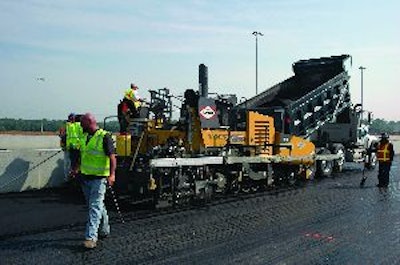
If you?re a race fan, the Lowe?s Motor Speedway (LMS) in Charlotte, NC (actually Concord, NC) probably offers one of the best venues to satisfy your high-octane appetite. And if NASCAR doesn?t quite satisfy your need for speed, the new quarter mile drag strip recently constructed at the speedway facility is sure to fit the bill.
The drag racing facility opened in September with the inaugural NHRA Carolinas Nationals, round 19 of the 24-race NHRA POWERade Drag Racing Series. The dragway is located on 125 acres of LMS property across U.S. Highway 29 from the speedway and adjacent to the LMS dirt track. Initial construction began in January, including a 34,000 square-foot starting-line tower and grandstand structures that will accommodate 30,000 race fans.
The facility?s new drag racing strip, known as zMAX Dragway at Concord, pit areas and midway will cover 46.5 acres, with construction requiring moving 750,000 cubic yards of dirt, placing 65,000 tons of aggregate stone base and paving 50,000 tons of asphalt. Construction crews poured concrete for the four-lane, quarter-mile drag strip in late June. Most drag strips have concrete for the first 660 feet or less, but the transition from concrete to asphalt often upsets the traction of the rear wheels, making the car unstable for drivers as they barrel toward speeds in excess of 300 mph down the 1,320-foot track.
As the only four-lane state-of-the-art drag racing facility in the United States, the drag strip features a pair of two-lane strips located side-by-side. The design will allow racing to continue in the event of an oil-down that requires extensive cleanup to one of the lanes. An oil-down usually halts the action for extended periods and has been a major obstacle for live television coverage.
Beyond the concrete quarter-mile racing surface, only one of two concrete drag racing facilities in the NHRA POWERade Series Circuit, asphalt extends the strip another 2,680 feet. From start to finish, the racing surface is 4,000 feet long, just over three-quarters of a mile. At the end of the asphalt surface is a 200-foot long sandpit.
Paving the shut-down area
Granite began placing the binder base layers of the 2,680-foot-long shut-down lanes the third week of July, and completed its work by the end of July. The shut-down lanes extend from the quarter-mile concrete racing surface another half mile, the distance required to bring the drag racers, traveling 300-plus mph by the time they reach the asphalt, to a safe stop.
Using a Volvo PF6110 tracked paver, Granite placed the rich (5.4 percent) liquid asphalt mix design (Marshall) in three lifts: a 2-inch 19mm binder base course, a 1.5-inch 12.5mm binder course and a 1.25-inch 9.5mm surface course.
With each of the two two-lane strips measuring 60 feet wide, the paving crew staggered the lift width on each of the mats to prevent any longitudinal joints from falling directly in line with the tire travel path of race cars. On the first lift for example, the paving crew set the screed width at 15 feet, following with a 12-foot-wide pull on the second lift and a 15-foot-wide pull on the final surface course.
?We generally use a paver with an 8-foot-wide screed, but on this particular project we used one (the Volvo PF6110) with a 10-foot wide screed,? notes Stephen Cosper, owner of Granite Contracting. ?Due to the tight smoothness specs we had to hit on this job, we thought the tracked paver would provide the most stable working platform to deliver the best results. It was not only important to stagger longitudinal joints on each lift and keep them away from the travel path of the race cars, but also to keep the transition (from concrete to asphalt) of the track as well as the entire surface as smooth as possible. When a car is traveling at over 300 mph coming off the concrete surface onto the asphalt surface, you don?t want to hit any surface deviation.?
Granite Contracting is a full-service contractor providing earthmoving, concrete, utilities, stone base and paving services. With its business comprised of 70 percent commercial and 30 percent state/municipal work, the Concord, NC company expects to generate over $22 million in revenue this year. Fifty percent of the work Granite performs is tied to asphalt paving.
For Cosper and his paving crew, the drag strip project proved to be a good test of their paving skills. Knowing that any slight bump could wreak havoc on a race car driver?s ability to maintain control, paying close attention to the details was critical.
?Since we had the contract to place the stone base under the asphalt, we were able to achieve the correct slope and grade requirements (within +/- ¼ inch) from the very beginning by setting the stone with a laser grading control system,? Cosper says. ?Then with each lift we placed it was simply a matter of making some minor tweaks at the screed to further fine tune the slope and smoothness specs. We had to be particularly careful with the first 200 feet coming off the concrete pad to provide a smooth transition for the racers.?
To make sure the asphalt lined up perfectly level with the concrete at the transition point, Cosper?s crews fabricated steel rails to align the paver screed to the concrete on each mat placed, with each rail corresponding to the various thicknesses of the three lifts.
The paver
The Volvo PF6110 tracked paver the Granite crew used on the project is equipped with an auger system that is independent of the conveyor system. Each of the two auger and conveyor drives uses sonic sensors for more precise handling of material. The paver is powered by a 205-hp Cummins Tier III engine, generating a paving speed of 246 feet per minute. The operator station features a digital display that provides onboard diagnostic capabilities, and the dual control consoles rotate and pivot, as well as extend beyond the edge of the machine for improved visibility.
The technically advanced hydrostatic direct-traction drive system eliminates 70 percent of all mechanical drivetrain components. The continuous and flexible rubber tracks have larger, oscillating bogies that provide optimal ground contact and traction. A Blaw-Kote release agent spray system is integrated into the machine with push-button operation to keep the tracks clean.
The paver used on the drag strip project was equipped with a Volvo Omni 318 screed with front-mounted extensions. The screed is equipped with a variable vibration system for improved performance, reliability and operator control. This vibratory screed is electrically heated.
To achieve density and smoothness, the Granite paving crew used a Volvo DD118HF compactor. The 13.2-ton compactor, with its 78.7-inch wide drums, is a high-frequency machine designed for faster rolling speeds. The machine design provides excellent operator visibility of the material being compacted, and the patented impact spacing meter provides the operator with a visual reference for speed control to maintain proper impact spacing and consistent smoothness. The compactor is also equipped with eccentric rotation that automatically matches direction of travel, which improves smoothness, and SMART drum vibration that starts with the lead drum, then follows with the rear drum to increase compaction efficiency and avoid damage to cold material.
Smooth pull
While Granite placed over 50,000 tons of hot mix on the entire drag strip project, the actual racing portion required just over 8,900 tons: 3,760 tons of binder base course, 2,820 tons of an intermediate binder course and 2,350 tons of the surface mix. Using dual grade controls with a non-contact ski, the Granite crew achieved superior ride smoothness profilograph results on the intermediate and surface mats.
?We started our first pull with a string line and non-contact 30-foot ski and we also constructed grade rails to properly position the screed depth to achieve a smooth transition from the concrete to the asphalt surface,? Cosper says. ?Our first pull was four 15-foot-wide lifts with no longitudinal joints falling in the wheel path. Then we pulled five 12-foot-wide lifts to place the second binder mat. Finally, we pulled four 15-foot-wide surface lifts, again to stagger the longitudinal joints and to make sure those joints didn?t fall directly on the wheel path (where the drivers travel the strip). With each lift we placed we were able to achieve the final grade, slope and smoothness specifications required.?
Pavement smoothness was tested using the California Profilograph method and results on even the base course lift were four-times better than the allowed specifications.