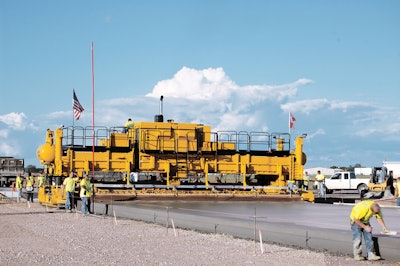
Downtime is the enemy of a concrete slipform paver. These machines automate traditional concreting procedures in a continuous process; downtime in the middle of a job can be very costly.
“There are no re-dos in concrete paving,” says Rudy Bouillon, U.S. training and sales manager, Power Pavers Inc. “If the paver fails in the middle of a job, there will be a loss of concrete, which can equate to a substantial loss of money and time [to repair the job]. The enormity of loss depends on the size of the job and the amount of concrete in front of the machine.”
“There are numerous costs that can be incurred when a slipform paver goes down on the job. One of the most costly is the loss of concrete,” says Wade Bowman, national sales manager, concrete slipform products, Wirtgen America Inc. “A high-production contractor might have thousands of dollars in concrete lined up in front of the machine.
“For a paving contractor, a job might be 24 ft. or wider and 8 in. or more thick. To put a machine like this in motion, it takes a lot of concrete, and good ride numbers require that the machine keep moving,” he continues. “This equates to a lot of concrete, or money, on the ground in front of the machine. Of course, breaking down also affects schedules and there can be foregone bonuses or, conversely, penalties including liquidated damages.”
Cleanliness is Top Priority
The best way to minimize downtown is a firm commitment to cleanliness and preventive maintenance of the machine.
“If you take care of your machine, it will take care of you,” says Nick Maupin, concrete paving product support specialist, Wirtgen America. “This is true with your car as well as a slipform paver.”
“It all starts with the cleanliness of the paver and the time the crew spends cleaning it,” agrees Dennis Clausen, director of training at GOMACO.
Clausen spent years in the field visiting paving crews. “It always amazed me that the boss would complain when a crew spent too much time cleaning a slipform paver, yet that same boss wouldn’t want a spec of dirt on his new car,” he comments. “Didn’t he realize that without the paver, he wouldn’t have a new car?
“At the end of the day, clean pavers are productive pavers,” he states. “Cleanliness makes it easier to diagnose existing or potential issues. A clean machine also allows easier access to maintenance points, which saves money when it comes to repairs because it cuts the time necessary to fix or replace components.”
Cleanliness can also affect the quality of the finished surface. “The bottom of the mold is what the surface of the concrete will look like,” Bouillon points out. “Unprofessional-looking results or failure of a paver in the middle of a job could often have been prevented if the machine was cleaned properly. Side plates will lock up if they aren’t cleaned out and crawler tracks won’t work properly if there is hardened concrete stuck to them. This is all preventable by washing the machine at the end of a shift.”
A high-pressure washer for immediate on-site cleaning is provided by some manufacturers as part of the equipment package.
Preventing Failure is Possible
“Wear, neglect and abuse are the main causes of paver breakdown on a job,” says Bouillon. “Preventive maintenance can’t prevent every breakdown, but it can certainly greatly reduce it.
“The amount of concrete paved and the hours on the job determines the timing of maintenance,” he adds, “but frequently servicing the paver [as well as keeping it clean] is key to uptime.”
“Simple maintenance procedures like changing the oil at the recommended intervals will extend the life of the components,” says Bowman. “If maintenance is not performed, costs incurred could range from a simple seal to a new engine.”
Premature failure in a concrete paver can stem from the same areas you may see with other types of road building equipment, such as hydraulic and electrical systems. “In addition, the concrete itself can cause problems,” Bowman notes. “For instance, if certain systems are not greased and gaskets are not maintained, concrete grout will work its way in and destroy them. This can be prevented through strict adherence to all maintenance schedules, and fastidious cleaning.”
A sensor or wiring failure could also cause a slipform paver to fail. “Some contractors are finicky about their sensors and wiring, and they should be,” says Clausen. “Pay special attention to the cable connecting the sensor to the prime mover. Check it daily to make sure it isn’t pinched or caught on a stake.” In an effort to reduce downtime, many contractors carry extra sensors, cables and parts to repair their pavers in the field.
Vibrators are another area prone to failure on a slipform paver. “Two of the main reasons vibrators fail are overheating and dirt contamination,” says Maupin. “When the vibrators are vibrating in concrete, the concrete cools them. However, when testing vibrators before a job, they have nothing to cool them and can easily overheat. One trick to help with this is to test them one at a time in a bucket of water so they stay cooled.”
