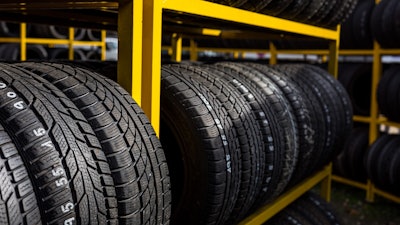
With approximately half of today's construction fleets running on bias-ply tires and the other half shod with radials, it's important to understand the benefits and impact on operating costs of each type. While North American construction fleets lag Europeans in the adoption of radial tires, their market share continues to grow.
"The larger the equipment, the higher the percentage of radials," says Dave Wright, manager - global OTR product support, Goodyear Tire & Rubber Co. "It continues to go toward radials. It's just a matter of how long will it take to completely change over."
The replacement market demonstrates the different adoption rates by size. "For the smaller machines that have a 23.5 R 25 or smaller, the market is about 40 percent radials, but it's climbing," says Tomas Bennett, market segment manager for forest and construction, Michelin North America. "You get into the bigger machines with a 26.5 or a 29.5 and it's about 50 percent. The large mining trucks are 80-percent plus."
This trend is being driven by the advantages of radials in many applications. "While the upfront purchase price of a radial is slightly more than a bias, in the end the total cost of ownership is almost always lower," says Rob Mills, marketing product manager, Bridgestone/Firestone Off Road Tire Co. "Radials offer lower fuel consumption, better traction and flotation and improved cut resistance in the tread area, and run much cooler than bias."
"Radial advantages are pretty much across the board," agrees Wright. Typically they offer longer tread wear and a smoother ride.
These characteristics make them an obvious choice for transport equipment, such as articulated dump trucks and rigid-frame haul trucks. "Transport machines were probably the first to use radials," says Bruce Besancon, key account manager, Earthmover Group/Michelin North America. "In most cases, those were the ones with the highest rate of tire usage. They could factor in the savings they were achieving out of the radials quicker than those on other products."
"Construction trucks operate at high speeds and carry tremendous loads," says Mills. "Radials really show their advantages here. Better traction, less heat and less rolling resistance all lead to better performance, increased productivity and improved operator comfort."
Work tools such as wheel loaders and scrapers are now moving toward radials. "The work tool tires have taken longer to switch over," says Wright. "In Europe, loaders are 100 percent on radials due to longer tread wear and ultimately operator comfort. In North America, the changeover has been much slower, I think due to the fact that the stability is not the same."
Puncture and Cut Resistance
"Radials are about 80 percent more resistant to cuts and penetrations in the tread area," says Mills. This is due to differences in construction between radial and bias-ply tires.
A bias-ply tire is made of layers of rubber-coated, criss-crossed plies of fabric placed at angles of approximately 30 degrees. Nylon is the commonly used fabric. The tire is constructed to form a single working unit.
A radial tire is constructed in two parts. The casing has one layer of rubber-coated steel cables that arc from one bead to the other. Then several rubber-coated steel plies make up steel belts that are placed under the tread to stabilize the crown. These belts resist cuts and punctures.
"You have to cut through a number of steel belts to cut all the way through the tire in the tread area, where you are going through fabric on a bias-ply tire," says Wright.
This often results in less downtime due to punctures. "It's not uncommon to see a reduction in flats by 80 percent," claims Bennett. "If you put a pencil to it and just said you want to reduce your flats 20 percent, it would more than pay for the tire."
When cuts do occur, the radial tires are often more repairable. "If the radial tire is damaged, it only damages a very small portion of the tire," says Besancon. "If a bias-ply tire is cut in the sidewall, it affects 25 to 35 percent of the overall structure of that tire."
"If you make a cut in [a bias-ply tire], it unravels kind of like a ball of yarn," adds Bennett.
But there are applications where bias-ply tires have the advantage. "Bias-ply tires have thicker sidewalls, which can improve sidewall cut resistance," says Mills.
"What happens is a radial tire [sidewall] deflects more so you have a little more opportunity to hit a rock [with the sidewall]," says Wright. "When you cut it, you are ultimately working through one ply of steel. With a bias-ply tire, if it is a large tire, it may have a high number of fabric plies. It is more material for the cut to work through."
