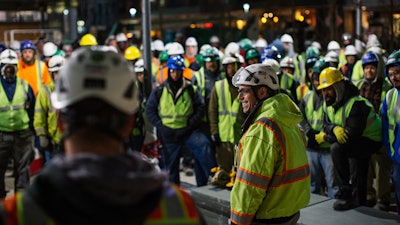
By Gregg Wartgow, Contributing Editor
Construction vies with agriculture for the most-dangerous businesses in the U.S., so it’s common for construction companies to talk about their desire to create a culture of safety. But enacting a safety culture that actually makes construction work safer demands more than making regulatory compliance a priority. And the transformation does not happen overnight.
'Safety culture is about measuring the presence of safety, not the absence of accidents.' says Don Swasing, CEM
“Safety culture is about measuring the presence of safety, not the absence of accidents,” says Don Swasing, CEM, while quoting a respected safety mentor. Swasing is chief operating officer for Schlouch Inc., a Pennsylvania-based site preparation company. “A safety culture is the way in which safety is managed in the workplace. It most often reflects the attitudes, beliefs, perceptions and values employees share as they relate to safety.”
Compliance is the basic component of company’s safety program, but safety culture must go much deeper.
'We don’t view safety as a priority; safety is a core value to us. Priorities often change.' Kris Manning
“We are focused on relationship-based safety,” says Kris Manning, national director of safety and vice president with Clark Construction Group, a commercial building and civil construction services firm with offices and operations across the U.S. “We don’t view safety as a priority; safety is a core value to us. Priorities often change. A core value, on the other hand, represents the foundation of who you are and what you do. Everyone shares this belief at Clark.”Compliance is the basic component of company’s safety program, but safety culture must go much deeper.
In order to create a living safety culture, company leaders must commit to the transformation. A failure (i.e. accident or near miss) can often be used as a catalyst for change.
Driven by the desire to eliminate rollovers, A Schlouch Inc. team meeting. “Leadership must be very open and honest when it comes to safety,” says Don Swasing. “As we’ve transformed our culture, it has been important to celebrate good results. At the same time, when you have a near miss, you have to immediately let everyone know.”
Once the analysis was in, Schlouch leadership told employees of its intention to eliminate rollovers. A specific rollover prevention plan was developed and put into place. “Everyone in the company clearly understood that this was a priority of senior management, and concrete steps were being put in place to address it,” Swasing says.
Schlouch has made great progress over the past several years. They have eliminated heavy equipment and tri-axle-truck rollovers, which was leadership’s original intent. An important milestone, but the quest for a healthy safety culture continues.
“Leadership must be very open and honest when it comes to safety,” Swasing points out. “As we’ve transformed our culture, it has been important to celebrate results as they’ve happened. When we went 100 days without an accident, it was big news. At 200 days, it was bigger news. You have to celebrate the good. At the same time, when you have a near miss, you have to immediately let everyone know.”
Clark Construction Group believes in the concept of celebration as well. “Rewards are instrumental when trying to change behavior,” Manning says. “We often have stand downs where we have breakfast or lunch brought in to celebrate milestones. We’ll issue spot rewards like TVs or tickets to a sporting event. We are excited to reward teams for strong safety performance.”
If a leader shrugs off accidents as a cost of doing business, the culture cannot transform.
An interesting way in which Swasing is helping celebrate safety is through a private Facebook group. Approximately 100 Schlouch employees are part of that closed group. “We share photos and stories, and celebrate safety successes,” Swasing says. “I also send out company-wide emails. These types of things are important if you want to shift away from a compliance-driven culture. The ‘front line’ contributes a tremendous amount of great ideas and examples of what ‘right’ looks like.”
Leaders: accept cold hard truth
In order to get to a place that “looks right” with respect to safety, leadership must first acknowledge the current state of safety in their company. If a leader shrugs off accidents as a cost of doing business, the culture cannot transform. Leadership must decide and communicate what is and isn’t acceptable.
At Schlouch, superintendents and the fleet coordinator assessed their current state of safety. They reported their findings up to the CEO. “It could have been easy to make excuses for our rollovers, i.e. the operator was inexperienced or the underfoot condition was poor,” Swasing says. “But at the end of the day, a lot of our problems had to do with unsafe acts and putting employees and machines into challenging situations.
“You have to be strong because there’s a risk in being honest about your current state,” Swasing continues. “A lot of CEOs do not want to hear that things are messed up. It’s important to give the CEO confidence that you’re going to fix it. Trust is a critical component in cultural change.”
In order to establish the necessary level of trust, leaders have to be “present” out on the jobsite so they can see the hazards and conditions for themselves. “Safety leaders must be credible, respected and inspirational,” Swasing adds. “If they are trying to inspire change, they need to walk the talk every day. At Schlouch, we actually created leadership standards together as a team, published those standards and gave them to everyone in the company.”
Any leaders who do not embrace change threaten the credibility and viability of the safety transformation. It’s possible that they may need to be removed from the team.
Refocus from rituals to attitudes
When trying to distinguish between a culture of safety and a culture of compliance, you must scrutinize what Swasing calls “compliance rituals”. Swasing offers the below example to illustrate.
