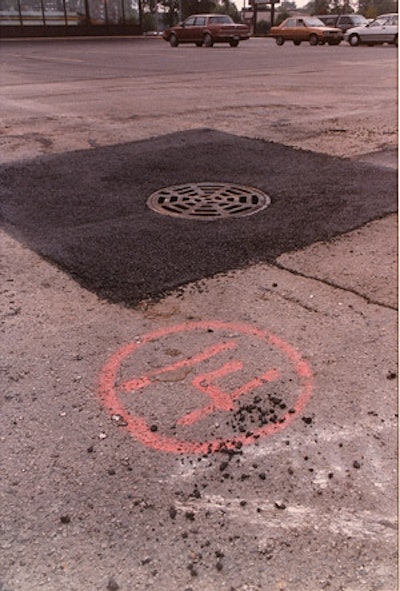
In a best-case scenario contractors offer pavement repair services that add value to their own business while also adding value to their customer's purchase; work is done efficiently to keep production rates up to maximize profit.
Achieving this best-case situation requires a mix of repair options and sales know-how, and it can be enhanced by adding a particular product or even piece of equipment to the contractor's operation. So contractors looking to improve their pavement repair business can use these 11 tips as a starting point.
- Encourage timely maintenance. This is probably the single most-important service contractors can provide their customers. Most property managers work under tight budgetary constraints, so they often have to pick and choose the maintenance that gets done on a given property - or even among several properties. Contractors who are able to rank the seriousness of pavement damage and help the client allocate dollars where they will do the most long-term good are the contractors that will enhance their contractor-client relationships.
As the chart shows, maintenance done early helps the pavement last longer and, over the long haul, will cost your client less. Repairs made at a later date are more extensive, so more costly. Understanding this concept and educating your customers on how best to allocate their resources will go a long way to installing effective, successful pavement repairs.
- Know the plans for each customer. Property managers have different goals - often different goals for each property - so the repairs they need done are affected by those plans. If a manager plans to sell a property in the near future he might not be interested in an expensive overlay or costly removal-and-replacement repairs. On the other hand, a manager who intends to hold and invest in a property for a long term might not want to "waste" money on small aesthetic repairs when he intends to overlay or remove and replace an entire parking lot in a the near future. Knowing this information enables a contractor to provide the best suggestions and make the pavement repairs that will best serve the customer.
- Sell your services as what they are. Maintenance is not repair, so a client looking to improve the integrity of his parking lot pavement should not be considering a sealcoat (at least until after the repairs are made). Pavement marking, sealcoating, and some types of patching are purely maintenance options - valuable, of course, but not if the pavement demands repair first.
- Seal the cracks. This is an essential element of any maintenance operation but crack repair can also be considered pavement repair. Studies by the Federal Highway Administration have determined that not sealing cracks threatens the entire pavement structure as water penetrates, weakening the pavement and the base, and eventually the subbase. If this goes on too long an entire section of pavement becomes damaged, eventually resulting in a complete removal of the section or of the entire parking lot.
It's essential that clients understand why cracks need to be sealed, and once they've agreed it's essential that contractor seal them properly. Whether you rely on a rubberized cold-pour material or a hot pour material, cracks must be properly cleaned and dried before material is added. In many cases routing is necessary to create a stable reservoir to hold the material, but this requires additional of equipment, additional time, and is more expensive. But the result can be longer lasting. In many cases paving fabrics or fabrics designed specifically for cracks can be used to slow reflective cracking in overlays. (See Contractors' Choice, page 32, for information on selecting crack repair equipment.)
- Offer remove-and-replace patching as an option - and then perform the repair properly. While this is a more expensive and time-consuming pavement repair, it is the only type of repair that can solve a problem caused by a weak or soft base or subbase. A properly done remove-and-replace repair will not only rid the pavement of a weak area but enhance the structural integrity of the pavement.
Property managers who don't avail themselves of this repair option because of its cost - and opt instead for a quick-fix solution - need to be made aware that they are throwing good money after bad. Eventually the area will have to be cut out and replaced - or if left unattended long enough the entire pavement will fall into disrepair, requiring construction of an entirely new parking lot. To perform a proper remove and replace repair, which generally extends about 4 in. deep, follow these basic steps:
- Excavate the area to a depth necessary to reach firm support. In many cases this means removing the base and often removing some of the subgrade. Failure to remove all unstable material assures the patch will fail.
- Extend your repair at least 1 foot into the structurally sound pavement surrounding the damaged area.
- Square up the repair, making sure it's rectangular. Some contractors use a jack hammer to cut the edges and square up the hole, but a pavement saw is generally faster and results in a cleaner cut.
- Apply a tack coat to the vertical faces of the cut. This helps the hot mix stick better to the sides of the patch, making the patch stronger by bonding it to the existing pavement.
- Backfill the hole with a dense-graded hot mix or with some of the dry recycled base. If the patch is deep, say 6 in. or more, backfill it in layers, compacting each layer with a vibratory plate before constructing the next layer. Compaction of each layer is essential.
- Install a hot mix asphalt surface layer and compact it flush with the surrounding pavement surface. Do not overfill the patch expecting traffic to compact it.
- Recognize when a remove-and-replace repair is not necessary. In some cases pavement - or the pavement's appearance - can be improved without resorting to a remove-and-replace approach. One method is to use a skin or surface patch, which according to The Asphalt Handbook can be used if the area to be repaired "consists of small hairline cracks, minor surface distortion, or even ravelling."
