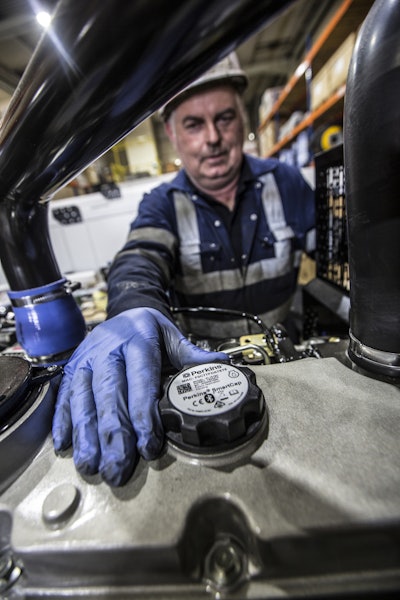
In this day and age, we use our phone for just about everything - it's our alarm clock, our navigator, our personal DJ, shopper, organizer and personal trainer, not to mention a fount of all the world's knowledge. So why wouldn't we use it for engine maintenance?
Fortunately for fleet owners, engine manufacturers have been working hard to make the process of taking care of their products easier through the use of mobile apps coupled with small diagnostic devices that can be connected to any piece of equipment.
The recently introduced Perkins SmartCap and Cummins INLINE Mini are excellent examples of this trend. Both work with mobile apps to support routine maintenance by reminding owners when service is required and then assisting with the task.
"Working together as a low-cost engine connectivity device, the Perkins SmartCap, and intelligent software, the Perkins MyEngine app, help the owner/user implement a regular maintenance program that can provide significant financial benefits from improved efficiency and extended operating cycles," explains Ian Bradford, Perkins parts product manager. "The bottom line is that engine connectivity enables both engine monitoring and service scheduling to maximize engine reliability and minimize unplanned downtime."
Obviously, in the rental business, maximum uptime is everyone's top priority.
"Smart diagnostic tools are critical for not only engines, but the construction rental segment overall," notes K C Hall, project management director - service, at Cummins. "Many customers tend to work in remote locations and may not have quick access to a service provider for assistance. In understanding this crucial need, we’ve developed innovative tools such as Cummins Guidanz and the Cummins INLINE mini."
Smart diagnostics tools promise to help everyone service, maintain or repair engines more efficiently and effectively. Equipment users are almost always on strict project deadlines, so equipment failure can be disastrous to the project and the bottom line. Cummins' Guidanz mobile app and the Cummins INLINE Mini quickly identify fault codes (on Tier 3 and later engines), locate a Cummins service provider and allow the customer to communicate critical information to their service provider.
"Rental houses are able to effectively manage their equipment downtime by understanding the failure root cause in advance and improve uptime by ensuring parts, service bay and technician availability to perform the needed repair," Hall says. "With Guidanz mobile app and INLINE Mini, it's possible to convert an unplanned equipment downtime to a scheduled maintenance job for our rental customers."
Likewise, the Perkins SmartCap gives fleet owners access to critical information including total running hours, current location and upcoming service requirements.
"Intelligent software like the Perkins My Engine app provides automated assistance to help smaller customers with detailed task lists and parts requirements for scheduled engine service," Bradford says. "Even Original Equipment (OE) service dealers can benefit by providing more responsive support based on improved awareness of customer requirements."
The human factor
Sadly, people aren't perfect, and often, neither are their equipment service and maintenance habits. Fortunately, smart diagnostic tools are making it easier.
"People get busy, people forget, people make mistakes and people take shortcuts, none of which helps extend engine life or improve operating efficiency," notes Bradford. "That’s why smart tools are the wave of the future."
He explains that until now, smart diagnostic tools have been primarily focused on the latest generation of electronic engines. But, there are millions of mechanical engines in service too, which is why the Perkins SmartCap was designed to work on both.
"The Perkins SmartCap does not require communication with an Electronic Control Unit (ECU) or even the presence of an ECU," he says. "A user simply replaces the existing oil filler cap with a Perkins SmartCap and instantly gets engine level connectivity on an electronic or mechanical engine. It’s the only engine connectivity device in the world that works on both and it does so without the cost of a monthly data communications subscription."
