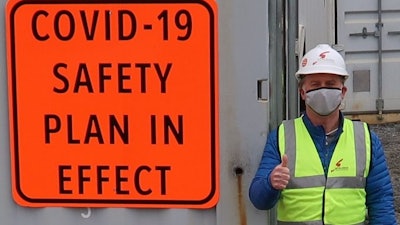
It’s an ambitious goal.
Some may say it’s unattainable.
But Barry Schlouch, president and cofounder of Schlouch Incorporated, has created a safety culture at his civil/heavy highway construction firm that is designed to achieve what many employers have not been able to during this pandemic: keep COVID-19 out of the workplace.
“We want zero COVID-19,” Schlouch says. “Some people will say that’s a little extreme. Well, I don’t think so. What’s wrong with having zero COVID-19? I think it’s a good thing.”
It’s a challenge Schlouch is treating no differently than how the company aims to prevent other hazards.
“We’re not planning our company around how many injuries per day or per week or per month we can tolerate,” he says. “We want zero.”
Because of the high priority the company gives to developing and implementing its construction safety plans, Schlouch Incorporated celebrated zero lost-time injuries last year. Schlouch believes they can do the same with COVID-19.
A Safety Culture Years in the Making
Schlouch is a full-service civil/heavy highway contractor with $80 million in annual revenue. Recent projects include site work for the Lehigh Valley Health Network in Pennsylvania.
The company has 285 employees and about 300 pieces of equipment in its fleet — and still has its first employee from when Schlouch and his wife Deb started the company in 1983, a notable achievement that points to how much Schlouch values his team and the strength of the environment he’s created.
“People say they care about their employees, but really, you don’t care if you don’t work safe,” Schlouch says. “We have an industry that is mixed on safety. There are too many fatalities in this industry, there’s a lot of injuries, and there’s a lot of shortcuts. We just don’t want to be one of them.”
But Schlouch Incorporated’s successful construction safety culture didn’t happen overnight. It has been built with intentional consistency through years of experience.
“I like the book ‘Outliers,’ which talks about putting your 10,000 hours in before you get good at something,” Schlouch says. “I really believe in that.”
It’s a philosophy that Schlouch has relied on throughout his life, from his early days as a construction laborer at age 19 to starting his own company at 25 — in order to meet your goals, you need to purposefully work at it.
“Safety is often baked in as assumed, and it’s not assumed,” Schlouch says. “It is a constant that must be delivered every day, a block-and-tackle effort to really work safe.”
Two years after founding Schlouch Incorporated, he says he had a life-changing experience that permanently affected his views about construction safety.
“Dec. 30, 1985, was one of the worst days of my life,” Schlouch says. “We lost a person on a jobsite.”
He says he’ll never forget going to tell the victim’s family and witnessing their grief.
“His fiancee fell over — she just collapsed to the floor,” Schlouch says. “I made a decision that day that I never wanted to feel that feeling again. When I look back, the accident was preventable. Most accidents are.”
Establishing a Singular Safety Vision
That tragedy sharpened Schlouch’s focus to deliberately develop his firm’s safety culture.
“At our company, we have three main priorities,” he says. “The first priority is the safety of the people. The second priority is the safety of people. The third priority is the safety of the people.
“I keep those three because sometimes priorities can veer off. You can’t veer off when the three are the same. If we fade on priority number one, we go to priority number two, which is the same thing. If we fade on priority number two, we go to priority number three, which is the same thing. It doesn’t matter which priority you go to, we get the same outcome.”
The singular vision is merely the first step, Schlouch says. Creating a positive safety culture requires a strong commitment from the outset — but it’s an investment that pays off, not only for the construction firm’s crews but also for its clients. He says safety goes hand-in-hand with future success.
“What I found is that safety takes mindfulness, thoughtfulness, planning, preparation, process, execution and accountability,” Schlouch says. “When you really get that down, you can do the rest. The mindset of safety paves the way for quality and production.”
Combating the Construction ‘Fatal Five’
It was the beginning of March 2020 when everything changed. Schlouch was getting ready to head to Las Vegas for the Association of Equipment Management Professionals Connect Conference and ConExpo-Con/Agg when he got word that an employee’s wife had been at a hospital in Philadelphia where a doctor was confirmed positive with COVID-19.
Though there was not any evidence that the woman had come in contact with the infected doctor, Schlouch decided to take the proactive measure of quarantining the employee for two weeks.Schlouch added hand washing stations to its jobsites.
