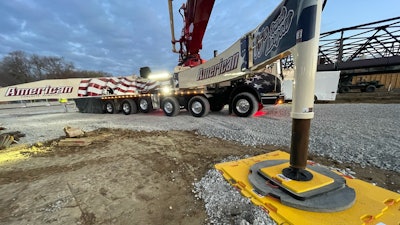
Concrete pump operators face significant challenges when setting up equipment on job sites. Ground conditions are often unlevel, have been disturbed, and are affected by weather conditions. When the ground is not strong enough to support the ground-bearing pressures exerted by the equipment, the result can be a pump truck that tips over. “Better education is needed on how to spread the load. Tipovers due to improper ground conditions are among the top three types of accidents involving pump trucks,” says Kyle Rask, Program Manager – Concrete Pumping for NBIS Construction & Transport Insurance Services, Inc.
The Challenges
Operators are often working alone in situations where risk levels are high. They are tasked with getting in and out of job sites quickly, with limited advance information about the site conditions and available set up space. The American Concrete Pumping Association (ACPA) recommends in its Safety Bulletin on setting outriggers that “setting the outriggers of a concrete pump is one of the most critical jobs of the concrete pump operator. If not done properly, it can lead to a serious accident.” When a pump truck tips, it’s often the person holding the hose or other workers in the area that get hurt, explains Rask.
“NBIS recommends amending the daily work ticket or rental ticket to show ground bearing pressure and PSI requirements for the pump truck on the contract.”
—Kyle Rask, Program Manager – Concrete Pumping for NBIS Construction & Transport Insurance Services, Inc.
By design, to keep the vehicle width within DOT restrictions, standard outrigger floats on concrete pump trucks are between 12 to 16 inches in diameter. These small outrigger floats contribute to extremely high ground-bearing pressures. In fact, the ground-bearing pressures created by larger concrete pump trucks are often significantly higher than those created by most cranes.
This situation becomes more complicated because the ground in and around the setup area is often disturbed. This creates a scenario where the equipment pressures are high, and the ground to support the equipment is generally unknown. Jim Manson, President of Sun Concrete Pumping in Grimes, Iowa, explains another consideration. “Pump trucks experience pulsing as concrete is pumped through the boom. This can cause outrigger pads to get pushed into the ground if the pads aren’t large enough or if the ground is not strong enough.”
Dunnage or outrigger pads are a critical piece of the solution, but dunnage needs to be made of a material that is strong enough to withstand the imposed forces and stiff enough to prevent excessive deflection. “Operators are often scrambling at the job site to find materials to use for dunnage, but wood breaks and warps. We recommend using after-market, engineered outrigger pads that are designed for the application,” says Rask.
Concrete contractors should discuss and plan minimum ground bearing capacity requirements with the general contractor before arriving on site.DICA
Solutions
Because many pumping jobs require the operator to fully extend the boom, operators should assume they will generate the maximum outrigger reaction force on each job. Fortunately, ASME standards require concrete pump manufacturers to post the maximum outrigger reaction forces on each outrigger leg. Rask suggests that concrete contractors communicate this information and the ground psi requirements for the pump truck to the general contractor in advance, requesting that they supply appropriately sized outrigger pads. “Unlike the crane industry, there is not ‘controlling entity’ language in OSHA regulations that requires the site owner to prepare the ground, but there is a growing awareness about the risks of not preparing the site,” says Rask. Most concrete pump trucks have limited available space for transporting dunnage on the pump truck, making coordination with the general contractor even more important. Rask says: “NBIS recommends amending the daily work ticket or rental ticket to show ground bearing pressure and PSI requirements for the pump truck on the contract.”
Punch through failures occur when dunnage materials are not strong enough or the load distribution area is not large enough for the ground to support the pressures imposed. Armed with this information, concrete contractors can continue the conversation with GCs to meet the majority of pump truck setup scenarios. DICA recommends the following approach.
- Always know your numbers. Begin with the maximum outrigger reaction force and allowable ground bearing pressure.
- Select a pad or dunnage solution with the strength to support the load and pressure so it will not physically fail.
- Select a pad or dunnage solution with the appropriate stiffness to effectively distribute the load over the intended area.
Engineered outrigger pad solutions like DICA’s SafetyTech and FiberTech are available in many different shapes and sizes. The company uses a 3-step fitting process to discuss the specific limitations of each pump truck and the setup challenges to provide solutions.
Risk Mitigation Trends
“There is growing awareness of these issues and it is being addressed on a state-by-state basis in OSHA-approved State Plans. In lieu of defined responsibilities, the best practice is for the pump operator to review adequate site prep with the controlling entity before work begins, on a daily basis,” says Rask.
Last year, the National Commission for the Certification of Crane Operators launched a new certification for operators of concrete pumps. The CCO certification program tests knowledge of operational concepts and industry standards, such as ASME B30.27. Pump set up is one of six knowledge areas covered.
Rask says the CCO program joins others available in the market, such as the American Concrete Pumping Association’s ACPA Certification, which now requires as a prerequisite that operators complete Operator Training. In British Columbia, WorkSafeBC amended its regulation making certification mandatory in the province beginning next year.
“We know that education and training is a good thing. I believe we will see fewer incidents as a result of these certification programs,” says Rask. “Certification gives operators the power to say ‘no’ if they are put into situations where the ground or setup conditions are not appropriate. This will have a big influence on continuing to shift attitudes,” says Rask.
About the author
Kris Koberg is the CEO of DICA, a family-owned and operated company that specializes in building high performance engineered outrigger pads, crane pads, and cribbing blocks that are lightweight, easy to use, and long-lasting. DICA products are proudly Made in the USA, ASME B30.5 compliant and used by operators in 40+ countries around the world.
Pump owners/operators are put in compromised positions daily. DICA is committed to doing its part to help reduce risk, increase safety and provide peace of mind. This is our Purpose, and it’s our passion.