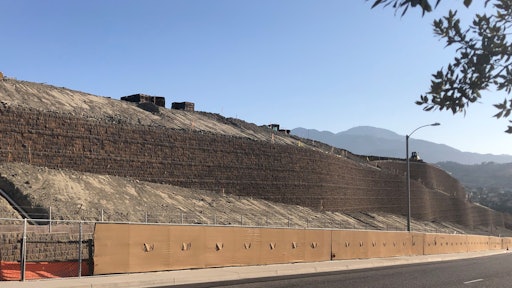
In 2014, California-based developers Baldwin & Sons began the design and development of a housing complex on 99 acres of land in the city of Lake Forest, at the base of the Santa Ana Mountains—it's currently about 2/3 complete. The 931-unit development, The Oaks at Portola Hills, is comprised of seven neighborhoods of both single-family and multi-family residences. It boasts many amenities, including a location in one of the fastest-growing yet safest cities in the state, with nearby restaurants and shops and easy access to interstates. It also sits at the edge of the Limestone Whiting Ranch Wilderness Park, one of Orange County’s largest wilderness preserves.
"Installation of a retaining wall system is an investment in creating more property square footage to build homes on."
-Mike Stevenson, Geogrid Retaining Wall Systems, Inc.
However, developing Portola Hills required converting the site from its natural state of valleys and steep hillsides into acres of construction-ready flat pads. A variety of Belgard Diamond Pro blocks engineered by Anchor Wall Systems as well as Belgard’s Vertica Virtual Joint (VJ) and Planter blocks were chosen to make up the expansive segmental retaining wall system that created the buildable space.
Constructing the Retaining Wall
To design and build the retaining wall, Baldwin & Sons chose to work with Geogrid Retaining Wall Systems, Inc., the largest segmental retaining wall installer in Southern California. Geogrid’s owner, Mike Stevenson, has more than 28 years of experience, including pioneering some retaining wall technologies.
“Geogrid checked all the boxes in terms of the competency of their people, value-engineering, and the products they were going to use. Their previous projects and references also gave us a high comfort level,” says Jose Capati, vice president of land development for Baldwin & Sons. “They were very proactive and responsive from design stage to construction and we are happy with the result of the collaboration.”
The vertical wall batter ratio was 8:1, meaning for every eight feet vertical the wall slanted backwards one foot. This allows an additional 66,5000 sq. ft. of useable land.Belgard Commercial
“There’s not much flat land left in Southern California, and there is a shortage of homes in Orange County, so installation of a retaining wall system is an investment in creating more property square footage to build homes on,” explains Stevenson.
The project was broken into three phases: Portola Northwest, Portola Northeast, and Portola South. While the first two feature single-family homes, the last phase saw the construction of 313 single-family, 256 multi-family, and 58 affordable housing/mixed-use dwellings. Portola North West and Portola South are completed. Phase 1 of Portola North East is substantially completed and Phase 2 is currently being worked on as well, with completion scheduled for December 2023.
Geogrid has an in-house design engineer, Matthew Merritt, P.E., of Red One Engineering, who exclusively designs the segmental retaining walls for their clients. For Portola Hills, the company designed and built walls comprising the entire perimeter of the project to develop “super pads,” acres of flat land for Baldwin to build on.
Many of these walls reached up to 49-ft. tall and 1,000 ft. long.
A Quick Video on Installing a Diamond Pro Pin System
The installer on the proejct was Geogrid Retaining Wall Systems Inc., an innovative leader in the design/build of retaining walls located in Vista, Calif.Belgard Commercial
Challenges
“We were involved with each phase of the project early in the design process and that allowed us to collaborate with the owner, civil engineer, and geotechnical engineer on incorporating the various Belgard wall products into the project,” says Merritt. Weekly project meetings with the project management and engineering team also helped avoid issues during construction.
Among the main concerns for the project initially, according to Capati, were the poor soil quality of the site and the weather.
Early in the project, they started to experience landslides because there were failure planes in the soil being excavated. A failure plane is a weak clay layer that causes instability. These thin layers are like grease which, once exposed, cause landslides as dirt and rock slip over them—especially during significant rainfall. “We worked with the geotechnical engineer on the global stability analysis and incorporating the Mirafi global stability geogrids into the wall design. Portola South had a long (100’+) and very strong geogrid for global stability. Portola NE had two walls incorporated into a large landslide buttress,” says Merritt. “We also worked with a shoring contractor to incorporate the Diamond Pro block facing over the shoring elements.”
