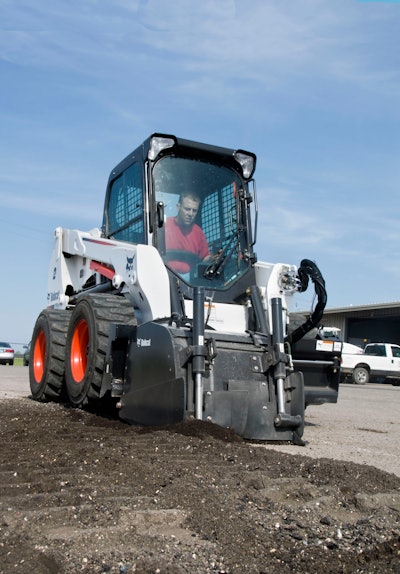
Cold planer attachments can work shallowly, providing just what’s needed to remove paint lines from parking lots, airports, etc. They can also mill deeply to cut through concrete or one or more layers of asphalt for repairing streets, highways, sidewalks, etc. But in order to efficiently and productively perform these and other jobs, it’s important to match the attachment to both the carrier and the tasks.
“Peak performance starts with proper matching of the attachment and the host machine’s provided power to the application,” says Adam Runner, special projects manager, Coneqtec-Universal. “A small, low-flow planer used for parking lot patch repair will probably be disappointing if used for deep milling or concrete work.”
Pay Attention to Hydraulic Needs
Improper pairing of the attachment to the capabilities of the carrier is one of the most common mistakes contractors make, says Larry Giberson, owner, GECON Attachments.
“An under-powered skid steer, both in terms of pushing power and hydraulic power — meaning adequate pressures and flows — won’t perform to expectations,” he notes. “If the attachment can’t get its required ‘juice,’ then it will only be partially productive. While nothing bad can really happen to the carrier, the wheels [of a skid steer] may spin or break traction, and the performance of the attachment will be less than can be achieved. Wheel wear costs can also go up if the machine is undersized.”
One of the first steps is to match the hydraulic needs of the attachment with those provided by the host machine. Unfortunately, there are a lot of misconceptions surrounding hydraulics, especially auxiliary power.
“It is important to know what hydraulic horsepower (hhp) is available for each [carrier] that will be running attachments,” says Runner. “It is not the host machine’s engine power but rather the hydraulic horsepower that is available... The host machine will need to deliver enough power to the attachment for it to operate productively. Minimal requirements may not cut it if the application is more demanding, such as milling 2 in. deep vs. 6 in. deep.”
Mike McSorley, field product support and training, Paladin Attachments, agrees, adding, “It’s important to understand the hydraulic performance of the machine. When you read the specifications, manufacturers are talking about gross hydraulic performance. That doesn’t necessarily mean you will yield 100% of those hydraulics through the attachment coupling system that attaches it to the machine. A lot of people have the presumption that all of the hydraulic flow is going to the attachment when it isn’t. There are other demands on the hydraulics, such as what is needed for an undercarriage.”
When acquiring a new machine, McSorley suggests checking with the dealership to confirm its actual hydraulic performance. You can confirm hydraulic flow and pressure via field service trucks, as well.
Runner also stresses that the hydraulic horsepower of a system must be calculated, rather than following what is stated as the amount of flow. “This would be similar to stating the horsepower of a truck is simply its torque,” he points out.
He offers the following calculation to determine hydraulic horsepower: multiply the system’s flow by its pressure, then divide by 1,714 (gpm x psi/1,714). “To be more accurate, knock off another 10% for inefficiencies, e.g. heat loss, etc.,” he says. “A hydraulic system with a lower flow rate at higher pressure can have more horsepower than a higher flowing system with lower pressure.”
To estimate the planer’s hydraulic horsepower requirement, multiply the drum width by 2. “That means, for example, a 24-in.-wide planer would require a host system with at least 48 hhp to run efficiently,” says Runner. “If a contractor anticipates deep milling or concrete work, he might want to multiply the drum width by 2.5 or 3 to find the minimum hhp required for the application.”
When selecting a loader to be used with a cold planer, Katie Althoff, attachments product specialist, Bobcat, suggests it is best to stay at the high end of the machine’s flow range. “If you are on the low end of the range, you will have less performance,” she says. “It will feel like the attachment is under-performing and not getting enough flow. With a planer attachment, there is a lot of resistance as you cut through the material. To get the best performance, you want to get as much flow going through the attachment as possible. A high-flow loader will also help improve performance.”
Runner advises paying attention to high-flow vs. low-flow requirements. “There will be problems if a high-flow attachment is mounted on a host with low-flow hydraulics,” he says. “There are also various hydraulic line configurations (three-line, five-line, etc.) on host machines that will need to be matched or accommodated.”
Bigger Isn’t Always Better
Another common misstep is selecting the wrong size of attachment. While cold planers can make cuts as wide as 40 in., wider isn’t always better.
“There is a misconception that a wider cut will give more productivity,” says McSorley, who notes that Paladin planers range in widths from 16 to 40 in. “But in fact, it slows down forward progress.”
Cold planer attachments can weigh up to 2,500 lbs. “Combined with the weight of the host machine, you are trying to push a lot through a road bed,” McSorley comments. “Oftentimes, contractors are better off making multiple passes with an 18- or 24-in. attachment rather than trying to do it all at once with a wider one. Multiple passes is a more efficient use of the hydraulic system, and it extends the service life of cutting teeth on the drum.”
Likewise, cutting too deep all at once can be a mistake. “The most efficient use of carbide tools [for asphalt] is to cut somewhere between 1.5 to 2 in. in depth,” says McSorley. “That will keep the tool in the asphalt just long enough so it can rotate and have a chance to cool down a bit.”
