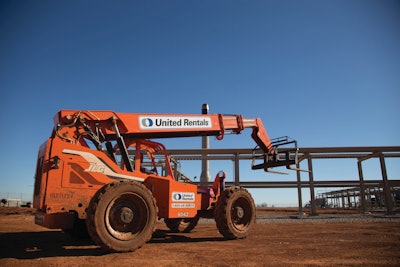
Forklifts are an important piece of equipment for construction contractors. They make it easy to load, unload, lift and transport materials on a construction jobsite.
The starting point in selecting the right forklift for a jobsite is considering forklift capacity, dimension and functional capabilities.
The rated capacity, or load capacity, of a forklift details the maximum weight it can safely lift. Forklifts have a wide range of load capacities, from 3,000 lbs. on the low end to 70,000+ lbs. for a high capacity diesel forklift on the high end.
Looking at equipment dimension, there is no point in buying or renting a forklift that can carry the loads needed to lift if it will not fit the area where it needs to go. Consider the length, width and height (especially the collapsed height) of a forklift with respect to access points such as low-hanging beams and branches; the height of a ceiling if the equipment is operating in a structure and the equipment’s storage space.
Also consider how much space is needed to maneuver when lifting and transporting loads. Longer forklifts will have a larger turning radius. Standard forklifts range in width from about 3 ft. to 7 ft. and in length from about 8 ft. to 10 ft. The largest forklifts can be 10 ft. or more long and 10 ft. or more wide.
Here are a few forklift options with different functional capabilities that contractors can consider for their worksites.
- Counterbalance forklifts are excellent for moving building materials on a jobsite and loading and unloading construction supplies. They have a heavy counterweight at the back of the machine that offsets the weight of the load in the front, which allows them to lift heavier loads. Three-wheel counterbalance forklifts are particularly useful for maneuvering in tight spaces.
- Rough terrain forklifts are designed to handle uneven surfaces—hills, soft ground, mud and rocks. There are several types of rough terrain forklifts. Variable reach rough terrain forklifts have a cab for the operator and a telescopic boom with overlapping sections, which allows the operator to place items directly in front of and above the forklift.
- Telehandlers, also known as telescopic forklifts, have features of a crane and a forklift. An angled boom enables it to access hard-to-reach areas. Telescopic forklift sizes vary. A compact telescopic forklift might hoist 5,500 lbs. up to 19 ft. high. The heaviest-duty telescopic forklift might hoist 10,000 to 12,000 lbs. up to 56 ft. high.
In addition to equipment type, there are a few other important elements that contractors need to factor into forklift operations. These include:
When choosing a forklift, contractors should consult with an expert, such as equipment rental providers, regarding the specific worksite circumstances, and the applicable rules and regulations related to the jobsite.United Rentals
Forklift Maintenance
A forklift in good working order is crucial to a productive worksite. Forklift maintenance matters for renters as well as owners. Most equipment rental companies require the customer to perform regular maintenance and will charge for any damage caused by neglect.
Forklift upkeep is mandated by federal rules. The Occupational Safety and Health Administration (OSHA) requires daily forklift inspections to look for “any condition adversely affecting the safety of the vehicle.” OSHA forklift maintenance guidance is limited to general advice that applies to all industrial trucks.
To catch problems that may pose safety issues or cause the machine to break down, the operator should perform a visual inspection of the forklift before every shift. If an inspection reveals a problem or potential problem, the operator should alert their manager. If an issue poses a safety hazard, the machine should be taken out of service. Operating a machine that is not in safe operating condition may lead to an OSHA fine.
The best forklift for the job comes down to a variety of factors, including capacity, dimension and functional capabilities.United Rentals
Forklift Safety
Forklift safety training is essential to learning how to operate a forklift safely and avoid accidents. Training ensures that operators can steer and maneuver safely, understand load capacity, load composition and the limitations of the machine, and know how to properly secure loads.
Per OSHA forklift regulations, no one should operate a forklift unless they are properly trained and certified to do so. Companies should verify that all operators are up to date on their certifications.
Holding regular toolbox talks is a smart way to remind operators of basic safety precautions. They provide a good opportunity to identify any forklift hazards specific to the worksite and also remind employees who might be on foot in the materials handling area how to stay safe around a moving forklift.
Consider the length, width and height (especially the collapsed height) of a forklift with respect to access points such as low-hanging beams and branches; the height of a ceiling if the equipment is operating in a structure and the equipment’s storage space.United Rentals
Equipment Access
The use of rental forklifts by operators who are not properly trained or certified poses significant safety issues. Equipment access control in the form of a keypad ignition lock can increase jobsite and worker safety and also help owners and contractors boost productivity and reduce costs.
Access control keypads let companies limit who can access the equipment and track who uses it and when. Contractors can set up access management on an online system and assign PINs to specific individuals or groups such as specific crafts or subcontractors. They can also provide access using RFID-enabled ID cards.
With access control system in place, the operator enters the PIN or swipes an ID card, unlocking the keypad ignition lock to start the equipment. If a contractor does not need a keypad ignition system for a particular machine or project, the rental equipment provider can easily disable the feature.
Consider how much space is needed to maneuver when lifting and transporting loads. Longer forklifts will have a larger turning radius.United Rentals
Safety and Productivity on the Jobsite
Forklifts can be one of the most useful pieces of equipment on a worksite. The best forklift for the job comes down to a variety of factors, including capacity, dimension and functional capabilities. Jobsite safety and productivity also require careful equipment maintenance, proper worker training and effective machine access. When choosing a forklift, contractors should consult with an expert, such as equipment rental providers, regarding the specific worksite circumstances, and the applicable rules and regulations related to the jobsite.