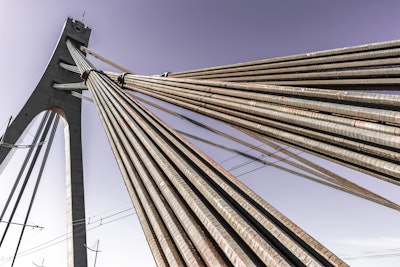
According to the American Road and Transportation Builders Association, there are 171.5 million crossings per day on over 45,000 structurally deficient U.S. bridges—a significant number of which have bridge cable corrosion issues. Bridge cable corrosion can be devastating to the integrity of a bridge over time. It’s imperative that stakeholders perform regular testing and inspection to mitigate disaster.
The American Association of State Highway and Transportation Officials (AASHTO) recommends that a bridge must be inspected every two years. The reason for this is simple: lives are at risk and supply chains need to be maintained. The main cable on suspension rope bridges supports the suspension ropes which in turn support the roadways, which carry thousands and sometimes millions of trucks, busses, motor vehicles and trains each year. The condition of the bridge cables is not always visible and therefore needs to be uncovered through a variety of testing methods.
The History of Bridge Cable Corrosion
Every year, federal and state governments need to spend billions on bridge corrosion issues. From San Francisco’s iconic Golden Gate Bridge, to New York’s Bear Mountain and Mid-Hudson Bridges, corrosion has been a problem on some of the country’s most prominent bridges.
Most recently, New York’s Tappan Zee Bridge was seriously affected by corrosion. Originally built in 1955, the Tappan-Zee bridge had to be replaced by the year 2000 because inspection and testing revealed corrosion and overstressing of the steel structure beyond its useful life after only 45 years. A replacement bridge was finally built and opened in 2017 after the engineer of record determined that the old bridge was unsafe for continued use and that the yearly cost of repairs did not justify continuing the repairs.
The Dangers of Corrosion
Cable corrosion on suspension bridges is dangerous, because corrosion is often not visible. Reduced cable strength as a result of corrosion can lead to bridge failure. Leadership needs to gain an understanding of the bridge’s condition, and they may do it with a rigorous testing and inspection program.
Some ways to address bridge cable corrosion include cable replacement, or a technique known as dehumidification, which helps to arrest corrosion in the main cable anchorages. The waterproof coating and wire wrapping must be periodically inspected to ensure that these components have not been compromised. It is up to the engineer of record to determine how to proceed and fix any problems that may have been uncovered.
How to Determine Condition of Bridge Cables
Corrosion of the main cable, over years of service, is not readily visible because the cable is wrapped with wire and waterproof coatings. Determining the extent of corrosion is accomplished by removing the outer wire and wrapping at predetermined areas of the cable and driving wooden wedges to separate the wires in the main cable.
The condition of the main cable is evaluated by selecting main cable wires with the greatest degree of visible corrosion. These wires are extracted from the main cable and replaced with new wires joined with press-on ferrules and turnbuckle ferrules to maintain the wire tension. The extracted wires are initially categorized for the extent of visible corrosion and any evidence of cracks.
Testing Process for Bridge Cables
The sampled wires, nine to twelve feet long, are chemically analyzed, tensile tested, and the fractured surfaces are examined under a scanning electronic microscope for any evidence of pre-existing cracks. A dye penetrant examination can be conducted prior to tensile testing to determine if any pre-existing cracks are present in the sampled wires before testing.
The zinc coating on the wires provides passive corrosion resistance to the steel wires. Over time the zinc is dissipated and must be tested to determine its continued effectiveness. There are two tests used: one, a weight of coating test, which gives the average weight (thickness) of zinc left. A second test is the Preece test which determines the uniformity of the zinc coating and shows whether any holidays (bare spots) are present.
The results of these tests are then submitted to the engineer of record to determine the life expectancy of the subject main bridge cable based on the original design specifications.
There is an effort underway to design bridges for inspectability so that the inspection of all of the bridge components are readily visible. If this is accomplished in the design phase, the costs of inspection and maintenance over the life of the bridge would be greatly reduced.
Conclusion
According to the American Society of Civil Engineers, there are more than 617,000 bridges across the United States, 42% of which are at least 50 years old and 7.5% of which are considered structurally deficient—meaning they are in “poor” condition.
As leadership learns more about the state of their bridge infrastructure—from the bridge cables to the health of the overall structure—they may take the necessary steps toward repairing damage and increasing safety for people and communities. The new infrastructure bill will be a positive step toward providing the funding for repairing the deficient bridges.
Nagesh Goel, President, AEIS and Herbert Goldenberg, Technical Advisor, AEIS, contributed to this article