Hall at Cummins says one obstacle to the adoption of smart engine diagnostic technology is that with traditional failure reporting devices on the equipment dashboard, operators are not always able to understand the issue.
"It's often hard to understand the criticality of the failure and the time it will consume for the operational management, so the lack of information that the operator or foreman can share with the technician is often associated with multiple trips to repair and excessive downtime for our consumers," he says.
Technology offers a solution
Smart engine diagnostic devices can help anyone who owns or operates engine-powered equipment.
"All rental customers using Cummins-powered equipment can take advantage of the capabilities and features of smart diagnostic tools," Hall says.
Cummins' Guidanz Mobile App displays Cummins fault codes and other key engine info so customers can provide this info to their home office or rental house. They're then provided with links to the Cummins service locator and Cummins Care, which in turn sends information to the nearest service provider.
"It improves customer uptime by helping them to make more educated decisions – whether to service now or service later," Hall says. "And it reduces the risk of the technician making multiple trips to find the root cause and fix the issue."
The Cummins INLINE Mini Adapter, a nine-pin connector that plugs directly into the SAE J1939-13 diagnostic connector on equipment and connects via Bluetooth, works in tandem with the Cummins Guidanz mobile app, which is available on both iOS and Android platforms.
For its part, the Perkins SmartCap fits mechanical and electronic Perkins 400 Series to 1200 Series engines displacing from 0.7 to 7.1 liters, Bradford explains, noting, "It’s also economical enough to make sense for someone who owns only one engine."
For a single machine operator, the Perkins SmartCap provides useful reminders for when services are due and helpful aids when performing those services. Fleet owners get that benefit and the added support for an overall engine management system that eliminates the need to store extensive data files on each engine. They also get fully electronic service reminders, a service log and access to constantly updated parts books and operation/maintenance manuals.
Users appreciate simplicity and low cost
Bradford says user response to the Perkins SmartCap has been overwhelmingly positive.
"The feedback we have received says they are impressed with the simplicity of the Perkins SmartCap/Perkins MyEngine system and the fact that it works on such a wide variety of machines," he says. "The app currently supplies information in English, French and German with Spanish scheduled to be added within a month and other languages in the queue."
At $49.99, customers also appreciate the low cost of the Perkins SmartCap and the fact that the Perkins MyEngine app is free to download and use, says Bradford. "Most other connectivity systems require ongoing payments that add up over time, especially if an owner has many machines. The cap, by comparison, has no ongoing connectivity costs," he adds.
"Customers find it very helpful to use Cummins Guidanz to access and share failure information in advance with their maintenance operators or service shops," says Hall. "They believe they can inform service providers much earlier and it will enable technicians to visit equipment located in remote areas, with the necessary parts and tools. They anticipate that this pre-information will significantly reduce their failure diagnosis and equipment downtime."
He continues, "End users consider the use of Cummins Guidanz a game changer, by having the ability to understand better the problem and its criticality. Furthermore, they can make better decisions for their business and improve up time, in addition to sharing this information with the Cummins-certified technician in order to reduce the time to repair."
The bottom line
In the simplest terms, smart diagnostics allow rental companies to quickly assess and schedule service accordingly.
"In the event of a fault error message, rental companies can plug in the Cummins INLINE Mini, pull prioritized fault code data and send the information directly to their Cummins service provider via the Cummins Guidanz mobile app," Hall explains. "At that point, a certified service provider can work with the fleet to determine severity and schedule service accordingly. This maximizes equipment efficiency and uptime."
Rental sites can quickly verify that every unit is leaving their site with no fail codes, which means no issues during the job and rental period. Rental companies can also maximize their operations by obtaining key information from the engine and decide whether the job can be finished and schedule service later, or quickly swap the equipment before the job and customer is affected.
"A huge benefit to smart engine diagnostics is knowing the exact engine operation hours at all times, which means services can be scheduled while the asset is not committed to a project, so it’s never out of action when required by a renter," Bradford says. "Real-time data from the Perkins SmartCap also lets management teams compare engine use across assets, allowing all machines to be utilized at the most competitive rates. Rental companies also could use Perkins SmartCap data to offer preferred rates to renters based on tracking and usage information that quantifies the operational efficiency benefits of the Perkins SmartCap equipped assets."