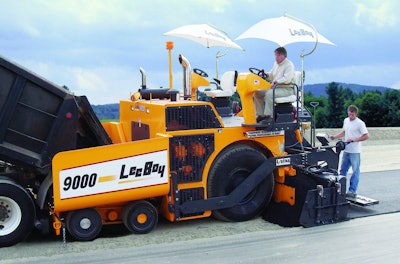
Contractors just beginning to learn hot mix asphalt paving today would recognize machines of 25 years ago but they wouldn't want anything to do with them. That's because of all the equipment used in the road building field, it is the asphalt paver that has evolved the most.
Manufacturers of today's pavers say that pavers of old were louder, hotter, less comfortable, had steel tracks, not as much horsepower, visibility that could have been better, and weren't capable of putting down as much mix as today's machines.
John Hood, Bomag Americas' sales manager for paving and milling products, says that manufacturers have made the greatest strides improving paving equipment over any other equipment simply because of the level paving equipment was at.
"Once the shift from gravity-fed to conveyor-fed machines was made, the conveyor-fed machine ascended to the top of the food chain," Hood says. "The reason is simple: A 59-hp machine will do all the work a paver box did, plus three times as much."
But Hood says that only opened the door for innovation because as commercial pavers moved closer and closer to their high-production highway paving cousins, many of the technologies used on a highway paver could be adapted to the commercial machine.
"There's nothing that's been done on a smaller paver that hasn't been done on a bigger paver," says Brodie Hutchins, Vogele America general manager. "When advancements from the large pavers became affordable for the smaller guy they started being incorporated on commercial machines."
John Sunkenberg, Volvo product competency manager - paving, agrees and adds that many of the improvements in paving overall were driven by the contractor. "It's important to recognize that these innovations were things that came from the customer. These were things they needed," Sunkenberg says. "Many changes are often driven by the contractor, that's why it's important that they voice what they want and what they need. You build a good piece of equipment by listening to your customers."
Power systems drive development
Manufacturers agree that one of the most important innovations in asphalt pavers was in the systems that power the equipment because it was the improvements in those systems that enabled other innovations and improvements to take place.
Hood says that in 1990 when Gilcrest introduced its Model 813 paver (since acquired by Bomag Americas) the paver offered 59 hp. "By 2001 we were at 85 hp and people wanted even more," Hood says. "We all have Tim the Tool Man Syndrome: Give me more power! Today everyone requires high power, high production, and high speed on all pavers. It's just not possible to have too much power."
Hutchins says higher efficiency pumps and motors, combined with advanced electronic designs, have been integrated with control systems, providing more robust and precise operation. Hood adds that the electronics package is cleaner and easier to use and that motors are smaller but can do more work - which he says is a key to many improvements in pavers. The combination of all this has meant a savings to contractors because pavers are now more cost-effective to build. "But more horsepower doesn't just mean more production," Hood says. "It means more production at a higher quality."
Sunkenberg says moving from mechanical systems where the operator made equipment changes (such as bolting on or removing extensions by hand) to a system powered by hydraulics makes the operator's job easier. "Operators are much more capable of making width changes, screed adjustments, crown and slope changes on the fly with the aid of hydraulics or electric motors."
Sunkenberg says that contractors in the field have benefitted greatly from improvements in material transfer - the movement of the mix from the truck to the hopper to the screed and the ends of the screed - which is also largely a result of improved power systems. He credits sonics that control material levels with making it easier for contractors to produce a better finished pavement.
"Power tunnels and hydraulic adjustable augers have given contractors better control of the head of material to the screed, which is of utmost importance to mat quality," Sunkenberg says. "When you start extending the screed out you have relief in front of the screed and the material can fall forward in front of it. In the past you'd use bolt-up steel retention plates to keep the material together and help eliminate segregation, but that's all handled now hydraulically. Today's pavers are much easier to use and enable the contractor to be able to focus on production and quality."
Screed Advances Improve Job Quality
Perhaps nowhere is the effect of improved power systems as obvious as the screed. For years screeds were big and bulky and were heated by gas - usually diesel on highway machines and propane on commercial pavers. Their size and the weight of the screed made them difficult to adjust, they were difficult to heat evenly, and the weight made it difficult to keep the machine in balance. But beginning in the early 1990s a switch to electronically heated screeds enabled contractors to be more productive and more productive at a higher quality.
"One of the game changers for contractors has been electronic screed technology," Hood says. "Commercial pavers no longer have to rely on propane gas to heat the screed as all manufacturers are either putting it on their machines or offering it as an option and contractors are taking full advantage of that."