Usually a skin patch does not require removal of any existing pavement and typically involves installation of hot mix asphalt or possibly chip seal layer over the damaged area.
If hot mix asphalt is used for a skin patch it's best the mix be of a sandy nature (as opposed to a mix comprised of larger aggregate) because the patch must be "feathered" to its edge to provide a smooth transition between the pavement and the patch.
The skin patch process is fairly simple: Clean the pavement, apply a tack coat, place the hot mix asphalt, and compact with either a roller or vibratory plate compactor.
Another approach to skin patches is to use the spray-injection patching machines which also perform these functions.
- Offer a proprietary product for skin patches. In recent years producers have developed repair materials that are thicker and heavier and must be spread by hand. These products, available under a variety of brand names from many material producers, contain fibers and often aggregate and are designed to take the place of a skin patch.
Rob Vance, Vance Brothers, says these types of products are available in both coal tar and asphalt-based versions, and both are generally fortified with some combination of fillers, fibers, and often sand.
"The nice thing about these products is they are relatively inexpensive and although the application is a bit more tedious, most anyone can install the product with a trowel or squeegee," Vance says.
He adds that main drawbacks are temperature sensitivity and slower curing due to weather conditions and size of cracks or patch.
Just as with a skin patch these materials do not improve the structural integrity of the surrounding pavement but can level out irregularities and can slow pavement deterioration by preventing water from reaching into the pavement itself.
In addition, many material producers now offer cold and hot-applied proprietary patching products that can be used to patch small surface areas. Originally designed as pothole repair material, these products have been refined over the years and now often can be used for thinner patches.
- Buy your crew an infrared machine. Initially introduced as a machine to facilitate pothole repair, infrared machines have become equipment that is in its own way as versatile and as cost-effective as the skid steer loader. Infrared machines, available from half a dozen manufacturers in a broad variety of sizes and configurations, can be used to repair utility cuts and potholes, heat joints prior to the next paving pass, smooth out birdbaths and other surface defects, heat pavement for pavement texturing, and apply thermoplastic markings among other things.
The advantage to the contractor is this type of equipment helps get you on and off a job quickly, increasing your productivity and adding to your bottom line. The advantage to the customer is you spend less time on the job disrupting his customers, and the finished pavement you leave behind looks remarkably new and ties in remarkably well with the pavement that surrounds the repair.
Your ability to get on and off the job quickly, leaving behind a flawless pavement repair enhances your reputation and makes it more likely you will be called for a job in the future.
Note: Infrared repair can be used on pavement with a damaged base and subbase but those underlying problems will recur. In those situations repairs should be made initially as if for a full-depth patch with the infrared unit brought in at the end to finish the final layer of hot mix. Or, if the property manager is looking only for cosmetic "repairs" the infrared unit can provide those.
- Stock up on adjustable manhole and catch basin risers. Bringing manholes and catch basins up to grade is a time-consuming, labor-intensive, and costly process that often involves jack hammers, bricks, morter, trowel work, and a skid steer.
But two companies, American Highway Products and East Jordan Iron Works, offer round, square, and rectangular adjustable risers, custom or standard sizes, that enable the contractor to adjust the height of the manhole more quickly and efficiently.
Bob Pushay, product specialist for East Jordan Iron Works, says in most cases contractors placing an overlay mark the locations of the manholes and catch basins and pave right over them. Then they remove the newly placed hot mix, jack hammering a foot or so around the manhole, removing all that new material. They then remove the original casting, install the bricks and morter to raise the casting to surface grade, then replace the original casting and put the manhole cover back. A similar process is followed for catch basins.
"With our adjustable risers contractors can get the street or parking lot opened faster and there's less disruption to traffic," he says. "Each takes only 10 to 20 minutes to install as opposed to 90 minutes to 3 hours for the physical adjustment."
Pushay adds that often contractors must close a section of the road or parking lot while the new concrete cures, which often takes between 12 and 24 hours. He says use of the risers is not limited to overlays, which raise the surface of the pavement.
"They also can be used by sealcoaters or stripers who are on a job and realize the lot has been paved a few times but the catch basins or manholes haven't been adjusted to grade, so now there's a situation where there's a sharp drop that cars and trucks hit and bang their oil pan or cause some other damage to the vehicle," Pushay says. "The contractor can easily solve those problems without tearing anything up. So he not only offers more value to the property manager but he adds another service he can charge for, generating even more income from that one jobsite. It's an easy and profitable add-on for a sealcoater or striper."
- Improve pavement edges. Using a product such as Permaloc's AsphaltEdge, contractors can both improve the appearance of their work and generate additional income by installing edge restraints. AsphaltEdge is an 8-ft.-long L-shaped aluminum restraint 2 inches wide and available in side wall heights ranging from 1 to 4 inches. The restraint can be installed on any base and is constructed with "V" noches so it can even be used on curved pavement. Mix is placed as close to the restraint as possible, then raked to the edge and compacted, the end result being a smooth and long-lasting pavement edge.
- Offer pavement texturing. Regardless of the type of process you choose, pavement texturing can be a valuable add-on service contractors can offer. Obviously not a "repair" or "maintenance" option, creating textured pavement can be added on whenever larger areas are overlaid or completely reconstructed, and depending on the location of the work, even a small area (in front of a mall entryway, for example) could be enhanced by installing a textured pavement surface.
This can also be done with existing pavement, using the handy infrared machine, which can reheat the pavement just enough for it to accept the texturing templates, which are then compacted into the hot mix and removed, leaving the imprinted pattern behind.