Another natural element to contend with was the fact that the project was in a seismic area. In addressing global stability, the team designed a system of secondary geogrids, placed between the standard grid layers. A grid’s length is usually equal to 100% of wall height (i.e., 40 ft. long for a 40-ft.-tall wall). At the Portola site, between every layer of the standard-length grid and compacted fill was another, smaller grid only 4-ft. long. These strata of primary geogrid fabric, compacted fill, secondary grid, compacted fill, and so on provided the necessary additional stability in the seismic area.
There were also design requirements the team had to meet for the project, including the city’s demand that most of the walls be plantable. “For decades now, Southern California has required plantable walls so, over time, what passersby see is vegetation instead of standard concrete,” says Stevenson. Geogrid’s choice of Belgard plantable blocks gave them an advantage over the competition in the bidding process and, ultimately, gave Baldwin & Sons the maximum amount of space on which to build homes.
“The wall batter is a ratio of vertical feet to horizontal feet, so 8:1 means for every eight feet vertical the wall slants backwards one foot so one foot of useable property is lost to the wall batter. The competition at 4:1 loses one foot every four feet of height, or two feet for every eight of height,” explains Merritt. Belgard’s Plantable system features an 8:1 batter.
He adds, “Using the various Belgard products provided the client with an additional 66,500 sq. ft. (1.5 acres) of usable land.” Oftentimes, the difference in wall batter may truly affect the usability of the small back yards of expensive California real estate.
Geogrid designed the plantable walls to go up 4 ft., then back 6 in., then repeated that to achieve the 8:1 batter. Providing plantable space every 4 ft. high, without compromising buildable space, made it likely the vegetation would grow to cover the walls in a shorter amount of time than they would cover an 8-ft. wall. All tall walls over 6-ft. high were plantable.
“We worked with the civil engineer to incorporate the various wall batters into the grading plan and avoid conflicts with the geogrid reinforcement,” adds Merritt.
Belgard Commercial
Deciding on a Color
Geogrid also worked with Sierra Building Products (the manufacturer of the Diamond Pro and Vertica VJ wall products) to develop a custom color block for the project, Belgard’s Toscana blend. The variegated block draws shades of browns and reds from the surrounding soils of the Santa Anas. While the plants were growing in, and after they suffered the effects of 2020’s drought and died off, the color and texture of the wall offered a beautiful façade on its own.
“I have designed with Belgard wall products for over 10 years so I knew I could trust their block on such a large and critical project,” says Merritt. “We used the full line of Belgard products available to us to meet the needs of the owner and requirements of the City of Lake Forest. The result was great looking plantable and non-plantable walls that blend into the site, provide an excellent aesthetic and most importantly provide lasting confidence in their structural capabilities.”
“The fact that Belgard offers so many complementary products that we could use both as vertical and plantable walls was a huge asset,” says Stevenson. “We were installing more than 1,000 square feet of block a day and they were always timely with manufacturing and delivery.” In total, the project utilized Belgard’s Vertica, Vertica Pro Stone Cut Virtual Joint, Diamond Pro Stone Cut, Diamond Pro Stone Cut Virtual Joint, Vertica Cap 8-in., Vertica Cap 4-in. and Belgard Plantable Unit.
Belgard's 18-in. wide by 8-in. tall retaining wall blocks with a combination of 4-in. and 8-in. tall caps included their Vertica, Vertica Pro Stone Cut Virtual Joint, Diamond Pro Stone Cut, Diamond Pro Stone Cut Virtual Joint, Vertica Cap 8-in., Vertica Cap 4-in., and the Belgard Plantable Unit.Belgard Commercial
Now near completion, the Oaks at Portola Hills is a private, gated community atop a hillside offset by the beautiful, Toscana colored retaining walls. It features tree-lined streets and panoramic views. There are outdoor recreational spaces, including neighborhood parks, a five-acre public park and sports fields, and 1.5 miles of walking and hiking trails.
“Everyone is very pleased with the walls’ functionality and how they enhanced the overall aesthetics of our development,” says Capati.
About the author
Michael Vaughn is the Masonry Commercial Brand Manager at Oldcastle APG.