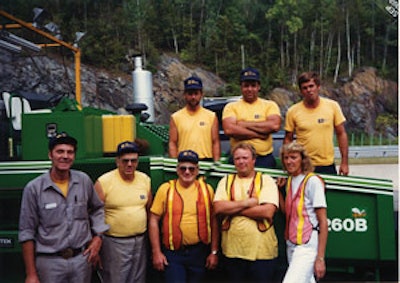
John Ball
In this series, Paving Crew Role Call, paving specialist and National Pavement Expo featured speaker John Ball, Top Quality Paving, will discuss the responsibilities and skills needed for each position on a paving crew. The series will give contractors insights into the skills, type of person, and responsibilities each position requires, and it can also be used to develop job descriptions for an employee manual.
Probably the most knowledgeable person on a paving crew, the foreman has the crucial job of overseeing the entire on-the-job operation while making split-second decisions and keeping lines of communication open among all parties. That's why he's "the negotiator."
The foreman is the contractor's eyes and ears on the job. He's responsible for communicating the client's and contractor's expectations of the job into the field, executing the work so those expectations are met, and balancing often conflicting expectations. He's responsible for communicating with the client in the field, negotiating change orders, maintaining or adjusting schedules, monitoring work locations, tracking delivery schedules from the plant and haul trucks - all while keeping his crew upbeat, productive, and working with an eye on the goal of quality work for a satisfied customer.
Wanted: Experience
It's rare the young or inexperienced worker can handle all that - while knowing the responsibilities of each crew member, how to operate each piece of equipment, and how to get the paving job done.
So the first thing a foreman needs is experience - on the various pieces of equipment, on various paving jobs, with customers, with the office, and with the plant. He has to have a "been there, done that" kind of attitude so he understands what his workers are encountering and what his clients are demanding. And that experience and attitude has to manifest itself in an ability to lead, to command respect, to be the authority on the site, and to be the responsive decision maker. That's why he or she needs to be experienced - and probably a little older.
In "the old days" a foreman would work his way up through the crew until he had enough experience to become foreman. Nowadays that's not necessarily the case as paving companies are placing people they think have foreman potential in foreman jobs. But the best foremen have that mix of experience and education that gives them the authority they need to lead a successful crew.
Common sense is also an asset. Being "book smart" is important, as is knowing and understanding the specifications of each job. But the foreman also has to know how to pave because he's going to direct the paving team on how to do it, where to do it, and what to do it with.
The foreman of the paving team is responsible for achieving a quality, finished product according to the specs in the most cost-
effective manner possible. So he oversees the asphalt lay down operation, and he coordinates jobs among the office, HMA plant, trucking operation, shop, and labs and quarries if necessary so that each day's paving operations run smoothly.
Other valuable skills include:
Delegating responsibility. Because the foreman is responsible for so much it is essential he be good at (or learn to) delegate. This can involve training to make sure the workers are learning what they need to, and it also involves matching the person and his or her abilities to the assignment.
Problem solving. Because of his position and experience the foreman must identify and solve problems in a timely manner. He must be able to gather information from all sources and analyze it skillfully.
While he must know the company's planned response to certain situations, he must be able to develop alternative solutions specific to a job. Because he oversees a crew and often is the contact between the crew and the office, the foreman must be comfortable solving problems in group situations, and he must be able to reason his way to solutions of even the most emotional topics.
Communication skills. Oral and written skills are essential, though these can be developed over time. Oral skills will enable him to manage difficult customer situations and will help him focus on resolving conflict in the field - as opposed to placing blame. Implied in good oral communication skills is the ability to listen to obtain the full picture before asking questions or formulating a plan of action.
Much of oral skills result from experience and authority in the field, which generates respect from workers and customers alike. But it's important to bring workers into the decision-making process, asking opinions and soliciting suggestions about a specific problem or situation. This helps build a positive team spirit, and is most successful when the foreman is able to put the success of the team above his own interests as this builds morale and develops a group commitment toward the company's goals.
Communication with the crew each day is essential so crew members know and understand their specific responsibilities for that day. And by promoting an exchange of information with crew members the foreman might learn something about the job he didn't know, enabling him to set up a safer jobsite or a more productive operation, or even make a change that can make the job more profitable.