“Vibrators shouldn’t be allowed to run out of concrete for more than a minute,” Clausen advises. He also recommends frequently checking vibrator speed to ensure proper vibrations per minute.
Vibrator dirt contamination originates when vibrators are disconnected and left unprotected. “When disconnected, dirt builds up on the quick-disconnect couplings,” Maupin explains. “Once they are connected back into the machine, the dirt build-up enters the hydraulic system. An easy way to prevent this is to plug the quick-disconnect couplings into each other when they are not in use.”
Dedicate Consistent Attention
Basic preventive maintenance (PM) starts with a daily walkaround inspection. During this inspection, all paver functions should be checked for proper operation, and the area surrounding and under the paver should be checked for leaks.
The checkup can be done at the end of the day (or after 10 hours of use) following cleaning, before operation in the morning or start of the next shift, or a combination of both. Areas to inspect include:
- nuts and bolts to make sure they’re not loose
- fluid levels (engine oil, hydraulic oil, transmission fluid and engine coolant)
- areas under and around the paver for signs of leaks
- grease points (Note: fittings take grease better when everything is still hot)
- tracks to verify tension
- cables
- sensors
- linkages
- battery fill and fuel levels
Daily checks should also include greasing components. However, take care to avoid over greasing. “All grease points should be performed at recommended intervals, but there is such a thing as too much grease,” says Bowman. “A buildup of grease will attract dirt and concrete, making a paste. That paste can be extremely abrasive, which is just one more reason daily cleaning of the machine is the best maintenance you can do.”
Each paver’s operator service manual will detail what maintenance tasks should be completed weekly (after 50 hours), monthly/quarterly (after 150 to 250 hours) and annually (after 500 to 1,000 hours).
According to GOMACO, weekly maintenance should include checking oil levels in the track drive, pump drive and auger drive gearboxes, as well as checking the battery electrolyte level and alternator and fan belt tension. PTA sprockets should be greased, and the track tension and auger drive chain should be adjusted.
After 150 to 250 hours, be sure to drain the engine oil and replace the oil filter, and change fuel filters. In between, check:
- torque track drive sprocket bolts
- grease points including inner legs, track yoke pivot pin, sideplate tubes and slides, lower leg bearing and fan bearings
- lower leg clamps
Pay particular attention to safety features and ensure the emergency stop system works properly. “This stops all functions of the machine and it should not be bypassed,” Clausen emphasizes.
Annual maintenance should include replacing the air, hydraulic oil and high-pressure lift filters if operating conditions haven’t dictated more frequent changes. Sump filters should also be removed and cleaned.
Other yearly PM includes changing the oil in the track drive, pump drive and auger drive gearboxes, as well as adjusting the tamper bar, grout box auger, track, vibrator, main lift and air and water pressures. The frame clamp, track drive pump stroke control and auger main relief valves should be checked and adjusted, along with calibrating track EDCs, slope sensors and the steering system.
In addition, during the off season, most owners rebuild or repair vibrators and repair tracks if needed.
New Pavers Offer Advantages
While the maintenance routines don’t really change for new concrete slipform pavers, they may be easier to manage.
“Electronic improvements in modern pavers offer advanced onboard diagnostics,” says Bouillon. “Now a flashing light will alert the operator of a fault code and where to look for it. On older pavers, if the operator wasn’t periodically checking concrete, a failing sensor wouldn’t be detected. Today, with onboard diagnostics, they don’t have to chase an electronic failure.”
In Iowa, electronic monitoring is one of four requirements for vibrators. “First, vibrators can be spaced no more than 16 in. apart. Second and third, they must be angled downward a minimum of 15° from horizontal and operate [from] 6,000 to 8,000 vpm. Lastly, electronic monitoring is required,” says Clausen.
Electronic monitoring can be a handy service tool. “If an operator notices vibration speed slowing down, then corrects it and discovers it slowing down again, it’s a good indication the vibrator is failing,” Clausen points out.
Of course, electronics also require maintenance. “Because a paver is a heavy piece of equipment that sits outside all its life, if it’s not sealed properly, moisture and dust can enter the control panels,” says Bouillon. “Make sure to periodically check the electronic control panels for moisture.”
Overall, slipform pavers of any size require diligent, consistent maintenance for optimum performance. “Any machine with moving parts — especially one working in a harsh environment with a material as abrasive as concrete — will always require considerable upkeep,” says Bowman. “Doing so will ensure a long and productive life of the machine.”