“That got us thinking,” he says.
At Schlouch Incorporated, there are 13 professionals who have obtained their Safety Trained Supervisor Construction certification. The STSCs oversee the work sites and the company’s plans to prevent the “Fatal Four” incidents in construction, which include falls, getting struck by an object, electrocution, and getting caught in or between an object. According to OSHA, eliminating the “Fatal Four” incidents would save nearly 600 workers’ lives in the United States every year.
“What our STSCs said is, ‘Barry, we need to design a plan for ‘Fatal Five,’” Schlouch says. “What’s ‘Fatal Five?’ Well, the fifth is COVID-19. We designed safety protocols of how you mitigate and prevent COVID-19 just like you do with a fall, just like you do with the electrical, just like you do with trenching.”
The decision to treat COVID-19 like other major construction safety incidents is instrumental to its prevention, Schlouch says.
“In the hierarchy of controls, the first line of defense is always to eliminate the hazard,” he says. “What you want to do with COVID-19 is you want to keep it off the job or out of the office.”
So how exactly is Schlouch Incorporated tapping into its established safety culture to prevent COVID-19? Here are the seven steps the construction company is taking.
1. Start with Online Training
First, Schlouch Incorporated compiled its newly developed COVID-19 prevention plan into a narrated, 12-minute online training program, based off CDC and OSHA guidance.
All employees must adhere to the company’s safety plan, which includes nearly 30 specific COVID-19 infection control protocols, such as traveling to and from work alone, using electronic communication whenever possible, and changing out of work clothes upon returning home.
Schlouch asks employees to follow nearly 30 specific COVID-19 infection control protocols, including wearing appropriate PPE and sanitizing all equipment touchpoints.
The company has also taken its online training a step further to help families of employees navigate the risks of the pandemic. Schlouch says an eye-opening trip to the store in March made him realize the company’s safety culture was going to need to extend beyond working hours in order to prevent COVID-19.
“I went to the grocery store with my wife, and it was like the wild west,” Schlouch says. “Well, I saw that and then we talked about it, so we decided to do a webinar. We have a whole training program that we did live on a webinar with all the families about how to safely go to the grocery store and return home.”
2. Use an App to Daily Monitor Employee Health
When they come to work each day, Schlouch says all employees — without exception — must begin by completing a health assessment checklist performed by the designated pandemic safety officer assigned to each jobsite and the office. The pandemic safety officer then logs the information into the B2W Inform mobile app that the company uses, and potential risks are communicated immediately to the executive team.
“We caught a few cases that way early on,” Schlouch says. “We had one employee who said, ‘Hey, my dad has symptoms.’ His dad ended up being positive. We quarantined that guy for two weeks, and he was fine. But if you didn’t do that early on, it could creep its way in.”
If an employee is found to be at risk through any of the provided information, the company pays the person to be off during the two weeks of quarantine. This benefit gives employees added incentive to be forthright without fear of negative consequences that could affect their jobs or finances.
“We want them to be honest, so there’s no reason to be dishonest,” Schlouch says. “That’s important too in the whole equation to remove the constraints.”
3. Transform Safety Huddles to Include COVID-19 Prevention
Schlouch crews practice social distancing during safety huddles. Huddles act as a reset button each day to review potential jobsite hazards and COVID-19 prevention information.
“We don’t start a job until we do our safety huddle,” Schlouch says. “We cover all the hazards for the day in the safety huddle, because they change every day. If there’s going to be overhead power lines, underground power lines — whatever we’re doing, we review the plans and the hazards to just bring everybody’s awareness back. It’s a reset button every single morning.”
Schlouch says because that framework was already in place, it was simple to add COVID-19 prevention information into the safety huddles, which now serve as a natural bridge from the daily health assessments in the company’s efforts to keep infections from spreading to their sites.
Crews are also required to wear appropriate PPE and practice social distancing whenever possible, but Schlouch says the key is to not rely on those as primary protective measures.
“PPE is a second line of defense,” he says. “We wear hard hats, but if you don’t have to walk under a cliff where there’s rock laying at the top of the cliff that could roll down and hit you on the head, you don’t need to walk in that section. You want to remove the hazard instead of relying on PPE to take care of the rock that’s going to hit the head. PPE is always the last line of defense.”
4. Ramp Up Sanitation
In early March, Schlouch Incorporated added hand washing stations on all its jobsites, since the CDC recommends doing that over using alcohol-based hand sanitizers.