Wright says this can make bias-ply tires a better choice for a loader that works in some forms of shot rock, where sidewall punctures are a common occurrence.
Traction
The difference in tire construction also has a major impact on traction. Since the bias-ply tire is constructed as a single working unit, when the sidewalls deflect, the tread squeezes in and distorts. "When the sidewall flexes, the middle of the tread actually lifts up," says Bennett. "So it actually erases itself." The relationship of the sidewall of the tire and the crown of the tire is interdependent.
The construction of the radial tires allows the sidewall and the tread area to work independently of each other. "That allows the tread to sit much flatter on the ground and become a much more evenly distributed contact patch," says Besancon.
"Radial tires have a bigger footprint, stiffer tread and distribute weight in a more uniform manner," says Mills. "This gives a steady and consistent contact patch, which promotes greater traction. This usually results in more even wear and longer tire life."
An example is a loader tire. Wright has observed that a radial loader tire working in the field doesn't spin as much when it is digging. "You can watch the casing wind up a little bit," he says. "Since the tread doesn't spin, it doesn't wear as fast."
Ride Quality
Ride quality varies dramatically between radial and bias-ply tires. Radials provide a smoother ride, while bias-ply tires offer more stability in the sidewall for certain applications.
Stability in the sidewall keeps loaders from rocking back and forth when loads are carried up high. "With wheel loaders, many operators like the stability provided by the bias tire's thicker sidewall and multiple body plies," says Mills. "At first, radials may feel 'soft' to some operators."
Goodyear has introduced radial loader tires with a similar feel to the bias-ply tires. "We have specifically marketed them as high stability," says Wright, "and we made them to have similar characteristics to a bias-ply tire."
But the smoother ride of the radial often translates into increased productivity for many types of equipment. The sidewalls of the radial easily flex to allow greater vertical deflection. This isolates the operator and machine from uneven terrain.
Heat Tolerance
Tires are made of a conglomerate of different materials. In many cases, several types of rubber are vulcanized to produce the desired characteristics. If a tire is heated past this vulcanization temperature, it starts to deteriorate.
"Once you overheat it, the tire does not come back to its vulcanized state. It comes back to a different state with completely different properties," says Besancon. The rubber may get brittle or you may witness other problems such as coking.
Heat buildup can be checked by monitoring your air pressure after operation — the hot temperature pressure. "If that pressure buildup is over 25 percent, there is a large heat source going into that tire," says Besancon. A good rule of thumb is that your air pressure buildup during operation shouldn't exceed 25 percent of the initial cold pressure.
Radial tires dissipate heat better than bias-ply tires, which allows them to travel at higher speeds for greater distance. "Due to a rigid tread, single steel body ply construction and the absence of multiple nylon plies, radials are much more effective at reducing heat," says Mills.
Tire Life-cycle Costs
Calculating the total life-cycle cost of a tire is the only true measure that will enable you to lower operating costs. "One [common mistake] is buying what is cheapest vs. what will give you the lowest economic cost," says Wright. "It is short-term vs. long-term thinking."
A lower-priced bias-ply tire may not offer the same life as a more expensive radial. "It's not uncommon that a radial will outlast a bias-ply tire two times or up to six or seven times, depending upon the application," claims Bennett.
"Another mistake is buying only when you have a problem," says Wright. This results in the purchase of what is available rather than what is most suited for the application.
The best way to determine the most appropriate tire for an application is to keep tire records. "The only way to improve is to know where your base is, then work on doing better next time," says Wright.
"If you start comparing tire bills and really get into the science of this, you will see that it is just as important to choose the right tire as it is to choose the right piece of equipment to go into an application," says Besancon.
It is not just a case of radial vs. bias-ply. Michelin alone makes nine different radial tires that go on the Caterpillar 950 loader, depending upon the application. You need to understand the differences in order to get the greatest return on your investment and not get lulled into the "tire is a tire" mentality.
"Besides the obvious tire-related savings that come with selecting the right tire for the application, there are potential productivity and machine mechanical issues that can cost much more than was saved by buying the cheapest tire," says Mills.