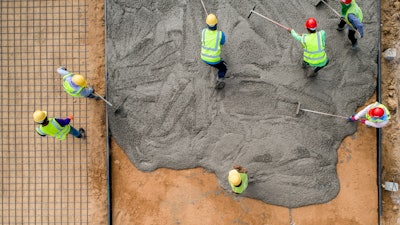
Unless the weather is really extreme, not placing concrete isn’t really an option. There may be other factors that force a stop work but temperature is often a challenge that can be worked around.
Like shift changes, there are different things contractors can do. One of the most common solutions is to start pouring in the middle of the night when it’s cooler in the “hot weather” climates or seasons to avoid dealing with a blazing sun bearing down on you – and your concrete - the entire time.
According to the Occupational Safety and Health Administration (OSHA), a lot of the U.S. is on track for the hottest summer on record. Likewise, the Center for Construction Research and Training states that even though construction workers account for only 7% of the country’s workforce, they experience 38% of all heat-related deaths at work in 2020.
No matter the time of day, if hot weather is going to be a hazard; treat it as such. The first item on the day’s agenda should be the toolbox talk. Take this opportunity and remind the workers of how the body reacts to hot weather conditions and dress appropriately. How you dress is key. “Sometimes people think that not wearing the shirt or just wearing their safety vest will keep them cooler,” notes Nick Demonte, Operative Plasterers' & Cement Masons' International Association-ITF (International Training Fund) Cement Mason Coordinator. “It’s actually the opposite.”
No matter the time of day, if hot weather is going to be a hazard; treat it as such.Operative Plasterers’ & Cement Masons’ International Association
His recommendations:
- Wear lightweight loose-fitting clothing – there are clothing options available today that help wick sweat away and keeps you cooler once a breeze comes through.
- Take breaks in shaded, cooler, or air-conditioned areas to escape the sun and heat.
- Stretch
- Stay hydrated – take water breaks during the course of the pour when you can depending on manpower. Hydrate the day before too, not just the day of or during. Do not wait until you are thirsty to drink water. Avoid alcohol and caffeine as much as possible.
“If you see a co-worker with symptoms of heat exhaustion, speak up,” says Demonte. “Seek medical attention immediately.” Contractors should have a heat illness prevention program and emergency plan in place for training on heat hazards and steps to prevent heat-related illnesses.
Responsibility
According to OHSA’s Hazard Alert on extreme heat, employers are responsible to:
- Provide workers with water, rest, and shade.
- Allow new or returning workers to gradually increase workload and take more frequent breaks during the first week of work as they build a tolerance for working in the heat.
- Plan for emergencies and train workers on prevention.
- Monitor workers for signs of illness
Source: osha.gov/heat
It’s About Time
Because the biggest issue when placing concrete in hot weather is the fact that it’s setting quicker, you’ll have to move at a faster pace. How the concrete sets, will dictate the pace and how fast you’ll have to work so contractors may need to call on a few extra hands to get things moving as quickly as possible.
ACI 305.1-14 (Specification for Hot Weather Concreting) provides recommendations and best practices for concrete placement when environmental conditions can have detrimental impacts on concrete quality. High-temperature placement of concrete can sometimes cause challenging and difficult conditions to ensure that concrete quality and desired properties are maintained. However, it is not just the temperature of the concrete that must be controlled during placement as other factors such as ambient temperature, humidity, wind speed and exposure to sunlight can also play a significant role in the hydration process of cement and ultimately alter the physical setting characteristics of the concrete mixture.
Although many local and national requirements vary, it is generally recommended to consider taking precautions for placing concrete in “hot weather conditions” when the concrete temperatures are in the range of 77-95º F (25-35º C). ACI 305.1-14, sections 3.2 and 3.3, recommends a maximum temperature of fresh concrete at time of discharge to not exceed 95º F (35º C), unless supporting field experience or pre-construction testing is available.
