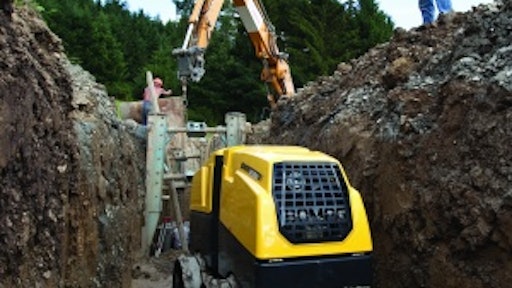
When a project calls for compacting material in a trench, it's important to make sure you use the appropriate compactor for the conditions.
"Like any compaction job, the challenge starts with matching the right equipment with the material and size of the job," says Fred Paul, sales engineering manager, Wacker Neuson. "Trench compaction also offers an additional challenge of [ensuring] operator safety. The contractor needs to pay special attention to the width and depth of trench to determine if shoring is required."
"With shoring, a contractor can use any type of compaction available, since it is a safe environment for the operator," says Scott Bailey, North American sales manager, Weber Machine, Inc. But without shoring, the options become more limited.
Know your soil
According to Guy Boor, engineering product manager for compaction, Stone Construction Equipment, it's important for a contractor to have at least some understanding of the materials, moisture content and soil mechanics of the area to be compacted. "He will then understand the relationships involved to achieve compaction and can make an informed decision."
In the case of cohesive materials (e.g., clay or silt), rammers and sheepsfoot (padfoot) trench rollers are more effective due to their lower frequencies and high amplitudes. For granular materials (e.g., sand or gravel), vibratory plates and smooth drum rollers are the better choice due to their higher frequencies and lower amplitudes.
"If a contractor is compacting 'crush,' then the best option would be a vibratory plate compactor designed for the amount of material to be compacted," Bailey states. "A vibratory plate compacts mixed aggregate better than a trench roller due to its faster travel speed and larger surface area."
"The vibration action reduces frictional forces at the contact surfaces, allowing the particles to fall freely under their own weight," Paul adds. "Cohesive soils, made of silts and clays, are best compacted by the impact force of a rammer or sheepsfoot roller."
In most cases, notes Boor, contractors are compacting native material, which is usually made up primarily of clay. "Trench rollers work the best because of the drive wheels and the vibration," he says. "In clay material, a plate compactor will tend to bury itself."
The exception would be a boom-mounted plate attachment. "The boom-mounted option works because the operator is performing spot compaction and can pick the plate off the material and move it to another location," Bailey points out.
Match width for width
The dimensions of the work area will influence both the type and features of the compactor required.
"The width of the machine as compared to the trench is an obvious starting point," says Paul. For very narrow trenches, rammers (tampers) are the most common choice. "Rammers are ideal for utility and cable trenches as narrow as 4 in."
Several different foot sizes -- from as little as 4 in. to 13 in. or more -- are available to accommodate varying trench widths.
As the work area expands in size, however, plate compactors and trench rollers tend to be more productive. Walk-behind plate compactors come in working widths up to around 50 in., and are available in forward (single direction) or reversible (dual direction) configurations.
"The advantage of using a reversible plate in the trench is that it eliminates the need to actually turn the machine around. Simply changing the direction of the unit will make quick and easy work of trench compaction," Paul asserts. Many reversibles also come with extension plates to more easily match trench width.
Certain trench roller models can also be adjusted to accommodate narrower trenches. "BOMAG trench rollers offer two different working widths [in one machine] to be flexible for different trench width applications," says Albertus Krings, product manager. "By taking the drum extensions off, the working width can be changed from 34 to 24 in. in just minutes."
Ensure safety
As their name implies, trench rollers are specifically designed to operate in the narrow confines of trenching applications. Wacker Neuson's trench roller, for example, is designed so that the body of the machine doesn't protrude outside the width of the drums. This makes the machine easier to maneuver in tight spots, and less likely to bump against the sides of the trench.
But trench rollers are also suited to deeper trenches where shoring may or may not be in place. Take Stone's Bulldog trench rollers. In addition to 34- or 24-in. drums, vibration in forward and reverse, high compaction force and dual-speed control, they incorporate Snap-Tek technology, a "plug-and-play" control that enables a manual model to be easily converted to radio-frequency remote control.
"With it, operators can stay out of the trench and still operate the machine," Boor indicates. "Our machine also uses anti-backup logic that will prevent the machine from backing into an object, structure or person."
Remote operation is highly desirable for compaction in trenches where a cave-in risk exists, or where exhaust fumes may be a concern. "By using the remote-controlled products, the operator can keep a safe distance from the machine and out of the trench -- avoiding the inherent dangers of being in the trench — and away from the fumes and noise of the machine," Paul points out.
For added protection, BOMAG also incorporates a "safety zone" around its remote-controlled trench roller. "The machine stops moving toward the operator while in a range of 3 ft. all around the machine," says Krings.
In addition to a radio-controlled safety zone, Weber Machine includes "dead man" bars on its remote-controlled models. "If for some reason the operator is not paying attention while running the unit, a safety bar mounted in front and back will stop the machine immediately if it comes in contact with anything in front or behind the machine," says Bailey.
Remote control isn't exclusive to trench rollers, however. Several compaction equipment suppliers now offer remotes for specific plate compactor models.
BOMAG's BPH plate compactor offers a choice of remote options. "[Our] remote-controlled reversible plate offers both cable or radio remote control for a very safe operation by allowing the operator to remain positioned out of the trench," Krings notes.
Wacker Neuson uses joystick-controlled, infrared remote control for both its trench roller and plate compactor models. The remote uses a line-of-site signal and will stop the machine automatically should the operator lose visual contact.
The remote also features a standby safe mode. "A sensor will immediately switch the plate to idle and stops all movement as soon as the operator is standing within 6 ft. of the unit, or lets go of the joystick," Paul explains. "While this feature improves safety, by switching the unit into idle, it also reduces exhaust fumes, saves fuel and keeps noise levels down."
Achieve density specs
Of course, a compactor is only effective if it can meet the required specifications of the project.
"The common specifications include lift, soil depth/layers and the number of passes made with the machine to achieve compaction," says Paul. "The machine selected should have enough power to compact to the depth required. If the machine does not have enough power, the proper density will not be reached. If it has too much, over compaction can occur. This is the result of excessive passes or too much power on too thin a soil layer."
To minimize the risk of over- or under-compaction, some manufacturers are now incorporating technology into their plates to monitor compaction effectiveness. For example, BOMAG offers the ECONOMIZER soil stiffness measurement and display system on its large reversible plates. The system is calibrated on the jobsite using a common soil stiffness measurement device, such as a radiation test or load bearing test.
"With each pass, the compaction progress is displayed to the operator. Soft spots or over-compacting is also displayed," Krings explains. This allows for more consistent compaction over the entire work area. "The operator is able to check the compaction target of the complete area he has compacted in the trench, and not just on the random QC measurement spots."
Weber Machine's COMPATROL system is offered on its large plates from 900 to 1,200 lbs. and widths from 18 to 34 in. The system lets the operator know when optimum compaction has been reached based on the material.
"When compacting trenches, it is very important to make sure all the material is compacted to maximum compaction, so there are no voids that can cause failure once the final surface is applied," Bailey emphasizes. "COMPATROL will tell the operator if the material is too hard or too soft, and allows the contractor to control 100% of the compaction job... [It] takes out all of the guesswork and tells you when you are done."