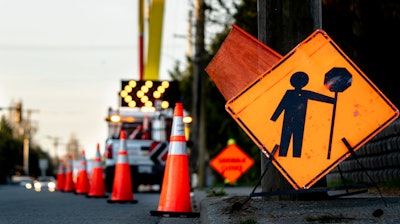
Working in road construction is a dangerous business. According to the Federal Highway Administration, more than 20,000 workers are injured each year in road construction work zones, and 35% of those are injuries due to contact with objects or equipment. With an influx of new and less experienced workers in road construction, proper training and safety guidance is imperative to help reduce injuries on the job. According to the U.S. Bureau of Labor and Statistics, 34.9% of new, untrained workers in the construction industry are injured during their first year on the job.
While workers may be more aware of visible safety protocols like reflective clothing and traffic routing or safety practices for operating equipment, it’s often the little things that cause accidents—and that adds up to injured workers, lost time, and higher insurance premiums for construction companies.
Hand placement of shims and use of pry bars can lead to pinched or crushed hands or fingers. Caught-in or caught-between hazards are one of the leading causes of death and injury in the construction industry according to OSHA.RimRiser
Crushing injuries are one of U.S. Occupational Safety and Health Administration’s (OSHA) fatal four incidents, and “caught-in” or “caught-between” hazards are one of the leading causes of death and injury in the construction industry. OSHA defines these as injuries resulting from a person being squeezed, caught, crushed, pinched, or compressed between two or more objects or between parts of an object. That’s why OSHA requires the use of “special hand tools for placing and removing material without the operator placing a hand in the danger zone.”
Shim material is often left up to the installer’s discretion. In a pinch, improvised materials are used to approximate the correct elevation.RimRiser
More Information
Download a FREE whitepaper on the 2022 State of the Road Building Industry.
Manhole-related Injuries Are Serious Business
With high risk comes high insurance premiums for construction management firms and municipalities. Employers in the construction industry already pay more than twice the average worker’s compensation costs as compared to employers in all other industries. If we don’t get newer processes, specifications, and safety practices in place, the situation is only going to get worse.
Manholes and other utility covers are commonly situated as close together as 20 manholes in a single city center block or every 200-300 ft. in a suburban area. As roads are re-paved and repaired—and as more utilities and services are built or moved underground to protect them from erratic weather patterns or simply to remove utilities from view to support the beautification of a city for its residents —more manhole-related injuries are inevitable. Road crews must be made aware of the common dangers of working around underground utilities and systems and practices need to be upgraded to protect everyone involved.
4 Pieces of Advice
Many of these dangers are entirely avoidable, particularly when proper guidelines and systems are in place to prevent them.
- Make manhole installation safety a conscious priority. Too often manhole rehab is a last resort, and it’s often last on the list of priorities for asphalt layers. This pushes workers to move quickly to level them as paving crews wait. When you have inexperienced crews on a job that’s a low priority or afterthought, with minimal supervision and outdated methods of installation, you have a recipe for injuries. It’s time to raise the profile of this work while leveling the profile of your utility covers.
- Ensure crews are aware of common dangers on the job. OSHA’s simple guideline of never putting hands or limbs between objects is a life-and-limb-saving recommendation. This is true whether you’re talking about lifting a cast iron manhole ring and cover or working with overhead objects like heavy concrete utility tops and grates. Using more modern methods of leveling can significantly reduce the number of workers required on-site and the time required to level these heavy objects, while also reducing injuries. And there’s no substitute for making sure every worker is aware of these hazards. The American Road and Transportation Business Alliance (ARTBA) has published guidelines and tools that can be posted at job sites discussing the hazards of “crushed by” and “pinned between” hazards.
- Employ training and safety procedures. When crews have inexperienced workers or a lack of standardized systems in place, everyone can be exposed to a higher risk of injury on the job. Procedures specific to underground fixtures must not be overlooked – whether for heavy precast concrete tops and lids or cast-iron manhole rings. ARTBA and the Transportation Development Foundation have published a Safety Center website where you can access training programs, events, tools, and other safety resources for road construction crews.
- Replace “we’ve always done it this way” with specs and engineered solutions. Upgrading engineering specifications to incorporate the latest, safest and simplest tools for utility cover leveling creates safer worksites (and smoother, longer-lasting road surfaces). Road crews can benefit from having these specs and equipment to ensure they know exactly what is expected for the safe and accurate installation of these awkward and heavy objects.
While specs can indicate the surface level of the road, there is no random shim that can precisely ensure that manhole and other utility covers are perfectly flush with the road surface. That puts workers’ hands and fingers at risk longer, trying to achieve a close-as-possible level. Contrast this with newer, engineered solutions like bolt- and screw-adjusted manhole rings and precast concrete tops that provide an extremely precise degree of accuracy while also eliminating the need for hands and arms to be placing shims under heavy objects. In these solutions, cast iron rings and precast tops can be premade with specially engineered screws that can be turned from above with a single ratchet or screw gun. This allows the tops to be quickly leveled exactly to specification by one or two workers without the use of machinery, prybars, or shims. In addition, the screws are uniform in size and easy to carry in a pocket, so road crews don’t need to carry around buckets of different-sized shims.
More Information
Listen to these podcast episodes by ForConstructionPros.com on safety and road construction.
- Digging Deeper: Improving Work Zone Safety Through Innovation - PSS International is delivering products to the industry that help to ensure every person arrives home safely at the end of the day.
- Digging Deeper: PPE Best Practices with Safety Expert John Meola - John Meola, safety manager, Timmons Group, discusses PPE best practices that can help to enhance safety on your construction sites.
- Digging Deeper: Asphalt Companies Strive to Improve Work Zone Safety - Asphalt Materials Inc. has created a culture of safety at their company to achieve their goal of getting every worker get home to their families each night.
- Backbone of America: A Fresh Perspective From a Laborer in the Roadbuilding Industry - Tyson Miller, a union laborer provides a positive perspective about training, the jobsite and words of advice for newcomers to the industry.
Find more articles and insight on construction safety at ForConstructionPros.com.
Typical manhole casting being adjusted to final grade with RimRiser jack screws. No pry bars or shims required.RimRiser
Reducing the number of injuries not only keeps people on the job, but it also pays off in lower insurance premiums. Insurance providers see a direct correlation between the products used for things like leveling manholes and other utility covers and reducing costs.
“When the product specs are in place and road construction crews implement safer practices, it improves efficiency, lowers overall project costs, and reduces workers' compensation injuries,” explains Justin Cumnock of Anchor Insurance and Surety Inc. “That can translate into a lower workers compensation Experience Modification Rate (EMR) factor and the potential to reduce insurance premiums down the road.”
About the author
Aaron Barr is the founder and CEO of RimRiser with more than 30 years working in the field as a contractor, developer, and craftsman.