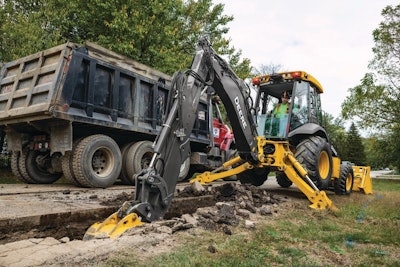
As jobsites continue to become smaller and smaller, and advancements in hydraulic and engine systems occur at an exceedingly fast pace, operators are demanding compact, powerful machines that enable them to complete their tasks as accurately, consistently and quickly as possible.
In response, the construction industry is integrating performance and power into smaller machines that have been created to accept several attachments, thereby enhancing operators’ productivity even on the most demanding jobsites.
One such machine is JCB’s purpose-built 1CXT backhoe-loader, which offers operators high efficiency, as it can perform in any type of application, while providing them comfort and ease of use, too. Highly maneuverable as well, the 1CXT also has a universal quick hitch that’s compatible with a majority of skid steer attachments. And it is easy for operators to trailer and tow it, often without a commercial driver's license (CDL), as a result of its compact size and weight.
JCB’s purpose-built 1CXT backhoe-loader, which offers operators high efficiency, can perform in any type of application, while providing them comfort and ease of use, too.JCB
“Due to its compactness, the 1CXT can also be easily transported and operated in confined workspaces,” said Ethan Clowes, product manager, skid steer/compact track loaders and backhoe-loaders at JCB. “With a standard skid steer hitch, it has a unique front loader design as well, which ensures a 25% greater dump angle and 15% more breakout. Furthermore, for high-sided trucks, it has a load over height that’s 8 ft., 8 in., resulting in smooth loading.”
He added, “With a fully-integrated side-shift backhoe, the 1CXT can dig close to walls for ease, too—digging up to 10 ft., 1 in., with the extending dipper option. By offering 12 ft., 10 in., of ground-level reach, the backhoe-loader also enables users to maximize their productivity by minimizing their need to reposition it.”
Despite its compactness, the 1CXT has a spacious cab that ensures operators are comfortable. It also has ergonomically designed controls that reduce operators’ fatigue. And it requires less downtime than other backhoe-loaders, as its engine has a 500-hour service interval.
Of equal importance, it offers operators a wide, one-piece engine cover, too, as well as removable side panels that provide them fast, ground-level access to daily checkpoints and routine service items. Featuring a side-mounted, 11.9-gal. fuel tank as well, the 1CXT can be used for long working stints and easily refueled, as it has a long filler neck that decreases the likelihood of spillage.
“In addition, the 1CXT has an innovative side-door entry and all-round visibility—through the cab’s large, laminated front window and toughened glass,” Clowes said.
Technology Offerings Positively Impact Backhoe-loaders
Aside from the 1CXT, a variety of other backhoe-loader technology offerings also stand out, including those that improve precision and stability during loader applications (like self-leveling and ride control) and those that enhance power delivery whenever necessary (such as power lift and power boost). Pilot controls and loader arms, along with the designs of loaders’ backhoes themselves, are presently standing out too.
According to Ryan Anderson, product marketing manager for backhoe-loaders, New Holland Construction, pilot controls, particularly on backhoe-loaders like the company’s D Series, utilize a variable displacement pump, leading to more controllability for operators. Since they’re considered a “hydraulic over hydraulic” design, pilot controls also provide operators more functionality for precision digging.
“An example of this would be precision swing control, which prevents backhoe arm movement and shaking when operators dig and unload the bucket to a pile,” he said. “This stops unwanted material from spilling back into the excavated hole, or adds an extra level of precision when operators place loads like wall blocks.”
Moreover, pilot controls offer operators features like return to dig and ride control—features that, according to Anderson, are critical for ensuring backhoe-loaders are as productive as possible throughout the materials handling process. In the meantime, current backhoe-loaders have straight or curved loader arms too, each of which performs differently for different reasons. For instance, straight loader arms provide operators two main advantages: improved lift capacity and higher visibility to the loader bucket. Curved loader arms, on the other hand, offer an enhanced bucket breakout force, along with a more precise placement of loads as operators utilize them since curved loader arms are closer to backhoe-loaders than straight loader arms are.
“Concerning backhoe design, operators can utilize internal and external slide hydraulically-extendable dippers (HEDs),” Anderson said. “Internal slide HEDs like New Holland Construction’s offer high lift capacity with the dipper, as well as less wear and tear on the HED itself since debris, dirt and rocks aren’t able to fall into the sliding mechanism. To compare, external slide HEDs provide more versatility for hydraulic thumb placement on the dipper though.”
