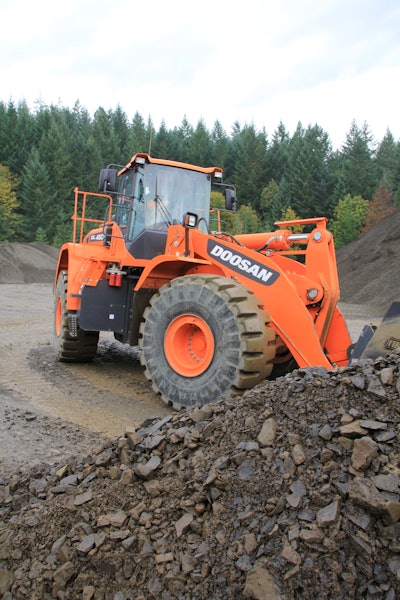
Selecting proper wheel loader tires may make a significant difference between under-performing or excelling on jobsites. If the correct tire is chosen for the application, it can save time and money down the road.
According to Mike Stark, Doosan wheel loader product specialist, a radial tire tends to be more expensive than a bias tire. However, the machine’s total cost of ownership may be lower because the radial provides better traction and flotation, and helps contribute to lower fuel consumption.
“Radial tires have better control, especially at higher speeds, because the tires don’t flex as much,” Stark says. “Also, a lower rolling resistance allows wheel loader operators to turn easier.” The tires also don’t heat up as much when in high-speed applications, extending tire life.
Radial tires typically consist of two parts. The first is the casing, composed of one layer of rubber-coated steel cables that arc from one bead to the other. The second is rubber-coated steel plies — made up of steel belts — which are placed under the tread, helping resist cuts and punctures.
Radial tires are ideal in applications where traction, tread wear and distance are important factors. They are well suited for wheel loaders operated on finished surfaces for loading applications.
Operators looking for tires that do well on gravel, as well as pit and quarry applications where cutting the sidewall is a possibility, should consider bias tires. “Bias tires have thicker sidewalls, which gives them a stable and smooth ride,” Stark says. “The bias tires perform well because they are more repairable and the distances traveled are normally shorter.”
According to Stark, Doosan wheel loaders come with standard bias tires, but many of the loaders are sold with optional radial tires. He says it depends on what application the tires will be operated in most.
Radial Vs Bias Earthmover Tires
In addition to radial and bias tires, there are solid tires, which are normally reserved for scrapyard and industrial applications, and flotation tires, which are wider, but are ideal in soft and muddy ground conditions.
Multiple Tread Patterns
After determining the best tire type for the application, the next step is to select the tread pattern or tire design. According to Stark, wheel loader tire treads should be tapered to allow material to exit the tires. In wet or muddy conditions, the excess buildup can fall out of the tire grooves, giving operators more traction on jobsites.
In common wheel loader applications, an L2 or L3 tread design is recommended. With the L2 tire, maximum traction and cleaning ability in sand and soft conditions is favorable. The L3 offers rock resistance in general loader applications. When looking for tire treads in pit and quarry applications, the bigger the tread number, the better. The L5S or L5 offers deeper tread depth and longer tread life.
Although L4 and L5 tires are more expensive than the lower numbered treads, Stark says the cost of ownership again comes into play. “If the machine is sitting around for a couple of hours each day, the owner might want to look at the up-front cost,” he says. “However, if he’s continually operating the machine, he may want to invest up-front in the right tire to save him money down the road.”
Understand Tire Ratings to Match Off Road Tires to the Application
Maximizing Tire Life
To maximize wheel loader tire life, you must first understand that each jobsite is unique and that some applications may tax the tire more than others.
“A typical tire lasts between 2,000 and 3,500 hours, but it all depends on the application,” Stark says. “You have to consider what applications the operator will be using the machine in to determine if your tire will have longevity.”
For instance, a tire that is used in rock or quarry applications may have a shorter life span than a tire used in sandy, dirt or concrete applications.
The way an operator handles his machine also plays a part in the tire’s longevity, says Stark. For instance, operators who spin the tires going into a pile could produce more tire cuts and also cause the tire to wear faster.
Operators should perform daily maintenance checks, including monitoring air pressure, to maximize tire life. “[Low air pressure] may put more pressure on the outside of the tire, creating problems later on,” Stark points out. “Owners also have to make sure they don’t have too high of air pressure in the tire either. If a tire is under- or over-inflated it may cause the wheel loader to burn more fuel, which isn’t efficient.”
Choosing the proper tire for the application can be confusing. However, with tips from product specialists and information from an independent dealer, maximum tire longevity can be achieved.