Written skills are essential too, because the foreman relates a broad variety of information to the office and shop every day.
Essential job responsibilities
Some of these responsibilities can be delegated to others, but whether a foreman delegates them or handles them himself, he is responsible for these essential aspects of each job:
Participate in the pre-meeting so he and the client know each other and so he can be involved in planning and in solving any customer concerns.
Be aware of production needs and maintain constant contact with the HMA plant. He should have his finger on the pulse of the progress of the job, projected tonnage per day, and any equipment breakdowns. He should periodically monitor yields and overruns to assure the job comes in on or under budget.
Complete a "daily completion report." This provides field information to the office and the shop. Information should include the equipment used on the job, tonnage placed, job status, employees' and their time on the job, problems encountered and how they were resolved, and any communications with the customer. Much of this today is done via laptop or through use of pre-printed forms, but the ability to communicate in writing helps the entire process proceed smoothly.
Keep a "maintenance repair book." The book should be divided into safety repairs and equipment failures, and information should be entered regularly on all equipment. This documentation helps the maintenance shop to plan what to do on which day and know what equipment will or won't be available.
Communicate the job to the crew. Outline how it's going to proceed; ask for any questions, comments or suggestions; and review with the crew what is expected of them at the jobsite. Topics to cover include dress, attitude, and conduct (language, loitering).
This is a great opportunity for the foreman to generate some enthusiasm for the work and some identity with the company. It's also a great time to discuss extending appropriate professional courtesy to others on the job, whether they are coworkers, supervisors, or the customer. Workers should be reminded of their roles on the job; reinforce that they should not be talking with the client if that's not part of their job.
Be aware of jobsite conditions and how they affect the work and the crew. This includes not only setting up traffic control but monitoring changing situations to make sure traffic control setup initially is still effective, monitoring weather via the Internet to make sure none of the work is compromised, and even policing the jobsite at the end of the day. If a site isn't clean and well maintained and a client happens to see it, the image of professionalism is damaged - and the client might complain.
Coordinate with the plant. This needs to take place on a regular basis. The foreman needs to track the amount of mix placed throughout the day so he can double check that against what the plant says it has delivered. This helps keep the job costs in line with the budget and lets the foreman know how much more mix he has left to place before the job is complete. He needs to order mix for the following day usually by 2:00pm or 3:00pm of the current day, and he needs to stay on top of hauling and truck schedules, too. He also needs to let the plant know the expected start and end times for the next day.
Monitor jobsite safety. In addition to establishing traffic control, the foreman must familiarize himself with each piece of equipment, how to run it, and proper safety procedures so he can answer operators' questions, assist in training on equipment, and ensure safe operation.
In addition, the foreman must be familiar with the contractor's own safety policy as outlined in an employee handbook. This includes knowing such information as when hard hats, steel toed shoes, safety masks, and ear plugs are required; when uniforms are required; when safety vests are required; and whether employees are permitted to talk on cell phones at the jobsite.
Every employee that operates a piece of equipment needs to know how to operate that equipment safely, and it's up to the foreman to know that, too.
Walk the job. Some foreman like to stand on the back of the paver and manage the job from there, but the foreman should really be walking the entire site. From the back of the paver he is limited to what he can see and what he can direct. By walking the site while work is ongoing he can oversee and analyze the entire operation, making sure the paving is starting in the correct place, making sure the operator is putting down 21/2 inches and not 3 inches of mix, checking to make sure the rollers are close enough to the paver, and communicating with the haul trucks and the plant.
But don't let this information scare you away from becoming a foreman. All of this is learned, and if you are offered the opportunity to step up and run a crew, take it. If management offers a foreman position they must see something in you they think they can develop. You never know when that opportunity will arise again.
Next issue's installment: Where did the foreman come from?
John Ball is president of Top Quality Paving, P.O. Box 4398, Manchester, NH 03108. Reach him at [email protected] or attend his paving seminars at National Pavement Expo West, Nov. 20-22, Las Vegas, or National Pavement Expo, Feb. 18-21, Charlotte, NC. For more information visit www.nationalpavementexpo.com.