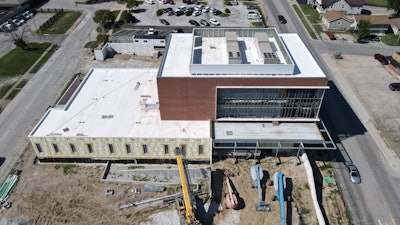
There is a vanishing small number of very large contractors, who pursue the most impressive and monumental infrastructure and industrial projects, and rely on high-flying enterprise software tools from companies like Oracle, SAP, Microsoft Dynamics or Infor Global Solutions. There are a lot more contractors like Columbia, Mo.-based Little Dixie Construction that build the infrastructure of American communities, and they rely on a cloud-based middle market construction technology stack that has come to market over the last decade.
This is delivering to companies like Little Dixie capabilities that had only been affordable to the largest global contractors so they can improve the owner experience, project quality and drive down cost.
With 35 employees working from an advanced headquarters facility they built for themselves in 2019, replete with light harvesting and Lutron lighting systems, Little Dixie may at a given time have crews on sites for convenience stores, multi-family, Greek housing, and government projects.
The company is not young—it was founded in 1964—but technology is enabling management to actively evolve Little Dixie, making them more competitive and helping them diversify from general contracting services and into design/build and more recently construction management at risk.
“We are making investments that are really aimed at preventing the loser projects from happening,” Little Dixie Controller Kale Dempsey said. “I think we have seen that coming to fruition. All the technology we purchase, we evaluate from the standpoint of whether the juice is worth the squeeze. And we hope we are, using these technologies, giving our project owners a better price and a more accurate budget. And by getting more accurate budgets and competitive prices, we are working with more customers that would otherwise hire someone less qualified.”
Plaza Tire location under construction by Little Dixie Construction.Little Dixie Construction
Innovating in the field with EquipmentShare T3
A middle-market business like Little Dixie Construction has to think on its feet when the ground shifts under them—as it has been with recent supply chain constraints and disruptions which indirectly left Little Dixie without a job site camera on a number of projects.
“We were unable to get transformers oftentimes until the project is substantially complete,” Dempsey said. “Not having the right transformer means we don’t have power—not even temporary power—for months. So we built a solar camera using Ecoflow technology for the batteries on it—and that is something we did just the other day.”
Little Dixie also leverages a broad spectrum of technology for construction equipment fleet management, including EquipmentShare’s T3 operations application. Launched in 2021, T3 is billed as an operating system for construction, and expands EquipmentShare’s remit beyond management of rental and owned equipment to broader management of assets, people and materials in a construction setting. The application ingests equipment telematics data, data from its own timecard application, mobile expense capture and inventory modules. Apps in the T3 suite include:
- Fleet—OEM-agnostic telematics
- Time Tracking—Schedule management, labor timecard capture, work order management and more
- E-Logs—Electronic Logging Device compliance with digital reporting
- Analytics—Customizable reports on utilization, job cost and more
- Work Orders—For equipment maintenance
- CRM—Track vendors and customers
Learn More in Our IronPros EquipmentShare T3 Product Deep Dive
“We have our own fleet of skid steers, lifts, and on bigger jobs we have a telehandler on site, scissor lifts, generators, trailers—we do a bit of our own concrete so we have some excavators,” Dempsey said. “We have an abnormally high amount of equipment for a contractor of our size because we dabble in a lot of different areas and find it necessary.”
In his role as controller, Dempsey relies on an export from T3 to evaluate equipment utilization on a monthly basis, with this utilization then invoiced to the project in Trimble Viewpoint’s Spectrum product which is now part of the Trimble Construction One application suite. He also democratizes T3 data by making it available to others internally.
“We use EquipmentShare asset tracking to go back and look at usage patterns,” Dempsey said. “I give supers access to their own vehicles and projects, just so they can see how much they are using. We want them to see how long they spent on tasks or jobs, and they can do this based on their vehicle movements.”
T3 is a rapidly developing product, and Dempsey sees potential for where EquipmentShare’s research and development efforts are headed.
“There is room for growth there,” Dempsey said. “I am excited for some of the things T3 has on the horizon. We are very excited about a product they are working on called Rapid Rent. They leave equipment on a job site and all of our subs have their own account, and we have an account, and you put your code into their keypad and their system auto-bills whoever is using the equipment. Right now, Rapid Rent uses EquipmentShare’s equipment but in the future, it could use our equipment. So, if a subcontractor needs to use our telehandler for a couple days to stock drywall, they can access it with the keypad and then EquipmentShare sends them a bill and reimburses us as the asset owners. They are beta testing this with their own equipment. The next phase would be using the system on our equipment on a job site—renting our equipment to our subcontractors to help our equipment pay for itself.”
Construction ERP in transition
EquipmentShare T3 integrates with Little Dixie’s instance of Viewpoint Spectrum—which Little Dixie selected shortly after the 2017 acquisition of Dexter + Chaney by Viewpoint and rebadging as Spectrum but before the 2018 Trimble acquisition of Viewpoint. The company had been running on QBCI’s StarProject and Star Builder products, which were going out of support. The vendor was only making annual tax updates to these on-premise applications that had no mobile accessibility or interface.
