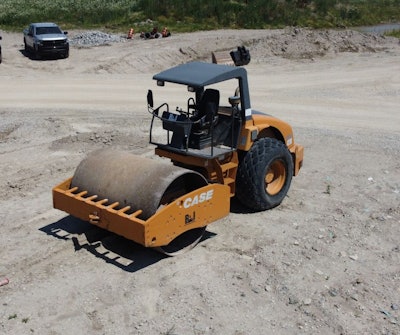
Proper soil compaction is crucial for both small and large construction projects because it increases soil density and load bearing, ensuring the stability, durability, and longevity of buildings and structures. Choosing the right compaction equipment is the starting point for any effective compaction strategy.
In soil compaction for foundation preparation, four primary types of compaction equipment are smooth drum soil compactors; padfoot soil compactors; tandem rollers, also known as road or asphalt rollers; and combination rollers. Each type has unique features and applications, which will be highlighted in this article.
Smooth Drum Soil Compactors
Smooth drum soil compactors are used primarily for compaction of granular soils such as sand, gravel and crushed rock. They consist of a large, smooth drum at the front, which vibrates to compact the soil underneath. These machines come in various sizes and configurations, from smaller walk-behind models to large, ride-on units. The vibrating drum generates high-frequency vibrations that help achieve deep soil compaction. Modern models offer adjustable vibration settings to suit different soil conditions and compaction requirements.
Smooth drum compactors are best suited for road construction, where they are ideal for compacting base layers and sub-base layers of roads. They are also used for preparing building foundations by compacting granular soils and are effective in creating stable, well-compacted layers. For optimal results, these compactors should be used on sandy and gravelly soils where fine particles need to be packed tightly. They are ideal for final surface preparation where a smooth, flat finish is required, and models with high-frequency vibration are recommended for deeper compaction needs.
Padfoot Soil Compactors
Padfoot soil compactors, also known as sheepsfoot rollers, are designed for the compaction of cohesive and semi-cohesive soils like clay and silt. These compactors feature a drum equipped with metal knobs that penetrate the soil to compact it from within. The design allows for both static and dynamic compaction. Capable of operating in both static and vibratory modes for versatile compaction, many models also include self-cleaning systems to prevent soil buildup on the drum.
Padfoot soil compactors are most effective in projects with high water tables like dams and embankments, where they are essential for compacting clay cores and other cohesive materials. They are also ideal for compacting backfill materials in utility trenches and pipeline projects and for compacting waste and soil layers in landfill operations. When dealing with cohesive soils, padfoot compactors are the preferred choice due to their ability to knead and bond the soil effectively.
BOMAG padfoot roller.DOZR
Tandem Rollers
Road rollers, commonly referred to as tandem rollers or double drum rollers, are primarily used for asphalt compaction in road construction. They feature two smooth drums, one at the front and one at the rear, which provide even compaction. These rollers can operate in static mode or with vibration, depending on the requirements. The dual drum configuration ensures even distribution of compaction force across the surface, and the ability to switch between vibratory and static modes offers flexibility based on compaction needs.
These rollers are the best choice for projects involving asphalt layers, where smooth and even compaction is necessary. They are also ideal for final passes to achieve a polished, even surface on paved areas and are suitable for a variety of surfaces, including pavements, bike paths and pedestrian walkways.
Combination Rollers
The last type of compactor to highlight is combi rollers, also known as combination rollers. They are versatile machines that combine the capabilities of both smooth drum rollers and pneumatic tire rollers into a single unit. They feature a smooth drum at the front and pneumatic tires at the rear. This design allows combi rollers to effectively compact a wide range of materials, including both soil and asphalt surfaces.
The smooth drum is ideal for achieving a dense, even finish on asphalt layers and compacting granular soils. The pneumatic tires provide better compaction on cohesive soils and help to avoid surface damage on delicate asphalt layers. Combi rollers are particularly useful in road construction and rehabilitation projects where flexibility and efficiency in compaction are essential.
Wacker Neuson double drum roller.DOZR
Vibration
All the compactors above are a type of vibratory roller consisting of a rotating mass within the drum. As this mass rotates, it creates centrifugal force, causing the drum to vibrate rapidly. These vibrations reduce the air pockets between particles in the material being compacted, increasing its density and stability. The frequency and amplitude of the vibrations can typically be adjusted to optimize compaction for different materials and project requirements. This vibration is what allows construction workers to create a load-bearing, stable foundation for any building type to avoid long-term damage.
Soil compactors have a few distinct drum width sizes, including 48 inches, 56 inches, 66 inches and 84 inches, and some smaller hand-held and walk-behind models. The smaller compactors are useful for preparing the ground in smaller, tighter spaces like parks, walkways and residential roads. Larger models with wider 66-inch and 84-inch drums are often used on large-scale infrastructure projects like commercial site preparation or highway and interstate projects.
Selection & Maintenance
To maximize the effectiveness of compaction equipment, consider best practices, such as conducting a thorough assessment of soil type and moisture content, to select the appropriate compaction equipment. Compact soil in thin layers and multiple passes to ensure uniform density and prevent voids. Maintaining optimal moisture levels in the soil facilitates better compaction and prevents issues like excessive dust or soil sticking to the drum. Regularly inspect and maintain compaction equipment to ensure optimal performance and longevity, and ensure operators are well-trained in using the equipment, understanding its features, and implementing best compaction practices. The ground should also always be tested for its soil density before building.
Selecting the right compaction equipment is crucial for the success of any construction project. Smooth drum soil compactors, padfoot soil compactors, tandem rollers, and combi rollers each serve specific purposes and soil types. Understanding their features, applications and best use cases will enable you to achieve optimal soil compaction, leading to more stable and durable structures. By following best practices and leveraging the strengths of each type of compactor, construction professionals can ensure high-quality results in their projects.