Ralph Whitley, VT Leeboy vice president of engineering, says propane screeds required a tank on the unit and the tank had to be filled before leaving the yard and then refilled periodically during the day. This slowed production and sometimes had an adverse impact on mat quality.
"Electric heated screeds are powered by a generator that is powered by the paver itself," Whitley says. "No additional fuel sources are required - no volatile gas on site helps keep the job safer as well. They produce a very high-quality mat."
He says screeds now are lighter in weight, which make them easier to adjust and to balance the weight of the machine. "Lighter doesn't always mean better but the lighter material can help keep costs in control," he says.
Hood says electronic screed technology is "green," efficient, repeatable, and consistent. "Electric screeds offer consistent heating and finish," he says. "There are no cold spots on the screed. There's a little more up-front cost but you don't have to buy propane or worry about running out of propane on the job."
Hutchins says the advancements in hydraulics and electronics have taken the complexity out of screeds as most adjustments and operations are now primarily made with the push of a few buttons.
"Screeds are now easier to learn how to operate, and it's easier for a newer guy to learn how to produce a good mat," Whitley says.
Sunkenberg adds that vibration on a screed can be of significant importance for contractors. "Vibration helps material flow beneath the screed and it helps improve the mat texture," he says. "Vibration on a screed also enables contractors to get some density off the screed, which relates to mat performance. There's less compaction differentiation if you have more density off the screed."
Automatic functions ease the work
Automatic functions throughout the paver make it easier to operate the machine more consistently. Some functions, such as automatic tensioning of track and conveyor chains, help extend the life of wear parts. Other automatic functions help in job quality.
Whitley says the integration of computer technology into pavers has played a large role as well. CANBUS, which enables the connecting of electronic control units, has enabled diagnostic systems for maintenance to become standard. On engines, for example, Whitley says computer technology helps manage data from the engine. He says that knowing when and how to manage the engine helps set the pace to manage the other subsystems on the paver. He says computers are also important for diagnostics for maintenance, allowing the user to quickly diagnose problems and to troubleshoot equipment problems quickly.
"Automatic functions are improving job quality because they help the contractor constantly maintain a head of material across the front of the screed," Hood says. "That means there are no voids and no one has to be back there shoveling mix to fill areas in front of the screed."
Hutchins says many automatic features developed for highway class pavers are available for commercial machines. "But many smaller paving operations may not use them because they do not have a need for such sophisticated equipment on the smaller equipment or smaller jobsites," he says, citing grade-and-slope controls as an example.
But when these automated systems such as GPS and noncontact sensors are used accuracy improves. "Many of these features have become very integrated with the paving process and even with the equipment," he says. "These tools enable contractors to achieve high levels of accuracy in terms of profile for the road."
Hutchins says that while using GPS for grade and slope is still new for a lot of paving contractors and is not a standard feature quite yet, GPS for fleet management was accepted more quickly. Contractors can now track the location of a machine, the number of hours on a unit, and performance details such as engine temperature, engine oil level, engine oil pressure, and coolant pressure, and more.
"This allows maintenance managers and contractors the ability to keep an eye on all the units from a distance and know when maintenance or repairs are needed," Hutchins says.
Sunkenberg adds that the use of sonics on the commercial paver, whether for grade-and-slope control or auger-and-material control, is an improvement that has carried over from highway class machines. "Variable auger speed and variable conveyor speed provide a consistent head of material to the screed," he says. "That was more popular on the highway machines but it's working its way to the commercial pavers because the concept is the same: A consistent load of material equates to a consistent mat."
Innovations improve ergonomics & safety
Hood says that just as with other construction equipment, ergonomics and operator comfort have become a big factor in commercial paver developments. "Ergonomics has been a big factor on the highway side and has been filtering down to the commercial paver for years now," he says.
Whitley says that from an ergonomics standpoint a number of improvements in what he calls "the human factors" have made the work easier for the paver operator, including putting all controls within reach of the operator, improving comfort for an operator who is sitting for hours at a time, and reducing vibration to the operator through use of isolation pads.
Sunkenberg says moving from levers to toggle switches, for example, is another payoff of the improved electronics.
"It is more efficient but it's also more ergonomically friendly, particularly for a commercial guy," Sunkenberg says. "Instead of eight levers he's only got to flip switches. This allows for centralized control stations. So the move to toggle switches improved operator ergonomics. And the easier it is to operate the machine, the better the production, the better the paving, and the happier the crews. It all works together to get a better job done."
Hutchins says today's pavers also offer improved visibility, which he says leads to greater operator comfort. He says pavers also are quieter, partly because engines have gotten quieter but also because manufacturers have figured out ways to contain the operating devices within the machine to help eliminate noise through baffling and sound deflection.
"Pavers have come a long way in the last 25 years," Hutchins says.