“Little Dixie bought Viewpoint Spectrum it in December of 2017, and I was hired in January of 2018,” Dempsey said. “I was hired to get the back end of Procore up and running and roll out Spectrum. Before I had the first meeting with Spectrum, they had sold to Trimble. What this did was it showed us that what we had bought, Spectrum, was valuable or at least contained valuable aspects. I see the writing on the wall that eventually Viewpoint and Spectrum will be part of one Trimble main product, but I see Trimble’s technology as a definite advantage moving forward.”
Little Dixie’s instance of Viewpoint Spectrum integrates with Procore, which it had previously adopted as its project management platform. The integration did not come all at once, but rather started with the cost code and cost type fields. Later, vendors, jobs, budgets, change orders and job costs became part of either unidirectional or bidirectional integrations.
“Jobs are shared in the integration, vendors, subcontracts, change orders,” Dempsey said, suggesting they may be considered power users of Procore not only on the basis of their ERP integration but the breadth of their Procore estate. “We have gotten remarks from Procore that we use an abnormally high number of their features.”
Apart from the Spectrum integration, Little Dixie uses Procore’s daily log, photos tool, and the bidding tool—has automated the bid letting process, enabling Little Dixie to let subcontractor bids at scale.
“We just sent out one bid request out to 1,100 contractors,” Dempsey said. “It is letting us get more numbers, so we can get the best numbers available.”
Little Dixie also makes heavy use of Procore’s Documents tool, along with Procore odrive, which the contractor uses as a replacement for a beta product Procore phased out.
“We used a product that Procore was beta testing and then sunsetted—Procore Drive—that made Procore operate from a folder in Microsoft Office,” Dempsey said. “It went from something we were trying to something we could not live without. The replacement, odrive, helps us file things quickly and get things to the right place.”
Learn More With the IronPros Procore Product Deep Dive
Software for Construction Management at Risk
Adopting Trimble Viewpoint Spectrum has given Little Dixie a platform for construction management at risk.
“In the past three years, right when COVID was getting ready to hit, we started getting into construction management at risk (CMAR),” Dempsey said. “We had been a general before that. CMAR has been a trend locally here in Central Missouri and probably nationally. In Missouri and Central Missouri, customers are using this as a way to select the most qualified contractor and at the same time have control over their costs while eliminating risk associated with hiring a general contractor.”
Read the IronPros Product Deep Dive on Trimble Viewpoint/Trimble Construction One
The requirement to deliver a project within a maximum allowable price often requires contractors to refine their project accounting methods before adopting CMAR.
“I don’t know it required us to make changes in those things—it was probably the reverse,” Dempsey said. “We’d made some changes years ago that made that switch rather seamless. We had changed our accounting software and added Procore … so the changes we made after moving into CMAR are much smaller than that. We had also put laptops in more supers’ hands and mobile TV conference rooms in the job trailers.”
Between Spectrum and Procore, Dempsey said the company feels well-equipped for CMAR transparency requirements to document and share project cost, with Spectrum’s vast library of standard reports and the open nature of the Procore platform.
“Procore is making projects much more transparent to owners,” Dempsey said. “It used to be pictures were saved on our server, but now we are able to get customers access to our Procore so they can see photos and daily logs. We have had jobsite cameras for quite some time, and have recently invested in TrueLook cameras—and will be buying more at the end of the year. We are now able to give customers time lapse project videos, which our customers can then access right in Procore thanks to the TrueLook integration.”
This footage can also be used when evaluating vendor pay applications because Little Dixie personnel can go back and view the first day of the month.
“We use these cameras three ways,” Dempsey said. “We use them for marketing to let people see what is happening. We posted our first timelapse video of a demolition of a project and it was very well-trafficked. We use them for safety to be able to see who is on site, what they are doing and to document safety hazards that need to be remediated. But just confirming that our subcontractors have the required people on site is important Manpower is the number one issue we and our subcontractors face--making sure the manpower is there as promised. Otherwise, they may pull people off job site to support other projects, or not bringing the full complement. And finally, we use them to support the project management function to determine what progress has been completed.”
Expanded Phi Kappa Psi residential structure at the University of Missouri in Columbia, Mo.Little Dixie Construction
Tracking people a challenge
While Little Dixie relies on T3 for equipment tracking, they are yet to standardize on a timeclock application for their employees.
“Checking in and out is hard for us,” Dempsey said. “We were using EquipmentShare for e-logs and time keeping, and we looked at some products with geofences. But the problem we had with those is that if you leave the job site, you are automatically clocked out. It could be that worker is going to Home Depot or an architect’s meeting. We don’t want to make them clock out under those circumstances. We are pushing for some type of push notification where a worker gets a pop up that says ‘you left a job site, do you want to clock out?’ We are not seeing that yet at an affordable price.”
One more reason Little Dixie will be looking for a time clock for a while is the dynamic size of a crew on site.
“A lot of software is based on crews,” Dempsey said. “Sometimes our crew is one, sometimes crew is one in the morning and in the afternoon there will be four to five and a super on site.”
Even for prevailing wage projects with their heavy documentation requirements, time sheets at Little Dixie are currently paper-based and manually entered into Spectrum.