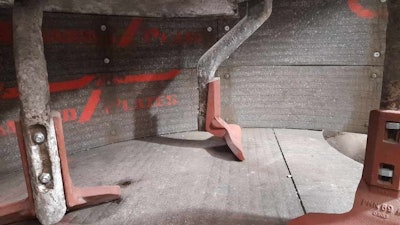
Concrete production businesses can now substantially reduce equipment downtime and related costs in the mixing and final production stages, thanks to the latest wearfacing technologies.
By the very nature of their function and operation, concrete mixers and concrete-handling accessories are continually subjected to a highly erosive, abrasive and mobile mixture of cement, sand, aggregates and water. These machine's capacity for intensive wear, tear and damage is huge but until a wearing component is replaced, its energy efficiency and operational performance may be lowered. This can lead to higher fuel consumption and in some cases higher material costs. It may also affect the quality of the concrete and increase the risk of its rejection.
The industry is under increasing pressure to deliver an uninterrupted flow of ready-mix concrete, produced with a consistent, homogeneous quality and with ever faster mixing cycles. This is especially true for precast and prestressed concrete. The rising cost of energy and raw materials is another driver of efficiency, as is the growing demand for sustainable use of resources and reduction of carbon emissions.
Protecting equipment and components from wear helps toward meeting all these demands. It not only extends their life but maintains their original shape and dimensions, so they perform optimally and energy-efficiently. Wearfacing treatments can be applied during the equipment’s original manufacture and preparation. Alternatively, they can be added as part of a repair and restoration process which gives the component a second life and a better-protected future.
Concrete Mixers
To understand the role of wear protection in concrete mixing, it is useful to first look at the anatomy and functioning of today’s concrete mixers. Fundamentally, they have a drum or pan in which the ingredients of concrete are stirred and homogenized with the aid of mixing tools. These consist of mixing arms to which are attached paddles for mixing and scrapers to stop the concrete from sticking to the drum or pan’s surface.
The arms are mounted on a rotating shaft which produces the necessary movement for stirring. More rarely, there are mixers in which the pan, rather than the mixing tools, revolves around a vertical axis. In older-style concrete mixers it was common for the drum to rotate around a horizontal axis, with the effect of mixing the contents by lifting and dropping them.
Concrete mixers can be divided into horizontal axis mixers (otherwise known as horizontal shaft or horizontal drive) and vertical axis/shaft/drive mixers. Within these, there are further divisions.
Most horizontal shaft mixers have two shafts, although single-shaft versions can be found occasionally. The twin-shaft machines offer high-intensity mixing with short cycles. They are typically used for high-strength, roller-compacted and self-consolidating concrete. Batch sizes tend to be between 70 and 211 cubic feet.
Vertical shaft mixers can be divided into pan types (sometimes known as ring-pan or turbine mixers) and planetary types (also known as counter-current mixers). Both kinds mix quickly and efficiently and are well suited to stiff as well as loose mixtures. The benefits of these machines include easy cleaning between batches. One of their differences from horizontal shaft mixers is that they discharge concrete via an opening in the bottom of the pan, rather than by pouring it from the top of a tilted drum.
Typical vertical shaft mixer applications include precast and prestressed concrete. The more efficient mixing action of the planetary types adds an advantage when consistency is most critical – in colored and self-consolidating concrete mixes, for example. Batch size for vertical shaft mixers is normally small – between 26 and 105 cubic feet – and they are often used where multiple discharge points are needed.
Castodur Diamond Plates (CDP), developed by Castolin Eutectic, can be easily cut, shaped and fitted to protect any surface in any mixer design. In tests, CDP plates have been shown to give up to five times longer service life when compared with previous solutions.Castolin Eutectic Corporation
Concrete Mixer Liners
An obvious place to start is by covering the inner surface of the mixer’s pan or drum with a protective lining. Some protective plates can be easily cut, shaped and fitted to protect any surface in any mixer design. These plates can provide high protection while concrete is being mixed and, importantly, during cleaning and maintenance. Quality plates should be highly resistant to chipping and are low weight for easy transport. A mixer's pan/drum protective plate are available with different alloys and thicknesses, designed for specific wear scenarios and categorized mainly as welded, powder, and laser cladded.
The plates provide an effective way of protecting both small and large surfaces. Retrofitting them is straightforward, with attachment by screws, rivets or spot welding. Make sure to know if your plates can be supplied pre-cut and formed to the mixer’s specifications. A 3D measuring arm may be used to ensure measuring accuracy. To maintain the best possible fit and function, given that mixers change shape over their life, new measurements should be taken for each replacement set.
Castolin Eutectic’s wear-resistant solution for paddle, scraper and arm protector surfaces is Laser Cladding. Components protected by LaserClad complex coating structure lasts up to six times longer than parts dependent on previous resistant technologies.Castolin Eutectic Corporation
Mixing tools
The mixing arms, paddles and scrapers in a concrete mixer are all considered to be replaceable parts. Also present in some are arm protectors, designed as an additional protective measure for vulnerable surfaces on the arms. Components protected by a complex coating structure are proven to last longer than parts dependent on previous resistant technologies.
For extra protection, some manufacturers apply tungsten carbide – with a hardness of 2,500 HV – to the leading edges of critical parts. Individual parts can be repaired again and again using the same wear-resistant alloy in electrode form. Coatings are available with different alloys and thicknesses designed to combat specific types of wear.
Castolin Eutectic's CastoTubes are protected internally by a welded coating of TeroMatec 4666 alloy, which is extremely wear-resistant. It gives the same level of wear resistance as Castolin Eutectic’s CDP 4666 plates but avoids the difficulty and expense of having to form plates into tubes.Castolin Eutectic Corporation
Pipework
Concrete ingredients and the resulting mixed concrete may be transported via a system of rigid, small-diameter pipes, with elbows for changes in direction. Their inner surface is, unsurprisingly, prone to erosive and abrasive wear. Internally hard surfaced tubes can range from 82 to 300 mm and are spiral welded to minimize distortion. The tubes are seamless, with perfectly round cross-sections and no linear weld joints. They are light to handle, and quick and easy to connect.
These custom alloys protect against high-temperature erosion.
Tube sections can be joined by simple welding or mechanical methods. The tubes can be delivered with integral or slip-on flanges, or with other flange joint types or custom connections upon request. Within the wide range of internal diameters, the precise wearfacing thickness can be varied to achieve a closely mating joint and avoid turbulent flow.
Final Production
There is a wide range of wear-resistant solutions for various equipment involved in forming concrete into the required shapes for construction.
Any shrinkage of these sleeves through wear decreases the size of the air cavity, which increases the amount of concrete used and the weight of the final product. Wear protection maintains the original geometry while extending useful service life.
Life of concrete spreaders, floor spreading equipment, augers and drawer table plates can all be extended using specialized wear technology. Preventive maintenance allows equipment to function optimally, consuming less energy, improving operational efficiency and the bottom line.