Known Problems
“Hot weather” conditions can create difficulties in placing and finishing fresh concrete such as:
- Increased water demand and accelerated slump loss
- Increased rate of setting times resulting in finishing difficulties
- Increased tendency for plastic and drying shrinkage cracking to occur
- Potential difficulties in controlling entrained air characteristics
- Inability to reach desired strength requirements
ACI 305.1-14, sections 3.2 and 3.3, recommends a maximum temperature of fresh concrete at time of discharge to not exceed 95º F (35º C), unless supporting field experience or pre-construction testing is available.@adimas | @pawimon - stock.adobe.com
Mix Design - Understand the material you’re working with is vital; know what chemicals are in the mix and the design. “How the mix design is composed of is going to be key and how fast its’ going to set itself off when it hits the ground as [you] start to pour,” says Demonte. Admixtures like retarders can help control concrete and offset the accelerating effects of hot weather. The opposite rings true for cold weather where accelerating admixtures can be used to speed up the setting process and early strength development. This would allow forms to be removed sooner and improve the concrete resistance to freezing at an earlier age.
If requesting a retarder or accelerator to the mix, inform your supplier exactly how much you’re looking for. The OPCMIA goes over many of these issues in its education: understanding the testing, understanding the formulas, how many gallons per yard, etc.
“Every job is different. It’s not one formula that works for everything,” says Demonte. Take a step back and try and see the whole picture. Note how your current job is different than others. If pouring on a roof deck, for example, consider that the sun will have heated the surface already and that heat can accelerate the concrete.
There are a lot of moving parts that go on that contractors may not be thinking about when they order a truck. The optimal situation is receiving your delivery first thing in the morning. If the pour is scheduled for later in the afternoon, it raises the chance that that truck has been on multiple sites. It’s gone through more revolutions during the course of the day – trapping heat inside even more and affecting how fast the concrete sets. While rare, the drum may also have remnants of previous jobs with leftover material which can set off the material quicker than you want.
Batch Temperature - Another big component is the temperature of the material. Ask if (and how) your supplier is keeping it cool overnight and how long the concrete sits in the drum. Look at the ticket and take note of the time it was batched from the plant. The more revolutions the drum spins, the hotter the drum gets.
If required for the job, a testing company will test the temperature of the mix when it arrives.
Cold water or ice are common solutions for a bit of insurance against the heat. On the opposite end, hot water can help set up the concrete quicker in the colder winter. Remember to consider your water-to-cement ratio.
“Some batch plants will keep the aggregates cool,” says Demonte. “Sometimes they’ll spray it down with water and keep that material cool. If it’s been sitting in the blazing sun, that material gets hot. Once you put all the ingredients together – it just makes it set off quicker.”
Site Situation - Direct sunlight is also a big component. Treat the job differently based on if you are working in a covered building vs. direct sun. “Depending on the structure of the building, you have to think about where the sun starts and where it ends,” says Demonte.
Consider the structure of the building you may be working on. Will you be in the sun all day? Will you have trades overhead while pouring a slab? Perhaps decking will be installed overhead creating shade. Look at the big picture and how the site changes throughout placement and finishing.
The key: plan ahead and use time wisely. Consider the sun’s movement. Keep the team together to make the placement and finishing easier and more efficient. Depending on the size of the placement more manpower might be needed.
“How you plan your pour, how you bring your equipment onto the slab is going to be key,” says Demonte. If the equipment is staged in the shade and you start pouring in the sun – that could be a problem and not allow you to get the equipment across the slab.
It’s all organizing and planning. Consider where the sun rises and sets; how to stage equipment, where to begin the pour, and where to end to avoid cold joints. Some additional key elements to consider here include the type of substrate you’ll be working on: metal, a vapor barrier, gravel, aggregate, compacted, etc.
“By understanding mix designs is something that is going to be really beneficial in working with the material. Doing your homework before the pour is just as important as while you're doing the pour.”