing, concrete forming, concrete walls, etc. Most of their concrete work, explains Bender, consists of large-scale construction or commercial concrete projects like high rises, parking garages, malls, bridges, tunnels, poured-in-place foundation walls, insulated concrete form systems, flatwork as well as slabs.
Fun Fact:
Peter J Mcquire, cofounder of the UBC created the first Labor day September 5, 1882 to recognize the many contributions workers have made to America's strength, prosperity, and well-being.
“If you go outside of our organization, and you ask somebody that does concrete formwork, they'll tell you they do concrete. But inside our organization, we say, ‘No, you're a carpenter,’” explains Bender. “But that title, and moniker isn’t used by people outside of our organization. They do the same work; the general public doesn’t classify each other outside of our organization like that. But I think we should, anybody that's working in the trades as a profession should start looking at what they do as building America and give yourself the appropriate title and recognition.”
Creating An Infection Control Standard
Beginning in the early 2000s, the UBC started outlining the risks created to better protect patients during construction, renovation, and maintenance–using the standards set by the healthcare industry. UBC set out to create an educational / training program which shortly became an “unofficial standard.”
However, “standard” is a bit of a misnomer here–what really happened was the set down of some best practices, as Bender explains it, to mitigate the secondary infection rates in hospitals that arise from construction activities. He cites that over 2 million people are subject to these types of secondary infections (MRSA, urinary tract infections, C. Diff, etc.) and about 100,000 of those patients end up dying and up to 10% of those cases are related to construction.
Infection control is a two-sided coin with clinical on one and construction on the other. The clinical side protects patients and has national standards. These standards are strongly enforced.
However, the construction side poses a bit more of a challenge in creating a true “national standard." Construction protocols for ICRA are typically regional and network driven. These networks–especially those for in the eastern region of the U.S.–might include 5-year-old hospitals and 105-year-old hospitals. The question at hand, says Bender, is “How you go about complying with all the rules in a building that is terrazzo floors and cementitious speed tile walls and ceilings when you have another building that was built 100 years sooner?”
He's seeing the Federal Guidelines Institute has started to change regulations to require any renovations to follow current standards. There can be issues should these regulations not consider older structures. “The standards are definitely coming, but unfortunately,” said Bender. “Right now they’re just not there.”
Addressing an official national standard for infection control during construction, the UBC developed a national ICRA best practices curriculum with the assistance of industry partners and subject matter experts. The EASRCC and UBC have implemented this ICRA program to help train construction workers on proper procedures to properly contain work sites during construction or renovation across the U.S. and Canada.
As part of this training, carpenters learn how to seal themselves off from the rest of the facility and patients, how to control air flow by creating negative pressure within their construction area so no debris or harmful contaminants can escape, and how to use HEPA machines to clean the air as they work. Once trained the EASRCC instructors help to train other trade workers to the same standards and procedures to reduce the secondary acquired infections at healthcare facilities.
There are two ICRA training programs available for contractors:
- The 24-hour training program was created for UBC members that will actually work in a health care facility and build the containments. This curriculum requires the attendee to be in the classroom for a total of 24 hours, in person. It’s designed to be a three-day class with two days (16 hours) of classroom training and 8 hours hands-on.
- The 8-hour training program was designed for the people that have to work around or in a healthcare facility but not responsible for the containment construction themselves.
Safety Practices, Today
Whether a brand-new construction, a renovation, or in-house maintenance, Bender suggests that anyone on a project must be aware of their role in protecting the current and future occupants in any healthcare facility. “Some of the risks that we can cause could linger inside walls above ceilings, below the floor for years before they pose a problem to any patient in the future. It's not just about the patient's room now or the staff that's in the building, it's also about future occupants,” he says.
Mostly focused on the stoppage of particulates and debris, IRCA protocols was designed for containment. Where OSHA’s mandates are mostly on an allowance of silica in the air, ICRA is concerned with all contaminates and any type of debris. It goes beyond making sure you use HEPA-certified filters and vacuums for your system; there’s how and why you do what you do.
Beyond training and erring on the side of caution, there isn’t a magic equation for the estimation process, unfortunately. Figuring out how to bid while both expecting the unexpected and not bidding yourself out of the market can be difficult. Consider comparing the infection control concept to knowing how many braces to use on a concrete form—you won’t until you don’t put enough in. At that point the outcome can either be a small leak or catastrophic.
It’s similar in an ICRA environment. “You never know if you’ve done too much or if you’ve gone overboard,” comments Bender. “But you find out quickly if you didn’t do enough.”
Urging caution, he continues, “There are case studies from overseas to the ramifications that these outcomes have had for the construction workers for the clinical workers. You put 6, 9, or 12 months into a cancer patient. And they beat cancer, only to die of a secondary infection from the construction project that was going on during their last treatment. It affects everybody, not just that patient.”
What Contractors Can Do
- Know the risks associated with the work
- Understand the effects of the work performed, inform, and educate the owner of what is planned (For example, how much dust will be generated from that floor grinder? How will that be contained?)
- Follow the healthcare facility guidelines, meet their demands, exceed expectations
- Plan ahead
- Use HEPA certified filters and systems
- Create a negative pressure room with proper exhaust ports, remember to note exhaust direction
- PPE and PPE decontamination
Flipping That Coin
In the coin of infection control standards for a healthcare facility construction project, contractors should think about their own employees, as well. Healthcare networks says Bender, are starting to look at if contractor companies are providing healthcare to the workers and considering that when reviewing bids for projects–along with the plans you might have in place to contain the job.
Having these practices in play, workers certified and trained to run the jobsite safe can all add to winning the next bid. But, consider that these issues are not exclusive to healthcare facility projects but schools and grocery stores, as well. The UBC has developed ICRA best practices/curriculum dedicated to non-healthcare work following federal guidelines for constructions concerning beverage and food manufacturing, pharmaceuticals, retail, hotels and education centers.