'We were focused on the wrong things, which we got right every time, but we missed the employee engagement piece completely.' Swasing
“We had a loss control person who went out into the field nine times a year to conduct audits,” Swasing says. “He would look at equipment logs, seatbelt on/off, backup alarms, housekeeping of trailers, etc. Then he submitted his report to me. Guess what? Everything looked great. We were focused on the wrong things, which we got right every time, but we missed the employee engagement piece completely.
“What didn’t make sense was that even though everything always passed audit, our incident rate kept going up,” Swasing continues. “What I discovered was that this ‘ritual’ of the monthly audit was not tied to anything that helped us move the needle to improve safety and hazard elimination. That’s why we hunt for rituals like this today. You must have standards and processes that actually produce results. We don’t have a loss control person doing audits like that anymore. Now he functions as a mentor and safety coach.”
That’s not to say that Schlouch suspended site audits altogether. Rather, senior leaders assumed responsibility for conducting the audits. “We have 13 STSCs (safety trained supervisors in construction) certified by the Board of Certified Safety Professionals,” Swasing points out. “We audit each other’s sites. We’re looking for hazards and corrections, and things in a site foreman’s blind spot. We’re also looking for things employees are doing right—and are recognizing and celebrating them. We then produce a site audit report and distribute it to everyone in the company.”
A Schlouch daily huddle is less ritualistic too. “We used to have a sign-up sheet,” Swasing recalls. “Then someone laid out three or four standard jobsite hazards. Now it’s different. When you first arrive on a jobsite, someone greets you and escorts you from place to place. New employees also get tool and jobsite orientation task training. Everyone always has their PPE on, no questions asked. The daily huddles are more energetic and interactive.”
Tips to help gain employee buy-in
Many construction companies are comfortable in an environment where they simply hold people accountable. For example, if you violate this policy, any number of things could happen, such as getting written up or perhaps even terminated.
Getting to know people on a personal level and fostering an ongoing dialogue around safety are critical to achieving an engaged workforce and strong safety culture.
“Another way for leaders to approach it is to get employees to take ownership of safety themselves, which results in both leadership and frontline employees owning accountability,” Swasing says. “When that happens, leadership can spend most of its time providing support coaching and training resources. That’s exactly what we’ve been able to do at Schlouch.”
Clark Construction Group has stopped believing that safety solely falls on the shoulders of the safety professional on the job. “Safety dovetails between safety and operations,” Manning points out. “It starts with camaraderie on the jobsite and the genuine, shared concern for each other’s safety. It’s a relentless focus on keeping the jobsite clean. Everyone is always focused on what they can do better to help ensure people go home safely at night.”
The “safety first” indoctrination starts on an employee’s first day of employment with Clark. A day-long orientation has a heavy safety emphasis. Shortly after that first day, every employee must do a walk-through of a jobsite with a safety professional. This includes office personnel and estimators. “Everyone in the company must understand what we do on a jobsite,” Manning says. “When an estimator understands, he or she can talk with our trade partners about what we’re trying to do with safety.”
Manning says he likes to use the term safety climate in addition to culture. “When you walk onto one of our jobsites, you can feel a heightened level of expectation and what we hold ourselves accountable for,” he relates.
Clark has a program called Stop, Talk and Accept. All Clark new hires, including office personnel, go on a jobsite walk-through with a safety professional. “Whether you’re a company veteran or its your first week on the job, you have the authority and responsibility to stop anyone on the jobsite who is doing something unsafe,” Manning says. “When it comes to safety, there is no rank.”
The concept of reporting near misses is critically important. Manning is especially interested in what he refers to as leading indicators.
“We ask employees: If something were to go wrong in your area or with your crew, what do you think it would be? Asking those probing questions leads to a candid conversation about what is really going on out in the field. Some employees are taken aback that a general contractor is asking for their opinion. We are always on site, but we can’t be everywhere on the site at one time. Getting to know people on a personal level and fostering an ongoing dialogue around safety are critical to achieving an engaged workforce and strong safety culture. We strive to ensure that every employee on our jobsite gets the same level of respect as senior leadership – and every employee knows that.”
Transforming to a safety culture takes time. Thus, leaders must exhibit patience to allow it to happen.
“There can’t be an undercurrent of fear during a cultural shift like this,” Swasing says. “When you look at your current state, it’s likely that things are going to be pretty screwed up. You can’t start scaring people and firing people. A company has to allow this new approach to settle in. If an employee refuses to get on board six months down the road, that’s a different story. But the current-state assessment is designed to see things for what they are. Identify your low-hanging fruit and biggest risks, take action, and lead the transformation one employee at a time starting from the very top of the company.”
No company is ever 100% perfect. When an incident does occur, Manning says it’s important to refrain from finger pointing. “Our goal is to identify the root cause and contributing factors, and have an open dialogue. We share lessons learned throughout the organization if we feel like others could learn from it,” Manning says.
'As soon as you start blaming your employees, the chance of getting their honest feedback goes away. At the end of the day, all of this rooted in a respect for people.' Manning
The reality is that, in many cases, it’s not an individual who failed; it’s the process. “As soon as you start blaming your employees, the chance of getting their honest feedback and jobsite observations goes away,” Manning says. “At the end of the day, all of this rooted in a respect for people.”Schlouch's safety culture is built around recruiting all employees to continually refine job hazard analyses until incidents end.Schlouch Inc.