Consider Host Specifications
There are considerations when choosing a host machine for a planer attachment. Carriers are typically skid steers, compact track loaders or excavators, but may also include backhoe-loaders and wheel loaders.
McSorley advises using a skid-steer loader over a compact track loader. “A compact track loader is designed with an undercarriage and tracks to diminish ground pressure and improve flotation,” he says. “That undercarriage is very expensive. As you work on concrete or asphalt, it wears the rubber tracks quickly.”
To reduce tire wear on skid steers in this application, Althoff suggests Bobcat’s all-wheel-steer option. “All-wheel steer gives you the ability to move the wheels in a crab-like position,” she states. “That means you will have less skidding, but you will still get plenty of maneuverability. Some contractors have told us they have extended tire life four to five times when using the machine in all-wheel-steer mode.”
Operating system preferences can come into play when choosing a host machine. A joystick can make a planer attachment easier to operate, notes Althoff. “You aren’t ‘feathering’ much so you don’t need to keep touching a handle,” she says. “With a joystick, you can ‘dial’ it in by selecting how fast you want to travel, which is generally slow, which will keep the torque high. Then you can drive without having to worry about adjusting your speed. You can dial into your sweet spot and maintain maximum driveline torque and full hydraulic power.”
Maintaining a constant speed is less taxing on the operator, as well. “It is one less thing they have to focus on,” says Althoff. “Operators don’t have to rock back and forth to maintain speed. This offers a nice, constant biting away at the asphalt for a cleaner cut, better performance and less feedback to the operator. You will get better fuel efficiency for the loader, as well.”
According to McSorley, Bradco’s joystick controller can make operation easier. “Setting up the three or four functions (depending on which style planer is purchased) is more easily controlled by using our joystick controller because the left side operates independent of the right side,” he says. “And if your machine goes down, you can immediately pick up the cold planer and move it to any other high-flow machine and go right back to work.”
GECON Attachments offers a “performer” enhancement feature to show an operator an easily visible measure of the most efficient way to do a job, eliminating the guesswork and any too slow or too fast operation. The company also offers a universal wiring harness. “That means anyone with a high-flow skid steer can run our planer with a conveyor,” says Giberson. “If a contractor has more of a particular brand of skid steer in the fleet, this would allow for changing the carrier and putting the planer on a different skid steer without having to plug in a different wiring harness. We also have a pigtail adapter to match any brand skid steer to the planer so the skid steer’s joystick and controls can be used.”
Built-in conveyors are becoming popular options, Giberson asserts. “A built-in conveyor allows for 90% to 95% of the trench to be clean every pass,” he says. “That saves time and labor, as well as minimizes a lot of unnecessary wear and tear on sweeper brooms.”
Choose the Right Drum
At the heart of the cold planer attachment is the drum, with varying options offered by manufacturers.
“Contractors need to understand there is a significant difference in drum design and configuration for concrete vs. asphalt,” says Giberson. “The best advice we can give is that there needs to be a mindset that there are two totally different applications in the field.
“Most planers are set up to attack asphalt,” he continues. “But just changing the pics, or teeth, is not the best answer because drum construction, placement of pic holders, pic composition and total number of teeth are different for milling concrete vs. asphalt.”
Concrete exacts more of a toll on equipment and wear parts. “Milling concrete with an asphalt setup will lead to less production and considerably more wear cost,” says Giberson. “The smart thing to do is invest in an extra/spare drum and teeth for concrete if you know you will be doing jobs with concrete.”
Bobcat offers different drum types on its planer attachments. “Fast-cut” drums have fewer bits to mill asphalt quickly with a relatively fine end product and scarified surface for patching or layering asphalt. The drum can mill more deeply (3 to 4 in.), depending on hydraulic flow and how much oil is in the asphalt. “Surface” or “smooth-cut” drums are typically used on concrete where a shallower cut is needed, such as when removing paint lines. “They mill more slowly and only about 1/16 to 1/8 in. deep,” says Althoff. “Once the spoils have been cleaned away, your surface will be smooth.”
Coneqtec-Universal offers an open drum design that features staggered, offset plates with the grinding bits attached to the perimeter of the plates rather than a barrel. “The open drum has proven to be much more productive and efficient due to the elimination of regrinding the aggregate,” Runner explains. “With closed drums, much of the spoil is thrown back over the drum and ground repeatedly into a fine dust. Open drums have the advantage of the spoil falling between the plates and left in the planing path without regrinding.”
Paladin provides one drum type for its Bradco planers and another for its FFC planers, each offering its own scarification pattern. “The FFC model cuts deep because of the pattern on the drum and the placement and shape of the carbide cutting tools,” says McSorley. “It’s designed to cut deep in a single pass, piercing through the road deck and into the sub base. It’s a great choice for cross cuts or lateral cuts to replace plumbing pipe or drain tile.
“The Bradco unit is typically favored by contractors who are interested in weight, torque, rear spoils clearance and quality of the scarification pattern,” he adds. “It gives more bondable surface, offering a place for more adhesion to occur.”
The 40-in. GECON PL-C planer attachment has a split-drum design that can be split into two halves in a combination of three configurations: 20” + 20”, 16” + 24” or 24” + 16”. “This feature allows for removal of one of the sections that is a type of clamp-on half shell and leaves the smaller (milling) area for more flexible milling,” says Giberson. When a section of the drum is removed, the scraper and conveyer must also be disconnected. “The segmented planer will act just as a basic planer with no trench cleaning unless the full drum is in place.”