Electro-hydraulic seat-mounted control systems also stand out presently, particularly those that are provided with Caterpillar’s 420 XE, 440 and 450 backhoe-loaders. Rather than providing operators two sets of controls—one for the loader and one for the hoe—the electro-hydraulic seat-mounted control system ensures one pair of joysticks is mounted to each backhoe-loader’s seat instead. This pair of joysticks will also travel with operators as they turn from the front to the back and from the back to the front.
Caterpillar is focused on continuing to build upon its electro-hydraulic platform, regarding the 420 XE, 440 and 450 backhoe-loaders that presently utilize the electro-hydraulic seat-mounted control system.Caterpillar
“The technology behind the control offering provides a feature known as ‘Dual Mode’, which allows operators to manipulate or control the implement he or she is not facing,” said David Young, product application specialist, Caterpillar. “For example, if an operator is facing the hoe, they can use the feature to change the RH joystick so that it becomes the loader control, thereby enabling the operator to reposition much more efficiently while running the hoe.”
He continued, “Likewise, operators can be faced forward and use the ‘Dual Mode’ feature to control all functions of the hoe. Lastly, the feature also allows operators to dig with the hoe anywhere in the swing arc of the loader’s seat. So, at any point between being latched forward or rearward, operators can use both implements.”
John Deere Construction Equipment, in the meantime, also has various current backhoe-loader technologies that particularly stand out. After all, according to Justin Steger, solutions marketing manager at John Deere, the company’s backhoes are especially focused on providing operators a reliable, straightforward way for them to operate their backhoe-loaders in a manner that ensures consistently high performance.
To do so, the company offers operators the John Deere PowerTech EWL engine, which eliminates any necessity for a diesel particulate filter (DPF) and exhaust gas recirculation (EGR) system. Utilized for four models of John Deere backhoe-loaders—the 310L, 310SL, 410L and 710L—the engine has more reliability than previously released engines, as well as enhanced torque and a 3% to 7% increase in net horsepower, improvements that underground utility operators will especially notice.
Additionally, the 310SL, 410L and 710L models of backhoe-loaders utilize pressure-compensated, load sensing (PCLS) hydraulics, which provide improved multifunctioning, smoother machine control and up to 15% higher craning capacity, via Lift Mode, than other hydraulics released by the company in the past.
“Collectively, the John Deere PowerTech EWL engine and the PCLS hydraulics offer operators distinct customer experiences, along with high machine reliability,” Steger said.
Stressing that “John Deere is committed to developing innovative, robustly tested and reliable equipment” for its customers, the company is, in turn, focused on “unlocking measurable value through the incorporation of smart technology solutions” in its machines.
“As it relates to other types of backhoe-loader equipment, John Deere continuously evaluates the needs of its customers and develops products that meet those needs,” he said. “To do so, at this moment, John Deere is focused on its electric backhoe prototype too, and is continuing its product testing and development process.”
Backhoe-loader Manufacturers Focus on the Future
In preparation for the future, JCB is focused primarily on sustainability, first and foremost.
“It’s no surprise to any in the industry that the next progression of backhoe-loader technology is tied directly to sustainability efforts,” Clowes said. “How can we look after the planet, while providing the same performance, safety and efficiency for which we are known? In short, how can we find a better way of getting the job done as a manufacturer, as well as machine operators?”
For answers to these two questions, JCB has introduced innovations that are focused on hydrogen engines. In particular, the company’s hydrogen combustion engine—the construction industry’s first-ever hydrogen engine—enables its advanced engine technology to be utilized for decades to come. Yet, at the same time, due to the potential of completely renewable hydrogen fuel, the engine may possibly have zero-carbon emissions one day too.
“The hydrogen combustion engine is an example of JCB accepting today’s challenge for tomorrow,” Clowes said. “When we consider replacing fossil fuels with a zero-carbon alternative that still allows heavy machines to do heavy work for up to 12 hours each and every day, it’s obvious that batteries aren’t practical for machines with high power demands and remote jobsites.”
He added, “Additionally, the weight, cost and charging time are prohibitive to the uptime and performance that operators expect out of a backhoe-loader.”
Thus far, JCB has produced a prototype backhoe-loader that utilizes the hydrogen combustion engine. According to Clowes, “it can do everything that its diesel-powered equivalent can do.” One key difference has been observed though: the hydrogen-powered backhoe-loader doesn’t emit any carbon dioxide at the point of use, as only steam is emitted from its tailpipe.
Alongside sustainability, there are four other driving factors for future technological enhancements, according to Anderson—a decline in risk, higher precision, more comfort and safety.
“For advancements in precision, 2D laser tools are becoming a staple in the backhoe-loader market,” Anderson said. “The usage of lasers and receivers in precision excavation and grading are proving to be the next level of profitability and productivity for backhoe-loader operators.”
