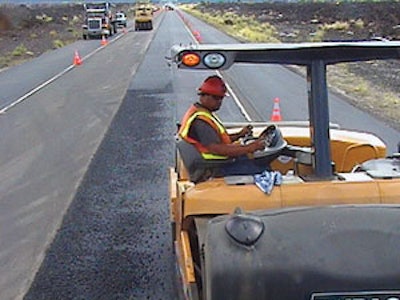
When the National Asphalt Pavement Association heads to The Big Island of Hawaii in February for its 50th Annual Convention, attendees will travel one of the smoothest roads on their way to the convention hotel thanks to the technology and craftsmanship Jas. W. Glover Construction employed in resurfacing a 21.5-mile stretch of the Queen Kaahumanu Highway.
The Hawaii DOT project required profile milling and fresh HMA overlay to achieve an average International Roughness Index of 90 inches per lane mile, with no individual areas of the surface having a deviation (bump or dip) exceeding four-tenths of an inch in 25 feet. Well, Glover not only met the smoothness specification, the asphalt contractor far exceeded the specification with a smoothness rating of well under 60 inches per lane mile.
Prior to beginning work on the project in April, Glover took profile readings of the existing road surface and recorded average IRI smoothness deviations of 180 to 200 inches per lane mile. All the milling crews and paving crews had to do was reduce those deviations by 50 percent in order to qualify for smoothness incentives. But unlike other paving projects, where the contractor would typically put down an intermediate course and a surface course to obtain the smoothest ride possible, this project called for only a 1 1/2-inch surface overlay on the two 12-foot-wide travel lanes. The contractor also had to construct 10-foot-wide shoulder lanes that were used as travel lanes during construction.
Michael Park, paving superintendent for Glover, says that "with only one chance to meet the IRI smoothness specs with an overlay, we had to rely on the milling process to remove most of the existing surface deviations." Hawaii's DOT just implemented the IRI smoothness specifications two years ago, and the Queen Kaahumanu Highway resurfacing project was the first major project that would be put to the test. It was also the largest road project Glover has undertaken, and it required a considerable investment in new equipment to achieve smoothness requirements and the completion deadline of September 1.
Milling operation
Using a Roadtec RX60 milling machine equipped with a Topcon System 5 automated laser leveling device that uses three electric eyes to calculate the average highs and lows of a 50-foot stretch of road surface, Glover's milling crew milled three-quarters of inch off the travel lanes. The crew worked at night, milling approximately three miles and 385 yards of material, which was used to build up the shoulder base of the road. The goal was to stay two to three days ahead of the paving crew.
According to Lucky Harris, milling foreman, equipping the milling machine with leveling automation proved to be the best solution for achieving the smoothness specifications required.
"Since this project did not call for a leveling course, we used our milling operation as the leveling course," Harris says.
Approximately 50 percent of the entire project required full-depth milling due to severe structural deviations in the asphalt. Those sections were done first and replaced with six inches of intermediate HMA course, and then milled with the existing road to achieve a consistent surface. At the end of each overnight shift, crews had to sweep and stripe the milled surface before opening the travel lane back up to morning commuters.
One of the more challenging aspects of the milling operation was to establish a crown in the center of one of the travel lanes in order to accommodate future expansion of the highway. In order to achieve a 1.5 percent slope on the crowned lane, the milling crew had to adjust the seven-foot-wide milling head for each pass down the 12-foot-wide travel lane.
Paving operation
Twenty-four hours after the milling crew completed a three-mile stretch of road, Donald Uchima's paving crew took over. Using a Cedarapids 461 rubber track paver equipped with a Carlson EZ screed and float trackers, Uchima's 10-man crew put down 1,700 to 1,800 tons of HMA a day.
The DOT required a material transfer vehicle to be used on the project and Glover equipped its paving crew with a Roadtec Shuttle Buggy, which proved beneficial in dealing with some of the sporadic trucking problems the paving crew experienced.
Park has tried to keep 30 trucks a day hauling to the project to accommodate both the full-depth reconstruction work and the surface overlay crews. Traffic delays often added to the 30-minute trip from Glover's portable asphalt plant to the actual workzone, so the material transfer vehicle helped to eliminate segregation and maintain a consistent temperature to the mix before it reached the paver.
Uchima used a Hypac 84-inch vibratory roller to generate 3,400 vpms traveling at two to three miles per hour for the breakdown pass and a Hypac 78-inch static roller to finish compaction, with the rolling pattern set up to achieve 94 to 96 percent density.
"We've had to pay close attention to our rolling pattern when working on the travel lane which has the crown to ensure a consistent profile to the slope," Uchima says.
Making the mix
Keeping the paving crew supplied with a consistent quality mix has been the responsibility of Rich Gribbin, quality control manager for Glover. With 30 years of experience in the asphalt business, Gribbin is well-suited for the task and the challenge of designing a mix using porous volcanic aggregate. Gribbin moved to Hawaii from New Jersey, where aggregate has a .5 to .7 absorption rate. The aggregate used in asphalt projects in Hawaii has an average 1.7 absorption rate.
Mixes designed for projects like the Queen Kaahumanu Highway resurfacing project require a richer asphalt cement content to bind the porous volcanic aggregate together when compacted.
"It's like a Superpave mix, but still considered a Marshall mix design, with the DOT specifying the aggregate gradation range and percent of liquid asphalt cement required to achieve stability, flow and air void percentage," Gribbin says. "Other than that, it really doesn't pose any paving or compacting problems. It's like any other mix design used on the mainland."
Glover purchased and set up a CMI/Terex 300-tph counterflow portable drum plant near the construction site. The plant is equipped with four cold-feed bins and two 30,000-gallon AC storage tanks. Gribbin used a PG 64-16 asphalt cement to bind the 5/8-inch, 3/8-inch and fine aggregate for the project.
"The aggregate size gave our crews the ability to achieve a more uniform compaction of the overlay, along with the DOT's required 91 to 96 percent density requirement," Gribbin says.
Gribbin is supported by two quality control technicians, one at the plant monitoring mix production and one at the project taking core samples (approximately five samples for each three-mile section the paving crew put down in a day) and density readings. The field technician also conducts a profile reading at the end of each day to make sure smoothness specifications are still on target.
Many smooth miles ahead
Keeping an eye on all the details required to achieve the DOT's smoothness requirements, Glover's milling and paving crews have been averaging an IRI rating of 20 to 30 inches per lane mile.
"We know we'll collect full incentive if we can keep the IRI smoothness spec below 60 and we've been able to do much better because everybody working on this project is really determined to make this the smoothest road they've ever worked on. We really have a great bunch of guys working on this project," Uchima says.
When paving is complete by the end of summer, Glover's crews will have put down 100,000 tons of some of the smoothest asphalt you'll travel, and the asphalt contractor expects to complete the project three to four weeks ahead of schedule, which could add another $300,000 bonus to the expected smoothness bonus. And you can be sure that once the $10-million resurfacing project is complete, the original road that was constructed in 1972 will provide many years of smooth and reliable service to motorists traveling the Kona side of The Big Island of Hawaii.