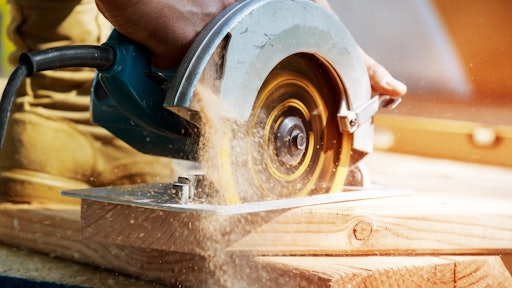
Having the right tools on a jobsite helps ensure job efficiencies, jobsite safety, optimal ergonomics, run times and speed. There are a number of new technologies serving as a driving factor toward that goal.
Trends in Hand Tools
The latest trends in handheld tools include improve digitalization, runtime, and safety in hammer drills, jig saws, pneumatic tools and more.
Another trend in handheld tools is improvements in impact drivers, which are compact, enabling their use in tight spaces. More impact drivers are being designed with comfortable grips, the benefits of which are enhanced when end users establish a correct balance in using the tool.
As these tools evolve, contractors are seeing longer battery life and upgrades to cordless options. Efficient batteries and brushless motors enable longer tool use. Cordless options are offering higher speeds and can save time through conducting high-volume fastening. Other cordless options for hand tools such as hammer drills and jig saws will be the primary offerings of the future and be part of a single-battery platform that includes a wide variety of tools and enable large and small tools to be used at the same time.
Digitalization
Tools and equipment, materials and consumables, and labor are the top three expenditures for construction companies; digital organization helps save money by managing assets. Connected tools can serve to increase efficiencies and provide data that is instructive for workers in getting the job done correctly and on schedule. The value of hand tool digitization is becoming increasingly embraced in the construction sector against the backdrop of studies such as those conducted by the McKinsey Global Institute Industry Digitalization Index indicating that construction is among the least digitized sectors across the globe. That can affect job efficiencies, which in turn can cause projects to go over schedule and affect budgets.
Hand tool digitization also can mitigate challenges related to skilled labor shortages, material costs and enabling a construction company to hold a stake in a competitive environment. One way is through battery technology. Smart batteries provide real-time key intelligence through built-in diagnostics that sync with connected tools to collect data and provide a holistic view of the tools, including location, usage insights, and battery performance levels.
New Tool Technologies Provide Ease of Operation
Milwaukee Tools’ battery-powered MX FUEL system incorporates a push-button start, which serves to eliminate the repetitive motions of a pull start as well as reduce downtime. The system enters the light equipment space designed to take on the same gas and corded equipment that has been depended on for years, but addresses the common hazards and frustrations experienced by light equipment operators on a daily basis, said Kevin Gee, director of product management for Milwaukee Tool.
“Priming, choking, and pulling a gas engine to start is a lengthy and strenuous process Equipment operators also risk flooding the engine and needing to restart the process if done incorrectly. Battery-powered equipment provides instant power,” he said.
Milwaukee Tool has more than 20 solutions in its lineup, enabling the completion of the entire pour-to-finish concrete process as well as providing specialized solutions for the mechanical, electrical, or plumbing user, he added.
“MX FUEL solutions are safer, more reliable, and more productive than gas or corded equipment, eliminating exposure to emissions and tripping hazards without sacrificing the performance needed to get the job done,” Gee said.
In 2021, DEWALT introduced the DEWALT POWERSTACK 20V MAX Compact Battery, which made DEWALT the world’s first major power tool brand to use pouch cell batteries designed for the construction industry. Rather than traditional cylindrical cells, POWERSTACK batteries use pouch cells that are flat and stackable. Pouch cells utilize the space that is otherwise wasted between cylindrical cells, resulting in more stored energy through a more efficient use of the housing, said David Veprek, DEWALT’s vice president of product development.
Veprek noted “innovation in cordless battery cells, electronics, and brushless motors have taken the cordless world where it was in early stages to now where we see entire jobsites going cordless.”
“This helps to reduce the need for temporary power setups, gas generators, air hoses and cords, which can be costly and hazardous on a jobsite,” Veprek said. “This breakthrough technology uses a stack of five pouch cell batteries, which offers less internal impedance, a longer lifespan, and a superior use of space that’s capable of powering a demanding, cordless jobsite.”
The DEWALT POWERSTACK 20V MAX Compact Battery is designed with 50 percent more power, enabling a broad application capabilities and fast performance with cordless tools, he added. The DEWALT POWERSTACK 20v MAX Compact Battery also is 25 percent more compact and 15 percent lighter, designed by DEWALT to provide tool maneuverability, high precision and reduced fatigue when used in tight workspaces, said Veprek.
Veprek said the compact battery also is designed to offer twice the lifespan, “providing the user benefit of more overall investment value.”
Heavy Equipment Integration
Tools, like assets such as heavy iron and vehicles–are becoming more connected to the Internet of Things, which is making it easier to integrate them with broader equipment management systems, pointed out Russ Young, Tenna chief business development officer.
“There are already smart tools available that allow for location tracking, utilization data, and custom use profiles, all of which help improve safety by making sure that the right tools are on site, they are in good working condition, and they are preset for optimum use on different tasks and materials,” Young said. “As AI continues to evolve in safety systems such as camera technology, it’s not hard to imagine that smart tools will start to adapt to this technology, as well.”
Construction Tool Safety
Two timeless key factors in the safe use of construction site tools is choosing the right tool for the job, as well as making sure the tools are in good condition before use, Young noted.
