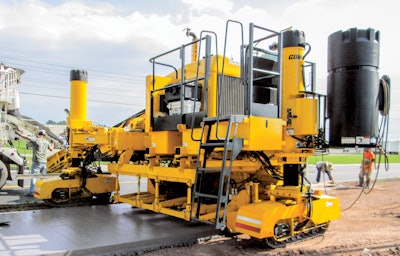
Curb Time Solutions in Russellville, AR, is a family run company specializing in commercial concrete and heavy highway work. Hannah Bowden is the owner and her father Jim and brother James each play crucial roles. Jim has worked behind concrete slipform machines most of his life and knows the intricacies of concrete very well. His experience proved crucial when it came time to order a new concrete slipform paver.
Jim had the opportunity to visit Diamond Materials’ jobsite in Cranbury, NJ, and watch their new GOMACO 3300 at work pouring 18-in.-tall stand-up curb. That visit was followed up with more discussions at World of Concrete in Las Vegas, and it was there that the decision was made for Curb Time Solutions to purchase the new paver, complete with both curb and gutter and sidewalk molds.
“The reason we went with the 3300 is because of its ability to pour multiple things,” Hannah explains. “Not only can we trim and pour curb and gutter with it, we can also do sidewalk, barrier wall, and bridge parapet.”
First Pour
The new paver was put to work on a project in Clarksville, AR, with 15,600 ft. of two different types of curb and gutter, as well as 8,200 ft. of 10-ft.-wide sidewalk. The profiles would be Arkansas State Highway and Transportation Department (AHTD) standard designs. The curb and gutter is 18 in. wide with a 6-in.-tall curb. The roll-over curb and gutter profile is 24 in. wide with a 4.75-in.-tall rolled curb.
This project would be Hannah’s first time operating the 3300 and putting concrete through the paver. “You don’t see female operators and owners very often,” says Hannah, “but here I am.”
The new paver was put to work on a project in Clarksville, AR, with 15,600 ft. of two different types of curb and gutter, as well as 8,200 ft. of 10-ft.-wide sidewalk.
“When you talk to GOMACO, you ask a question and you get an answer. If you need a part, they get you the part,” Hannah states. “Without that, you can’t run.”
The 3300 has a symmetrical configuration and has been designed for right-side and left-side pour capability. Its U-shaped operator’s platform ensures complete visibility of the paving process.
The Bowdens put the right-side pour capabilities to the test on the first day’s pour. “We like pouring from the right side because you’re going with the flow of traffic instead of against it,” Jim notes. “We can line up our concrete trucks right in front of the paver instead of trying to block traffic each time we need to get a truck in or out.”
The paver is also equipped with a 20-ft.-long folding conveyor with four-way hydraulic positioning for loading the hopper on either side of the paver. “With a conveyor you can see the mud better, you can know what the slump is and you move the concrete faster,” Jim points out.
Summers are extremely hot and humid in Arkansas. To compensate for the heat index, Curb Time Solution’s crew would sometimes start their day’s pour at 4 a.m.
“Our summer days will reach over 100 degrees F with 97% to 100% humidity,” Jim explains. “The mud can get hot by the second truck if we don’t start early. We’ll run chilled water and 3% retarder in the concrete mix to help out.”
Hannah, her chute person and Jim all wear headsets on site. The headsets allow for easy and instant communication between the key people while pouring. But there were still some initial communication challenges on that first pour.
“Trying to watch the hopper, trying to watch the vibrators and trying to make sure the concrete comes out right... the concrete was either too wet or too dry. The crew didn’t want to listen to me, even with the headset on. They’d just be doing their own thing,” Hannah comments. “Finally, Dad had to step up and say ‘Okay, you better start listening to her because she’s the one operating.’”
Once the communications issue was cleared up, paving progressed quickly. “My first day with the machine, I poured close to 2,600 ft. of curb and gutter,” Hannah says.
Another piece of technology incorporated into Curb Time Solutions’ projects is a drone with video camera. As the drone pilot, James flies the drone around all of the company’s projects recording site conditions before work begins. Then, if questions arise later, they have video proof showing the beginning condition of the job site. The drone is also a handy tool for tracking progress on projects.
Moving on to Sidewalks
With Hannah comfortable on the fundamentals of slipforming curb and gutter, it was time to master 10 -ft.-wide sidewalk. The city of Clarksville is putting in approximately 10 miles of new multi-use trails for walkers and bikers. The trail is slipformed with a cross slope and joints are every 10 ft. Expansion joints are saw cut in the next day at 50-ft. intervals.
The 3300’s curb and gutter mold, along with the hopper and trimmerhead, were removed and the paver was put into the transverse position so the mold could be center mounted underneath. The sidewalk mold is sectional and built to be open front or closed front, depending on jobsite requirements. It has adjustable side plates with up to 8 in. of adjustment on either side.
Ready-mix trucks dump directly onto the 3300’s conveyor, which moves the concrete into the hopper of the mold. A cross auger inside the sidewalk mold moves the concrete across the 10- ft. width.
Grade and steering was referenced off the new curb and gutter. The G+ control system was set to pave in the transverse right configuration.
Continued Learning
Hannah learned the fundamentals of the 3300, slipform paving and owning her own slipform paving company in her first season. But the learning process is ongoing.
This winter, Hannah, Jim and her company mechanic attended GOMACO University in Ida Grove, IA, for a week-long course. There they learned the finer details of the G+ control system and the 3300 in the classroom, in the hands-on shop time and from fellow University students - knowledge they can put to good use on their current and future projects.