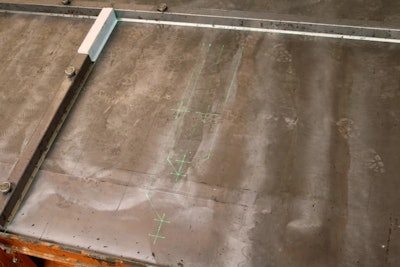
Laser projection systems by SL Laser meet the needs of its customers in the construction industry and in the production of prefabricated concrete components. Using a computer-controlled laser system and software, work plans and measuring points can be transferred even for large or angled assembly areas. In the precast concrete industry, the ProDirector enables the positioning of formwork, built-in parts and reinforcements. The laser can be permanently installed above a table or mounted on rails for long tracks.
ProDirector
Used on a rail system, the laser projector moves from position to position along a long track. A second laser projector in the same rail system can project a drawing at a different position on the track - or display a large drawing together with the other laser projector. In this way, two independent teams can also work independently on different projects on a long track without having to wait for the laser. Several projects can be completed at the same time. The track system can also be equipped with more than two lasers.
Laserpilot Software
A complete path can be predefined using a CAD system. The laser projector processes project by project. Each time the projector stops at a certain position, all the elements to be used are projected. These elements are stored on different layers so that the different components can also be displayed with a remote control or via the Laserpilot software. This software imports all common formats for projection, be it DXF, DWG, ULB or HPGL. Customer-specific data formats are tested by SL Laser in advance and the programming options are discussed with the customer. The laser projectors also work together with other well-known control systems.
SL Laser
Laser Projection in Precast Plants
The laser projectors in the precast plants save users the time-consuming task of manually measuring the positions for the formwork, empty conduits and built-in parts. The templates are imported directly 1:1 from CAD. The contours are projected to scale onto the tables. The Laserpilot software makes it possible to generate a surface for various applications in the precast industry. Depending on requirements, the adaptations are discussed with the customer and transferred to the software interface.
This is done by loading the file and is realized by calibrating, rotating, turning and mirroring. The template can also be rotated in the x and y directions or projected at a different z-height. Projection at a different z-height unlocks various capabilities. For example, the line on the upper edge of a support or another component is easier to see than at height 0, as shadows often occur at this height. The angle of the component can also be taken into account. Many of these functions can be placed on the remote control so that the user can use them with a click.