With this in mind, New Holland Construction utilizes various suppliers, in order to acquire highly advanced lasers and receivers, including 2D self-leveling lasers and magnetized receivers. Providing highly accurate results, they can also be effortlessly installed and used in a straightforward fashion.
For safety, the company may eventually offer enhanced camera visibility around each of its backhoe-loaders too. Much like customers in the automotive industry, customers within the equipment industry desire to have bird’s eye, 360° views around their machines. As a result of this potentially improved visibility, customers will be able to operate their backhoe-loaders more safely than before. Furthermore, they’ll be able to minimize the risk of damage to their machines and property, while also decreasing the injuries of people who utilize them or are near them.
“The same comfort, visibility and safety features that operators have grown comfortable with in today’s cars, trucks and other motor vehicles will soon be available in New Holland Construction’s construction equipment,” Anderson said. “Operators’ abilities to confidently maneuver their backhoe-loaders around their jobsites without having to worry about damaging their equipment or jobsites—while also keeping their team members safe—will pay dividends in the form of less fatigue, less expenditures for their employers and better overall productivity.”
Electrification is the Name of the Game
Meanwhile, Caterpillar is focused on continuing to build upon its electro-hydraulic platform, regarding the 420 XE, 440 and 450 backhoe-loaders that presently utilize the electro-hydraulic seat-mounted control system. To achieve this goal, it is primarily interested in developing features that are generally found on excavators and loaders.
“On the hoe side, this would mean features like e-fence, e-ceiling and swing limits,” Young said. “On the loader side, Caterpillar is looking at payload measuring as well. In addition, the incorporation of grade control is on the table.”
As Caterpillar prepares for these future technology advances, the company is especially focused on efficiency and performance.
“These types of advanced features are being implemented with the following goals in mind—ensuring your backhoe-loader works faster, safer and at a higher level of quality than in the past,” he added.
John Deere, on the other hand, is preparing for the future by working with National Grid, an electricity, natural gas and clean energy delivery company. By doing so, it will joint test an electric backhoe concept. A John Deere- developed, battery-powered and electric vehicle design, the concept, known as E-Power, will mainly target the company’s diesel-powered, 100 HP 310L Backhoe’s ease of operation and performance level.
A John Deere-developed, battery-powered and electric vehicle design, the concept, known as E-Power, will mainly target the company’s diesel-powered, 100 HP 310L Backhoe’s ease of operation and performance level.John Deere
“The design is intended to provide substantially lower daily operating costs, along with enhanced machine reliability, lower jobsite noise and zero tailpipe emissions,” Steger said. “Currently, the electric backhoe concept is only being field tested, as it is not yet available to purchase.”
The E-Power backhoe has been created to perform the same operations and run the same attachments as a conventional diesel engine-powered backhoe—without sacrificing any of its versatility.
“Increased versatility comes in the form of customer and jobsite requirements, which, in the future, may drive the need for an E-Power backhoe,” he said. “Companies and jobsites are striving to improve sustainability too. The decarbonization of their fleets’ equipment could be a large component of their sustainability efforts.”
He added, “By testing the backhoe during Phase 1 now, John Deere will be positioned to develop it in the future and, consequently, meet customers’ needs, concerning lower daily operating costs and jobsite noise, as well as enhanced machine reliability and a considerable decline in tailpipe emissions.”
Along with testing the E-Power backhoe, John Deere is also preparing to showcase new performance-tiering models of backhoe-loaders at CONEXPO-CON/AGG next year. For example, the 310L EP is transitioning to the rugged 310 G-tier, while the 310SL and 310SL HL are transitioning to the 320 P-tier and the 320 P-tier with a heavy-lift option, respectively. In preparation for these transitions, the 320 P-tier’s engine horsepower is set to increase as well.
While looking ahead to the future, Clowes predicts a backhoe with zero emissions at its point of use will eventually be released. After all, a majority of backhoes are utilized in cities and towns, many of which have committed to becoming carbon neutral in the future, according to Clowes.
Anderson, meanwhile, adds that alternative fuels are at the forefront of product development for virtually every manufacturer at this time. For example, electric power is the most popular manufacturing trend in the construction industry—even more popular than liquid propane, methane and natural gas, according to Anderson. As a result, more equipment and vehicle manufacturers are responding to this trend, as they’re offering more electric vehicle options than ever before.
“Electric vehicle options will continue to expand as battery technology evolves,” he said. “Alternative fuels are impacting operators directly too, as battery technology is going to be the most important factor in the growth of electric equipment and vehicles.”
Two key considerations stand out, in regards to alternative fuels: performance and run time, as batteries must work harder and longer than they ever have, simply put.
“With this in mind, the construction industry will continue to notice more electric vehicle options start popping up in the future, especially as battery technology improves,” Anderson said. “There is no question about it. Construction operators must prepare for a future of electrification, as the current movement will likely become a reality one day—across the construction industry.”