“It’s a foot pump where you put your foot on the pedal at the bottom and fresh water comes out,” Schlouch says. “There’s soap, and there’s towels.”
In addition to the hand washing stations, crews are provided with sanitizing wipes to clean equipment touchpoints, including controls, handles, and screens.
“They wipe down the equipment in the morning … we wipe it down at the end of the day, and if a mechanic works on the machine, they wipe it down,” Schlouch says.
5. Provide Telemedicine Care
In the case that an employee needs to be quarantined, Schlouch Incorporated has provided its team with access to a healthcare app that offers telemedicine services.
“We think that if they’ve got symptoms, they should have medical attention instead of just being quarantined, because there are things that doctors can help with,” Schlouch says.
He believes it’s important for employees to know they are valued and cared for in a quarantine situation.
“We have a whole process of what they do in those two weeks rather than just go home and feel they’re not wanted at work,” Schlouch says.
6. Re-evaluate and Adjust Work Practices
While there have been many challenging aspects of working with the pandemic, Schlouch says they have also gleaned valuable takeaways that can enhance the company’s ability to succeed in the market.
“We need to look at what we are going to pivot with here,” he says. “We don’t want to lose these opportunities.”
Like many employers during this time, Schlouch Incorporated saw much of its office staff shift to working at home.
“We learned that in some cases it may make sense and be more convenient for employees to be working from home,” Schlouch says. “It could be a recruiting tool that we can start employing people that live further away. We see that we can access more talent at a greater geographic location. Construction field trades are still going to have to go to the job, but secondary support, project managers, accounting people, estimators … I think some of the professional associates can spread our range out geographically and achieve a similar result.”
Online training is another benefit that Schlouch plans to continue beyond the pandemic.
“There’s just a lot of opportunity in online training, and we want to pivot and keep that going forward,” he says.
During the pandemic, the construction industry is increasingly moving its operations online. Streamline your parts procurement by searching for the exact part you need and ordering online at Gearflow.com.
7. Promote Success on Social Media
Once a company has put in the work to create a positive safety culture, Schlouch says then it’s time to spread the word — and one of the best ways to do that is through an active social media presence, such as on LinkedIn.
“We have a huge presence with our families and our employees on social media,” Schlouch says. “It’s a good reinforcer. If Jane or Joe is at work, the spouse sees we’re doing training or recognizing people. Or let’s say Jane or Joe comes home and says ‘I had a crappy day.’ The spouse can say ‘Well, did you talk to Barry? They care about you — we see what they’re doing.’ You get a lot of spousal support when someone’s having a bad day instead of Jane coming home and Joe says, ‘Sounds like you need to find another place to work.’”
Schlouch says the promotion of their safety culture and value of their employees on social media is not only a retention tool, but it also helps attract other family members to join their team.
“I get a lot of children of employees who come work with us,” says Schlouch, whose own daughter, Stayce Rowlands, works with him as the concrete coordinator. “They’re in high school or college, and who are they following [on social media]? They’re following Schlouch. They come out of high school or college, and we get a lot of them.”
The Benefits: A Successful Safety Culture Builds Trust
While creating a positive safety culture requires a significant investment, Schlouch says they’ve seen the payoff during the pandemic. As restrictions ease and construction projects ramp back up, Schlouch says he’s heard from peers that have had a hard time getting crews back to work.
“We’ve had none of that because of the depth of what we’ve done to prepare and work safe,” he says. “The families, the trust is so deep. The employees, the trust is so deep. They were back when we needed them, and they are just working safely, productively and with smiles on their faces.”
That trust speaks volumes. Now that the company is back in a position to hire, it’s attracting the attention of others in the construction industry.
“We have people that then say to me, ‘How do I get on your team? I want to be a part of this. This is the kind of company I’ve been looking for all my life,’” Schlouch says.
Clients are taking notice of this difference in safety culture as well.
“Our clients want what we have on their jobs,” Schlouch says. “They don’t want to be shut down because of positive COVID-19 on their jobsites. And a lot of times that’s what happens. We paved the way for our clients to be safer, and we built more trust with our clients as well. So we have a competitive advantage from that standpoint, because this is what they want.”
These are benefits that will last long after the pandemic has ended, he says.
“I think the companies that can build the trust are the ones that are going to be around,” Schlouch says. “Because people want to go to a place where they feel safe and even more so today than before.”
And as for that lofty goal of zero COVID-19 cases at the workplace?
So far, so good.