“Equipment management technology is an easy way to help ensure both of those tasks happen,” he added. “For instance, tools can be tagged and grouped with specific equipment, and alerts enabled so key personnel are notified if expected tools are not present on a site. Digital inspections are another great way to make sure a labor crew verifies that all necessary tools are present at the start of a job and that the tools are properly maintained.”
Manufacturers are now incorporating innovative technology-driven safety features into the design of their tools–especially those performing heavy-duty applications–in order to protect against vibration, loss of user control and dust, Veprek pointed out.
“Each are incredibly important and can be contained by choosing tools that are optimized for user safety, without sacrificing performance,” he added. “DEWALT offers a line of PERFORM & PROTECT tools that help mitigate these factors with innovations like built-in vibration reduction systems, clutch reducing technology, and dust shrouds and extractors.”
Milwaukee Tool’s Gee noted that battery-powered equipment eliminates gas and cords from the jobsite and in doing so enhances construction tool safety for equipment operators.
“Enclosed work areas or confined spaces such as tunnels, basements, occupied spaces, or areas shelled off with plastic sheeting become hazardous when operating gas-powered equipment,” he added.
“For example, MX FUEL solutions are powered by MX FUEL REDLITHIUM batteries, which produce less noise and zero emissions for a safer workspace, regardless if working indoors or outdoors.”
Gee noted slips, trips, and falls remain prevalent on the jobsite, especially with corded equipment, which can become tripping hazards and restrict the mobility of the operator.
Battery-powered equipment eliminates the need for corded solutions or extension cords and reduces tripping hazards, prevents breakers from tripping, or the need to have a gas-powered generator on site, he added.
The MX FUEL REDLITHIUM XC406 (XC6.0) battery pack is designed to provide maximum power and runtime for all MX FUEL equipment in a compact profile.
REDLINK Intelligence allows the battery to communicate with MX FUEL equipment in application to optimize performance. This battery pack is designed to deliver fade-free power, running cool even through heavy applications.
The lithium-ion battery is capable of fully charging in 90 minutes. An onboard fuel gauge displays remaining charge. A thick rubber overmold provides protection for the battery if it is dropped. ONE-KEY compatibility enables the end user to track, manage and secure equipment from a mobile device or computer using Bluetooth. Remote lockout capability prevents tampering if the battery is ever lost or stolen.
Construction Tool Maintenance
Tool maintenance best practices focus on “planning the work and working the plan,” said Tenna’s Young.
“Having [preventive] maintenance tracking for everything from cranes to circular saws is the best way to not only make jobsites safer, but also to cut down on unexpected delays for emergency repairs,” he said.
Young recommended these three best practices for construction tool maintenance:
- Have a preventive maintenance plan for each asset and tool.
- Set up digital inspections to have regular visual verification to determine that machines and tools are not showing unexpected wear and tear.
- Use equipment management systems to track utilization data and base preventive maintenance schedules on actual use and not using arbitrary timeframes.
DEWALT’s Veprek recommended for best performance, batteries should be stored in a location that is between 32°F and 104°F.
“Do not store or use the tool or battery pack in locations where the temperature may reach or exceed 104°F (40°C),” he added.
Addressing how equipment is a large investment for a construction company and routine maintenance is one of the most important ways to protect that investment, Gee noted that air filters, carburetors, spark plugs and recoils are examples of a few wearable parts that need to be regularly maintained and managed.
“Additionally, gas-powered products require proper storage and transportation in order to ensure they work properly,” he adds. “The equipment needs to sit upright, keeping the gas where it is supposed to be. For example, if tipped over in the back of the truck, the gas can go in the wrong direction and flood through the system, damaging the product.”
This maintenance can increase the cost of ownership over the lifetime of the product, said Gee.
“Battery-powered equipment eliminates the need for maintenance caused by having a gas engine,” he added. “With no wearable parts that need to be regularly maintained and managed, MX FUEL Equipment requires no gas, oil, or regular engine maintenance, giving users more confidence in their equipment.”
In addition to these industry experts’ recommendations, there are several other factors to consider in construction tool maintenance. Among them:
- Utilizing a proper tool storage system, which serves to prevent damage to tools by ensuring they are secured when not in use, for example. Doing so also improves efficiencies by enabling workers to access tools easily and safely as needed. A clean workspace where tools are stored also serves to increase their longevity and functionality.
- Conduct a quick inspection at the beginning and end of each job for signs of malfunction, wear, or damage. An established maintenance schedule can provide for a more in-depth approach that includes sharpening, calibrating, oiling, and any other best management practices. Record data on use, repairs, and maintenance as to offer a predictive analysis for future needs. Quickly addressing issues prevents accidents and extends tool performance.
- Upgrading or replacing tools that are damaged, have been utilized past their expected life cycle, or no longer meet efficiency or safety standards.
Additional factors to consider in ensuring construction tool safety on the jobsite include:
- Training employees on the proper use of the tools. Such training should encompass education on procedures and guidelines for handling tools, including safety protocols.
- Utilizing the correct PPE while handling tools. That may include wearing glasses, gloves, ear protection and headgear.
- Obtaining the necessary certification required to use certain specialized tools.
- Establishing steps to follow in emergency procedures in the event someone is injured by a tool, including easy access to first aid and stop the bleed kits. Written guidelines and procedures that are easily accessed should be available for employees to reference.
- Engage employees in the process of safe handling of tools and their maintenance. Encourage employees to report any observations about tools that may lead to a more serious issue if not immediately and properly addressed.