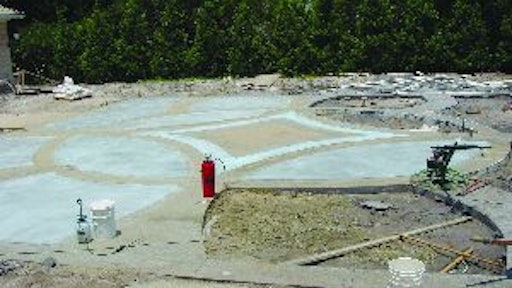
Last summer, Carolina Bomanite Corp. out of Charlotte, N.C., battled hot weather and a complex layout and forming pattern in a private residence driveway project in Wilmington, N.C. Using Lithocrete, an architectural concrete paving system that uses integrally colored concrete and surface-seeded glass, ceramic, and other materials embedded in the concrete, the company succeeded in supplying its client with exactly what they were looking for.
Mike Bernath is president of Carolina Bomanite. He's been in business since 1974 performing decorative and architectural concrete jobs. He's a Bomanite licensee and last year became licensed to install Lithocrete. Carolina Bomanite employs 17 people and takes on commercial and residential jobs in the Carolinas. Most of Carolina Bomanite's residential jobs are upscale projects, such as this 4,100-sq.-ft. Wilmington driveway project. This particular project was performed by a six-man crew over the course of two weeks in 100 degree days. The biggest challenge on this project, aside from keeping hydrated in the heat, was the intricate forming required on the 2,500-sq.-ft. courtyard leading up to the home and garages.
Forming the project
The driveway's square footage totaled 4,100 sq. ft., with a two-color, complex 50-ft. by 50-ft. courtyard near the garage and home area. Bernath received the architect's drawing with his radius points, from which the Carolina Bomanite crew pulled all the curves to do the design.
First Bernath's crew focused on the 50-ft. by 50-ft. courtyard, the key to the whole project. They used a builder's level to shoot grades and lay out the perimeter of the 2,500-sq.-ft. box. After the courtyard box was set, the crew laid out the garage approaches, and then it was on to the courtyard interior design. "Once we had the box laid out at the proper grade, we were able to lay out our curvilinear design because the radius points were taken off the edge of our box," Bernath explains. "For example, you take a point on the box and it's as if you have a giant compass - you stick it at a point and scribe your various lines to set your curvilinear forms."
Bernath's crew used Azek lumber to form the curves in the design. The correct shade of integrally colored concrete was poured in the box, and from there the job became a process of forming out the pattern within the courtyard. With a Lithocrete project, the surface is seeded with the appropriate aggregate right after the pour, leveled out and worked into the concrete. The forming and pouring that happened in the courtyard took approximately eight days with 10 visits from the ready mix supplier.
Bernath's team cut 3/16-in. control joints in the slabs the day following each pour in order to relieve stress within 24 hours. In addition, the separate pours are held together with steel Diamond Dowels from PNA Construction Technologies to offer strength to the driveway. "All of our Lithocrete concrete is reinforced with rebar and all dowelled into the adjacent pour so when a car travels over it your slabs hold together," Bernath says.
After the courtyard was formed and poured, Bernath's crew cleaned and sealed the area with the Lithoseal penetrating sealer. From there the rest of the driveway was formed, poured, cleaned and sealed.
Conclusion
"It was challenging to implement this design in concrete," Bernath says. "It would have been hard to do even if it wasn't Lithocrete, but the fact that we were able to utilize Lithocrete and give the customer the colors they wanted and implement the architect's design was a source of satisfaction for our company. We like to do challenging projects, and a lot of times architects design things but they have trouble implementing them so this project was a way for the architect to get his job done and make his client happy. We were glad to be a part of it."
Bernath emphasizes that on complicated projects such as this one, it's important to develop a good line of communication with the architect, analyze the job you need to do, and try to anticipate the problems and difficulties in doing the project before you start pouring concrete.
"For example, on this project, because of the shape of the design, there are certain stress points in the concrete. We submitted a control joint pattern to the architect and said 'this is where you need to put saw cuts'," Bernath explains. "If you tell the architect structurally what you need to do and submit it to him or her and explain it to them, they're going to go with it because they'll understand it's the wise thing to do."