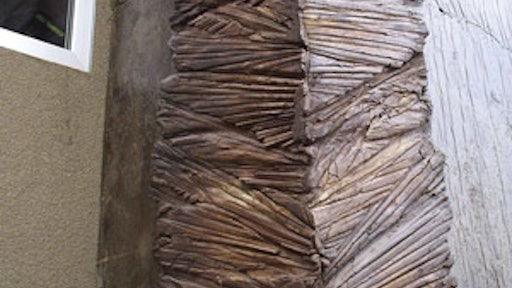
John Lamos of Studio Replica, Inc. contributed to the completion of a 36-ft.-tall residential fireplace in Sausalito, Calif. Lamos' role in the project was to add a decorative element to the exterior fireplace surround. He estimates the entire process for his part of the project - fabrication, curing and installation - took a couple of months.
Lamos says the key architectural element of the fireplace is that it is comprised of modular components, or tiles. He created separate pieces which interlocked to look like one whole piece. To add the decorative pieces to the fireplace, Lamos screwed the tiles into the framing of the fireplace. "It's a specialty item that can be installed by any contractor," Lamos explains.
Lamos pre-cast the entire unit in his studio. In fact, the actual installation of the tiles was the only part done outside of the studio. The flat panels used in the center of the fireplace are individual tiles 41/2 ft. wide by 8 to 10 ft. high and ¾ in. thick. The corner panels are 11/2 in. thick and cast into 20- to 24-in. right angle legs. He used his own mold to create the "Rough Grass" decorative element on the corner panels.
His use of molds instead of stamps is one way Lamos believes he sets himself apart from other decorative contractors in his market. He contrives the shape of the mold based on the project, but the texture can be anything. He works with molds taken from the actual source because of the detail they create. When it came to staining, Lamos used his own proprietary technique - a combination of integral color and topical stain and his own method of applying that stain - to create the effect the client was looking for. For reinforcement, Lamos used an acrylic-modified fiber reinforced product that he gets custom cut from a private, East Coast company.
The fireplace was a unique piece where the client basically allowed Lamos free reign when it came to the design for the face of the wall. But he didn't just keep the project to himself. Lamos prefers to work with a system where the client either comes into his studio or digital images are sent between the client and Lamos to ensure the piece suits the client's desires.
Aside from using molds and his own technique for staining, Lamos also used a proprietary mix of industry standard materials for his cemetitious blend that he says makes incredibly strong material. "It's not your grandfather's concrete," he says. And to create ¾-in.-thick, 4-ft. by 10-ft. panels with no cracks, like he did for this project, is no easy feat.
Do you have a project you would like Concrete Contractor to consider for "On the Job"? E-mail your idea to Kim Johnston at [email protected].